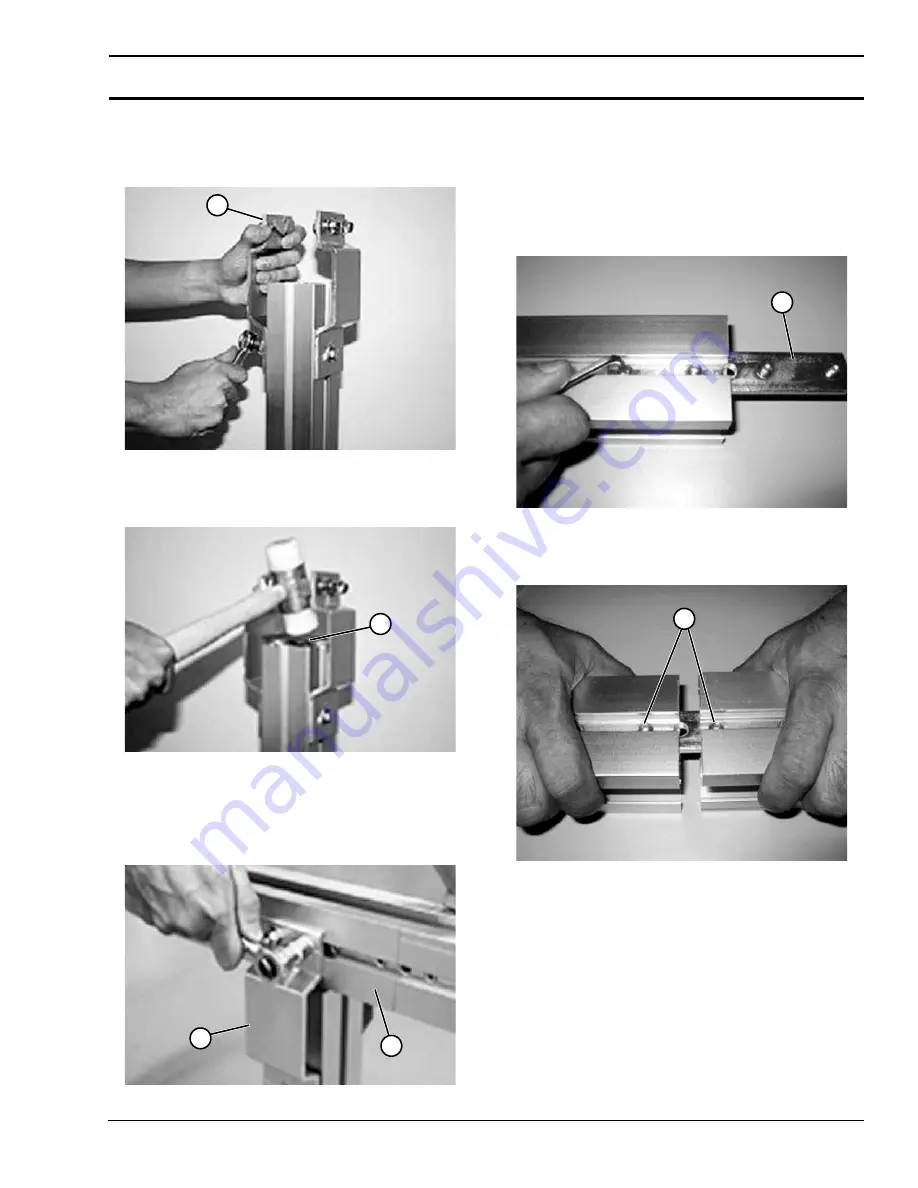
851-899 Rev. A
13
Dorner Mfg. Corp.
FlexMove FC (105 mm) Conveyor System
Installation
2. Insert the square nuts of the second support bracket
into the support beam T-slots. Slide
the bracket down so that it does not protrude above the
cross-section of the beam.
Figure 18
Figure 18
3. Use a soft hammer or mallet to mount an end cap
on to the support beam.
Figure 19
Figure 19
4. Mount the first support bracket
to
. Pull the second
bracket up and insert the T-bolts into the conveyor beam
T-slot. Tighten the nuts.
Figure 20
Figure 20
Conveyor Beam Installation
The next step is to connect conveyor beams – straight
sections and bends – to each other. Connect all conveyor
beams according to the instructions below.
1. Connect two conveyor beam ends by inserting
connecting strips
into the beam
inner T-slots. Use two connecting strips per beam joint.
Figure 21
Figure 21
2. Make sure that the set screws
do not
prevent the connection strips from sliding into place.
Figure 22
Figure 22
1
1
1
2
1
1