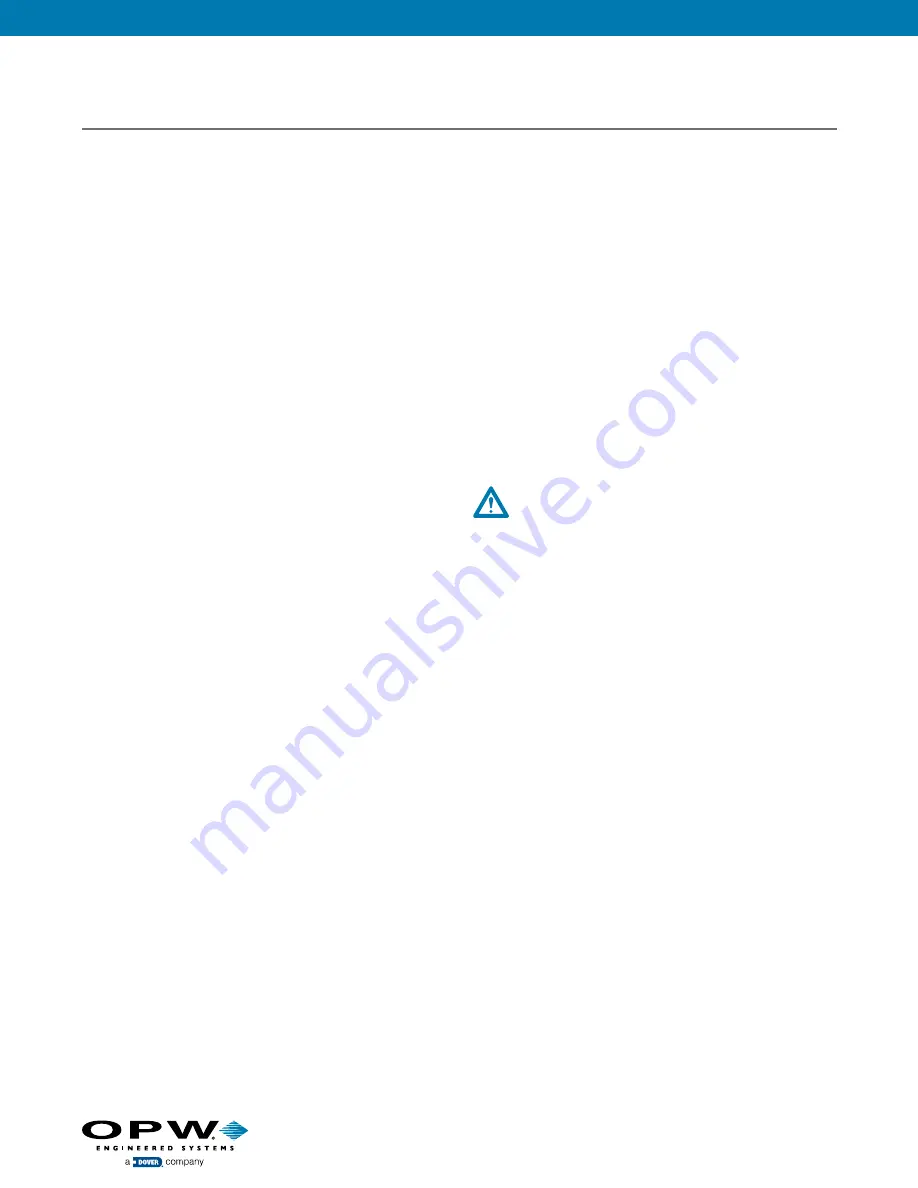
IMPORTANT:
OPW products should be used in compliance with applicable federal, state, provincial, and local laws and regulations. Product selection should be
based on physical specifications and limitations and compatibility with the environment and materials to be handled. OPW MAKES NO WARRANTY OF FITNESS
FOR A PARTICULAR USE. All illustrations and specifications in this literature are based on the latest product information available at the time of publication. OPW
reserves the right to make changes at any time in prices, materials, specifications and models and to discontinue models without notice or obligation.
14
Drylok
®
Dry Disconnect – 1" Coupler Maintenance
4.
