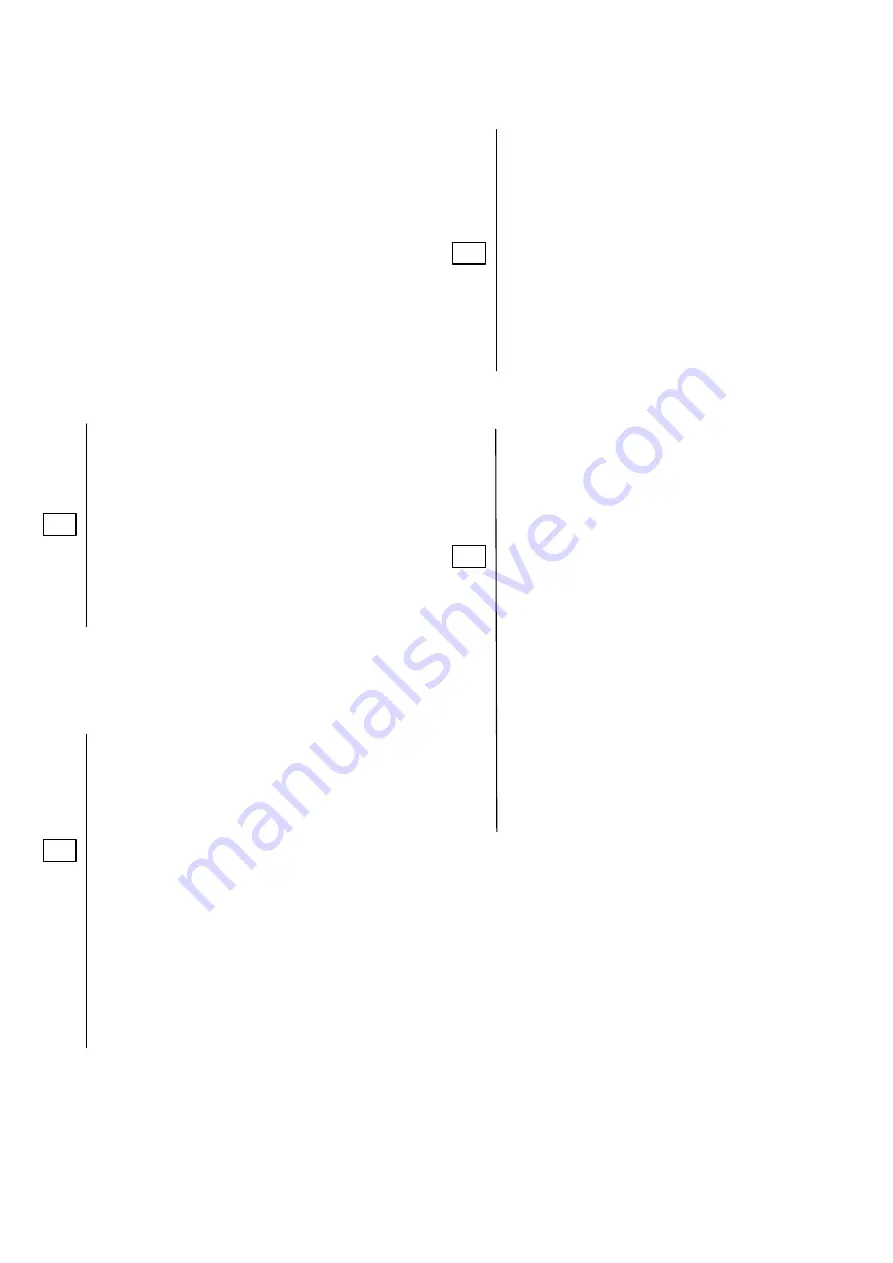
VII - 4
VII - 3. REMOVING REINSTALLING THE
LIQUID END AND THE LIQUID END
MOUNTING ASSEMBLY
(Figure 7.2
e - 7.2
f)
C1. Removing the diaphragm
1. Undo the screws [47]. Remove the liquid end [46].
2. Set the stroke adjustment knob to « 100 % ».
3. Remove the motor casing and rotate the motor by
hand in order to place the diaphragm [45] in the
« front » position.
4. Hold the outer edge of the diaphragm and turn it
anticlockwise in order to unscrew it. Remove the
diaphragm equipped with its support [44].
5. Where applicable, remove the diaphragm seat [49].
D1. Removing the secondary diaphragm
1. Disconnect the terminal box wires, and mark their
connection.
2. Remove the attaching hardware securing the pump
onto its frame.
3. Tilt the pump onto the opposite side of liquid end
(with the secondary diaphragm on top).
4. Undo the screws [43] and remove the spacer [42].
5. Remove the secondary diaphragm [41] and mark the
direction of fitting.
6. If this servicing is required owing to a lubricating oil
leak or in the context of work on the mechanical
assembly, carefully drain the housing and leave it to
drip for about half an hour. Wear protective gloves
to avoid any risk of being burned by hot oil.
Note
: It is advisable to replace the secondary diaphragm in
the course of servicing operation.
D1. Removing the secondary diaphragm
1. Disconnect the terminal box wires, and mark their
connection.
2. Remove the attaching hardware securing the pump
onto its frame.
3. Tilt the pump onto the opposite side of liquid end
(with the secondary diaphragm on top).
4 Unscrew the attaching screw [50] and remove the
diapram seat [49]
5. Remove the retaining ring [35], the washer [33] and
the spring [34]
6 Unscrew the attaching screw [43] and remove the
spacer [42]
7 Unscrew the diaphragm spacer [32] and remove the
stud [[30]
8. Remove the secondary diaphragm [41] and mark the
direction of fitting.
9. If this servicing is required owing to a lubricating oil
leak or in the context of work on the mechanical
assembly, carefully drain the housing and leave it to
drip for about half an hour. Wear protective gloves
to avoid any risk of being burned by hot oil.
D2. Reinstalling the secondary diaphragm
1. If the housing was drained, refill it (see Chapter VIII -
4. LUBRICATION), with the pump being laid onto
the opposite side of liquid end. Remove any
overflow oil immediately with a degreasing agent
suitable for the operating conditions.
2. Position the secondary diaphragm [41] in compliance
with the direction of fitting.
3. Position the spacer [42], placing the detection port [9]
(Fig. 1.2a) facing downwards (with the pump in the
operating position) and tighten the screws [43]
(applying a torque of 3 m.N)
4. Reinstall the diaphragm (see Section C2)
5. Tilt the pump and secure it onto its support.
6. Connect up the motor in compliance with the
directions marked during dismantling (see also
Chapter II -5. ELECTRICAL INSTALLATION).
D2. Reinstalling the secondary diaphragm
1. If the housing was drained, refill it (see Chapter VIII -
4. LUBRICATION), with the pump being laid onto
the opposite side of liquid end. Remove any
overflow oil immediately with a degreasing agent
suitable for the operating conditions.
2. Screw the stud [30] fully home in the connecting rod
3. Position the secondary diaphragm [41] in compliance
with the direction of fitting.
4. Position the spacer [42], placing the detection port [9]
(Fig. 1.2a) facing downwards (with the pump in the
operating position) and tighten the screws [43]
(applying a torque of 3 m.N)
5. Screw the diapragm spacer [32] (torque 0.15 m.daN).
Place the washer [33], the spring [34] (caution the
spring must be introduice by the most bigger
diameter), a washer [33] and the retaining ring [35].(
Use the special tooling available at the spare parts
department)
6 Place the diaphragm seat [49] placing the detection
port [9] (Fig. 1.2a) facing downwards and tighten the
screws [50] ( torque of 2.5 m.N)
7. Reinstall the diaphragm (see section C2).
8. Tilt the pump and attach it onto its support.
9. Connect up the motor in compliance with the
directions marked during dismantling (see also
Chapter II -5. ELECTRICAL INSTALLATION).
C2. Reinstalling the diaphragm
1. Where applicable, position the diaphragm seat [49]
on the spacer [42].
2. Screw the diaphragm [45] fully home.
3. Rotate the motor by hand in order to place the
diaphragm in the « back » position.
4. Position the liquid end [46] on the diaphragm and
attach it by tightening the screws [47] evenly.
Tighten to a torque of 3m.N).
5. Fit the motor casing.
6. Set the stroke adjustment knob to « 0 % ».
A2. Restarting
1. Connect up the pump hydraulically.
2. Check that the capacity is set to « 0% ».
3. Check that there are no suspicious noises when
starting up.
4. Set the pump capacity to « 100 % » to obtain quicker
priming.
5. After priming, set the pump to the desired capacity
and lock the stroke adjustment knob.
A
B
A
B
Summary of Contents for G A Series
Page 2: ......