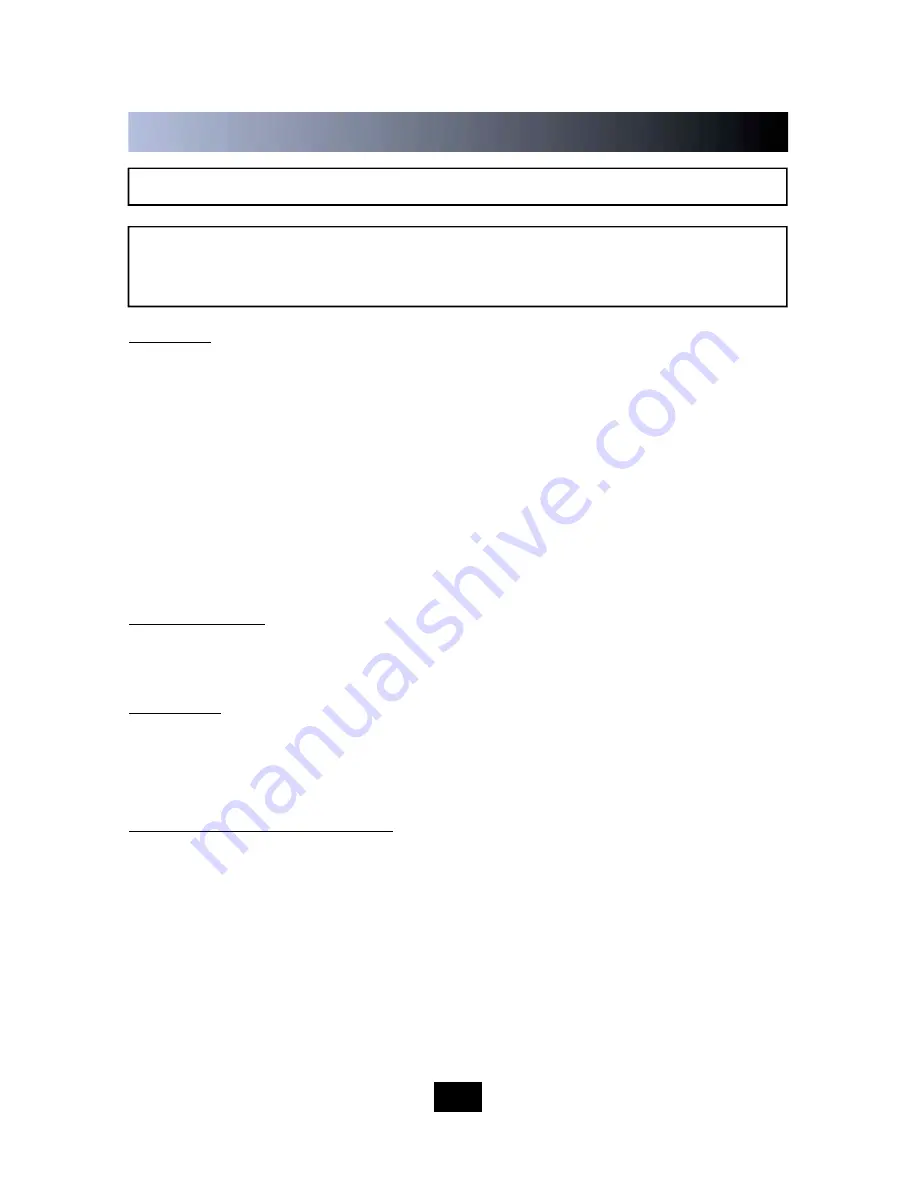
Check external hoses for chafing, rubbing, leakage, or other deterioration and
damage. Tighten all fittings as necessary. Check hydraulic cylinder, cylinder pin and
bolts for signs of wear and fatigue.
Check for any obvious unsafe conditions, such as operator obstructions, in baler
area.
Check oil level in hydraulic reservoir.
Lubricate the door hinge, and mechanical door lock with oil.
Check magnetic interlock on feed gate for proper operation.
Apply a light coating of all purpose grease in the feed gate tracks.
Apply a light application of all purpose oil to the feed gate latch moving parts.
Remove any pieces of materials on top of the platen.
Check functional operation of controls and options (stop button, timers, lights, etc.).
Check hydraulic cylinders, and hoses, for leakage, chafing and wear.
PERIODIC MAINTENANCE
1.
2.
3.
4.
5.
6.
7.
8.
1.
2.
MONTHLY
THREE MONTHS
ANNUAL FILTER MAINTENANCE
ANNUALLY
1.
2.
3.
Replace the hydraulic fluid. See Recommended Oil (page 2-14).
Electric motor bearings should be lubricated once a year.
Clean the top of the power unit to remove the dirt build up.
2-3
WARNING:
BEFORE PERFORMING ANY MAINTENANCE OR SERVICE PROCEDURES ON THE
BALER, MAKE SURE THE BALER IS LOCKED-OUT AND TAGGED-OUT PER THE INSTRUCTIONS
ON PAGE 2-1. FOR MAINTENANCE INSIDE THE BALE CHAMBER, SEE THE PLATEN CHOCKING
PROCEDURE ON PAGE 2-2.
The hydraulic filter should be cleaned at regular annual intervals.
The filter may be removed from the power unit through the cleanout cover in the top
of the reservoir.
Care should be exercised in cleaning the filter to insure that the element is not torn.
Clean the element with a soft brush and standard industrial solvent.
Replace the filter after cleaning and check fittings for tightness. Pump noise and a
"crackle" sound is most often caused by air entering the pump suction line.
Tightening the suction fittings will usually eliminate the problem.
1.
2.
3.
4.
2 MAINTENANCE