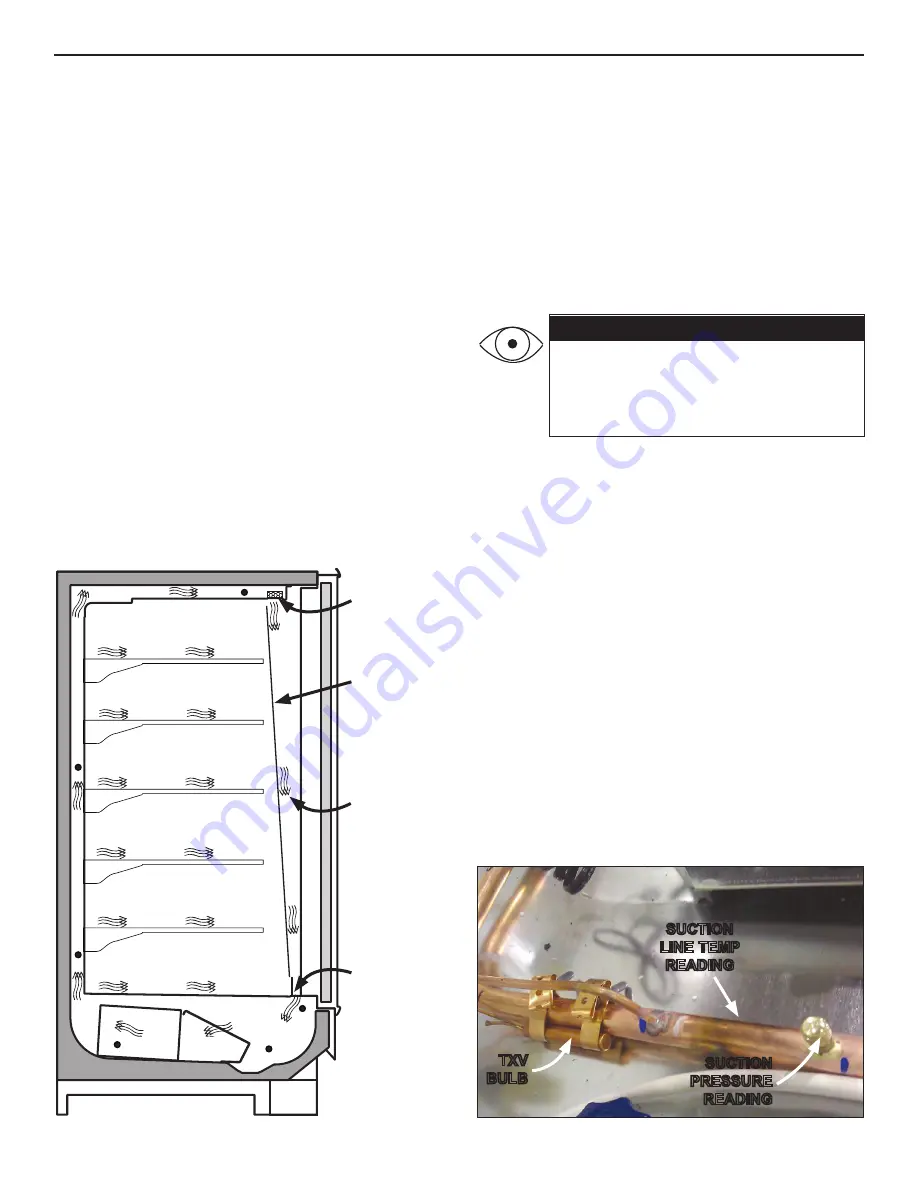
9
Fig. 16 Airflow
RETURN
AIR
DISCHARGE
AIR
LOAD
LIMIT
AIR
FLOW
AIRFLOW & DEFROST
SUCTION
LINE TEMP
READING
TXV
BULB
SUCTION
PRESSURE
READING
Fig. 17 Obtain pressure and temperature readings
AIR FLOW & PRODUCT LOAD
It is important that you do not overload the food product
dis-play so that it impinges on the air flow pattern —
overloading will cause malfunction and the loss of proper
temperature levels, particularly when discharge and return
air sections are covered. Please keep products within the
load limit line shown on the diagram below (Fig.16).
DEFROST & TEMPERATURE CONTROLS
Hillphoenix
low temperature door
cases utilize electric
or
hot gas
defrost
.
All low-temperature reach-in cases have
local defrost controls that terminate defrost cycles in
individual cases, as well as rack-system controls for
circuit termination.
The primary components used for the
defrost cycle are the various defrost termination sensors,
which work to terminate the defrost cycle in the case.
These controls may include 1) a Klixon
®
thermostat, 2) a
sensor probe, or 3) a dial-type thermostat with sensor bulb
(the thermostat will always be mounted with the electrical
con-trols of the case - i.e., in the electrical junction box, in the
electrical raceway, etc.).
If electric defrost is used, the defrost termination
sensor will be
located in a drop tube in the coil or mounted to
the return bend on the coil
. If hot gas defrost is used, the
defrost termination sensor will be mounted to the dump
line—the sensor should always be mounted on the coil-
side of the check
valve or solenoid valve. F
or proper
case operation, the defrost termination sensor must
not be located in the discharge air.
For more detailed information on suggested defrost times
and settings, see
Appendices A–D
. Further adjustments
may be required depending on store conditions.
DETERMINING SUPERHEAT
To identify the correct superheat settings, complete the fol-
lowing steps:
1. Obtain suction pressure from the access port. Obtain
suction line temperature from the area near theTXV
bulb at the outlet of the evaporator coil (Fig. 17).
2. Using the suction pressure reading and the Sporlan
®
temperature-pressure chart (
Appendix F
), convert
pressure-to-temperature.
3. Finally, subtract the converted temperature reading
from the actual temperature reading. The resulting
number is the superheat setting—once this has been
determined, adjust the TXV as needed to obtain the
proper setting.
ATTENTION!
To insure optimal operation of the door
and frame system, a constant 120V sup-
ply be used to power the electrical circuits.
Cycling the input voltage will adversely
impact case performance.
Summary of Contents for Hillphoenix ONRZ
Page 23: ...ELECTRIC DEFROST 1 PHASE E2 ELECTRICAL WIRING ...
Page 24: ...E3 ELECTRIC DEFROST 3 PHASE ELECTRICAL WIRING ...
Page 25: ...E4 ELECTRIC DEFROST HOT GAS ELECTRICAL WIRING ...
Page 31: ...J2 SEISMIC BRACKETS 5 BRACKETS ...
Page 32: ...J3 SEISMIC BRACKETS 7 BRACKETS ...
Page 33: ...J4 SEISMIC BRACKETS 11 BRACKETS ...