When inserting the SHAFT (1) into the BODY (7) and through the
SHAFT LINK (12), the flat on the SHAFT must align with the flat on
the SHAFT LINK. It may be necessary to rotate the SHAFT around to
get these flats aligned. Once aligned, push the SHAFT (1) all the way
into the coupler BODY. You can now turn the SHAFT (1) clockwise
to draw the POPPET (3) into coupler BODY (7) until it is possible
to remove dummy adaptor. Poppet face should be parallel to, and
about .06" below BODY face.
At this point, the flat on the SHAFT (1) should be facing forward
(toward the fixed jaw end of the coupler). The POPPET (3) should be
about .06" below the front face of the coupler, which is basically,
in all the way. Looking in the back (threaded end) of the coupler,
you should see the SHAFT (1) inserted through the SHAFT LINK (12)
and BUSHING (10).
5.
Position the SHAFT (1) so that the groove in the SHAFT is aligned
with GROOVE PIN (17) hole. Install GROOVE PIN (17), smaller end
of the pin first, into coupler BODY (7).ses). With the GROOVE PIN
(9) removed, the RAMP/HANDLE can be lifted off. With the RAMP/
HANDLE (4) removed, WASHER (11) and BEARING/HANDLE (16) can
be removed and discarded. Next, remove GROOVE PIN (17). Take
caution, as stated above when removing this pin.
RAMP/HANDLE RE-INSTALLATION:
1.
With SHAFT (1) reinstalled, place new BEARING, HANDLE (16) over
machine turn of coupler BODY. Install new WASHER (11) over SHAFT
(1) and onto top of coupler BODY.
2
.
While compressing CLAMP (6) by pressing at SPRING, CLAMP (15),
install RAMP/HANDLE (4) over SHAFT (1), aligning the GROOVE
PIN (9) holes. RAMP/HANDLE (4) should be aligned axially with the
coupler BODY, with the handle end towards the threaded end of the
coupler. The top of the CLAMP (6) should be positioned
underneath the RAMP/HANDLE (4).
COUPLER / ADAPTOR INTERFACE ADJUSTMENT:
This interface is critical to proper operation of the Drylok coupler.
Keeping the interface clean and adjusted will help maximize the life of
the coupler poppet seal and will reduce the chance of leaks developing
at the coupler / adaptor interface.
1.
Couple coupler and adaptor together and open to first button lock,
as per operation instructions.
2.
Look at the interface where the coupler face contacts adaptor.
This is viewable on either side of the coupler, in a radial location
between the fixed and movable jaws of the coupler. There should be
no gap at all between the coupler and adaptor. For a positive check,
you should not be able to insert a .002" (or larger) feeler gage
between the coupler and adaptor faces when coupled.
3.
If a gap exists, you can close it by a simple adjustment that is locat-
ed on the movable jaw (CLAMP (6)) near the handle. Loosen JAM
NUT (14) and tighten the slotted SAFETY ADJUSTOR SCREW (23)
until the gap between the coupler and adaptor closes (approximate-
ly 6 inch-pounds of torque). Retighten JAM NUT (14) while holding
the SAFETY ADJUSTOR SCREW (23) in its adjusted position.
WARNING
Do not forget to retighten JAM NUT (14)
over the SAFETY ADJUSTOR SCREW (23).
TEST PROCEDURE:
It is recommended that the VALVE be pressure tested utilizing the air
under water method, checking for leaks in the area of the O-RING,
POPPET (8) and O-RING, SHAFT (20). Place coupler under water, tapping
and rotating it to release any trapped air. Pressurize the valve to 2 PSI,
and check inspection points. Then, increase pressure to 80 PSI and
check inspection points again. Check for leaks in the following areas:
A) RAMP/HANDLE (4)
B) POPPET/COUPLER interface (place coupler
with POPPET face up and pour water on it).
Reduce air pressure to 0 PSI. Insert Drylok test fixture into coupler.
NOTE:
The Drylok test fixture is a fully operational, leak-proof adaptor,
fitted with a nipple and cap. Adjust coupler/adaptor interface as stated
above. Depress SAFETY RELEASE BUTTON (22) and open coupler to
first button lock. Check for interface gaps and adjust as required. Fully
open coupler and pressurize to 2 PSI. Check for leaks at the inspection
points listed above. Also check for leaks at the coupler/adaptor interface.
Increase pressure to 80 PSI and check for leaks again. If leaks occur at
coupler/adaptor interface, retighten adjusting screw as stated above
and retest.
1" DRYLOK COUPLERS 5770 SERIES: