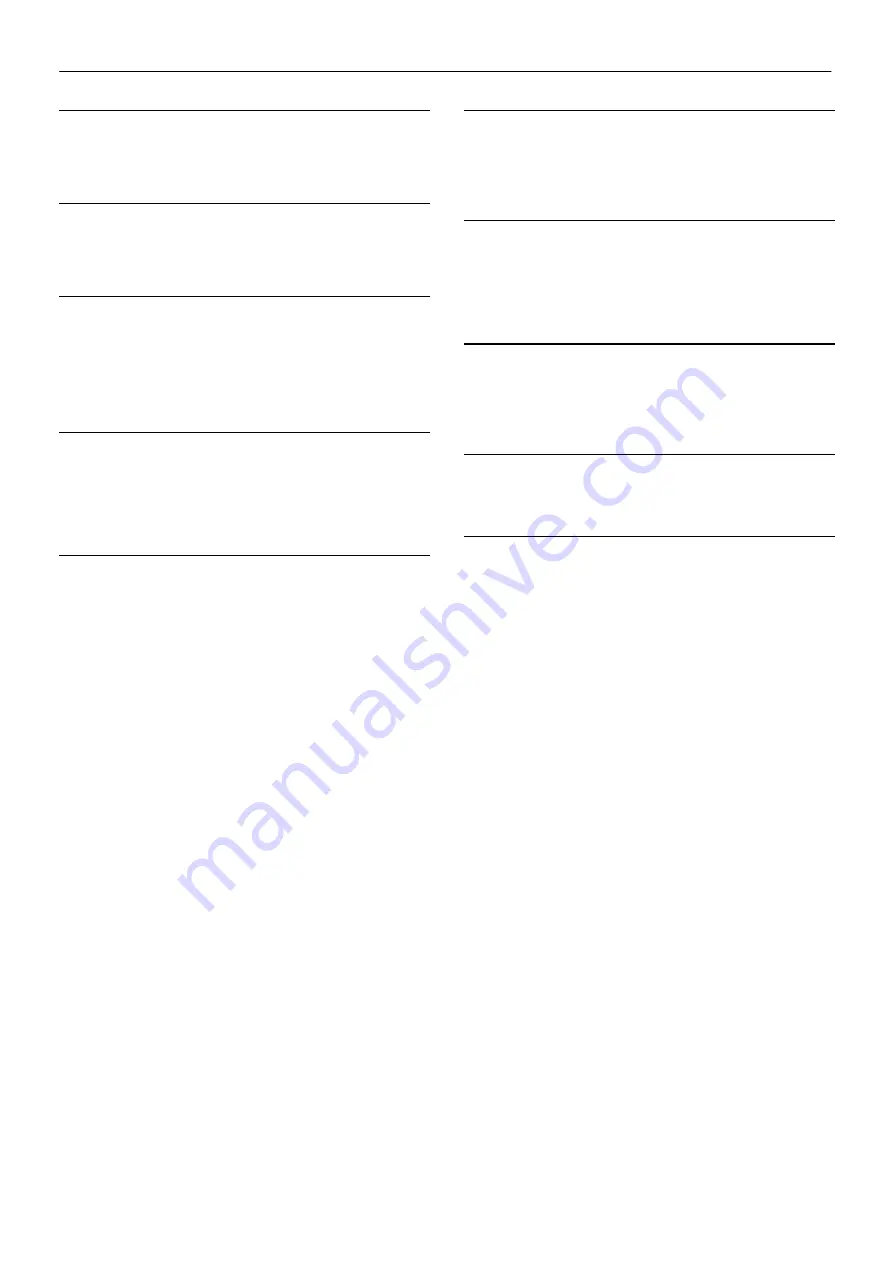
19
NOISE EMISSION
7/20, P65
A. COMPRESSED AIR LEAKS
Correct all compressed air leaks during the first shutdown period
after discovery. If severe enough to cause serious noise problems and
efficiency loss, shut down immediately and correct the leak(s).
B. SAFETY AND CONTROL SYSTEMS
Repair or replace all safety and control systems or circuits as
malfunction occurs. No compressor should be operated with
either
system bypassed, disabled, or nonfunctional.
C. ACOUSTIC MATERIALS
In daily inspections, observe these materials. Maintain all
acoustic material as nearly as possible in its original condition. Repair
or replace all sections that have: 1) sustained damage, 2) have partially
separated from panels to which they were attached, 3) are missing, or
have otherwise deteriorated due to severe operating or storage
conditions.
D. FASTENERS
All fasteners such as hinges, nuts, bolts, clamps, screws, rivets
and latches should be inspected for looseness after each 100 hours of
operation. They should be retightened, repaired, or
−
if missing
−
replaced immediately to prevent subsequent damage and noise
emission increase.
E. ENCLOSURE PANELS
Enclosure panels should also be inspected at 100 hour
operational intervals. All panels that are warped, punctured, torn, or
otherwise deformed, such that their noise containment function is
reduced, should be repaired or replaced before the next operation
interval. Doors, access panels, and hatch closures especially, should
be checked and adjusted at this time to insure continuous sealing
between gasket or acoustic material and the mating frame.
F. AIR INTAKE AND ENGINE EXHAUST
Engine and compressor air intake and engine exhaust systems
should be inspected after each 100 hours of operation for loose,
damaged, or deteriorated components. Repairs or replacements
should be made before the next period of use.
G. COOLING SYSTEMS
All components of the cooling systems for engine water and
compressor oil should be inspected every 250 hours of use. Any
discrepancies found should be corrected before placing the unit back
in operation. Unrestricted airflow over the radiator and oil cooler must
be maintained at all times during operation.
H. ISOLATION MOUNTS
Engine/airend isolation mounts should be inspected after each
250 hours of operation. Those mounts with cracks or splits in the
molded rubber, or with bent or broken bolts due to operation or storage
in severe environments, all should be replaced with equivalent parts.
I. ENGINE OPERATION
Inspect and maintain engine condition and operation as
recommended in the manuals supplied by the engine manufacturer.
J. FUELS AND LUBRICANTS
Use only the types and grades of fuels and lubricants
recommended in the Ingersoll
−
Rand Company and Engine
Manufacturer’s Operator and Maintenance Manuals.