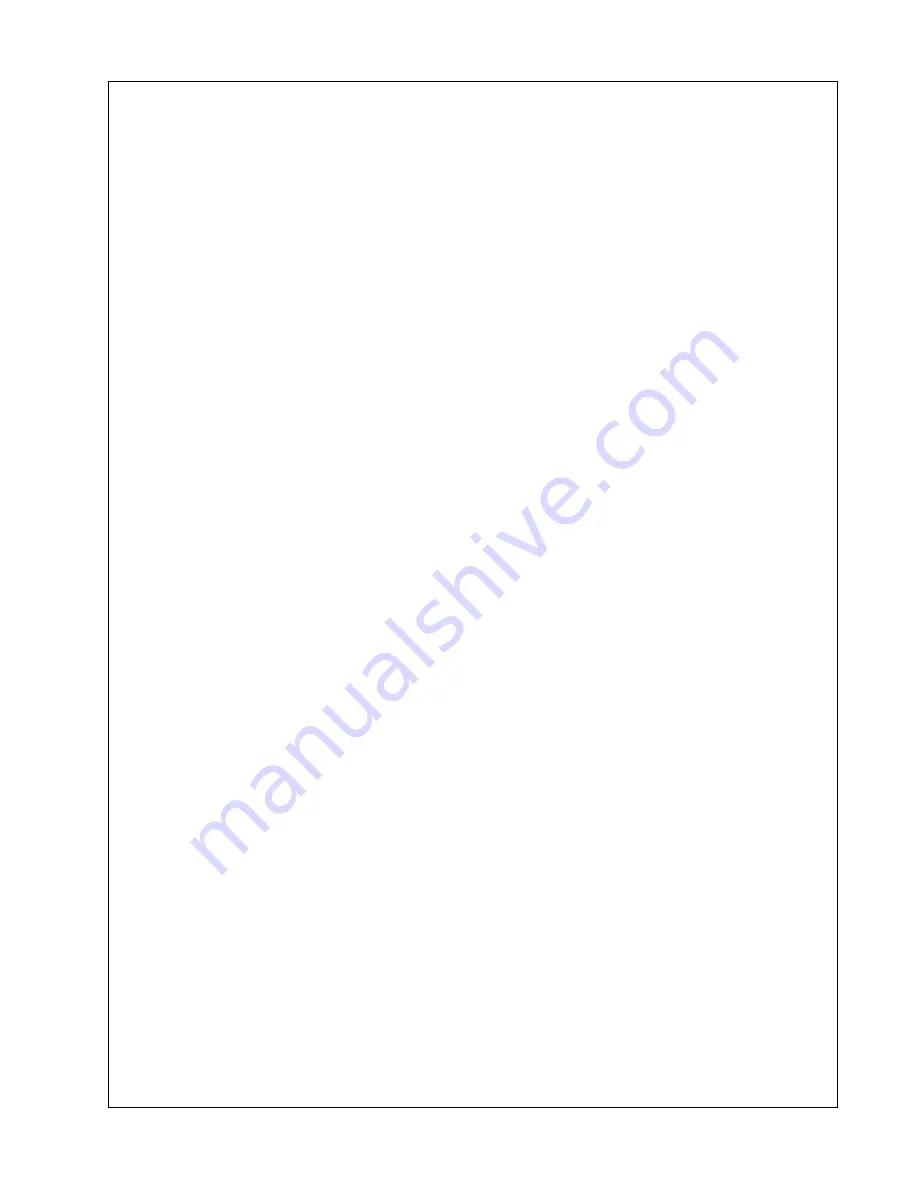
Electrical
Operating & Maintenance Manual
85
Sensors and Transducers
The electronics system contains sensors and transducers that are used to collect process data
from the compressor. The temperature is measured by a thermistor. This device exhibits a
change in resistance as the temperature changes. The resistance causes an input voltage
change to the WEDGE controller input and is interpreted as a temperature change.
The electronics system also uses pressure transducers to measure process pressure
changes. These devices have an output signal of .45V DC to 4.5V DC, corresponding to 0 psi
and the maximum measured psi for a particular device. The maximum pressure transducer
ranges are 100 or 225 psi. The 100 and 225 psi devices are gauge pressure devices. These
transducers are provided with 5V DC excitation to power the device. These are three wire
devices: excitation, signal and ground (return) connections.
Digital Inputs and Outputs
The WEDGE controller scans digital inputs such as switch contacts. These are either “ON”
(24V DC) or “OFF” (0 V DC). These digital inputs are connected to switches within the package
such as the key start switch, air filter switches and IQ filter switches.
The WEDGE controller provides 24V DC digital outputs to control solenoids, start compressor
and DC heaters. These are 24V DC “ON” and 0V DC “OFF”. They are current limited and short
circuit protected.
Controller Outputs:
The WEDGE controller has three different types of outputs: frequency, pulse width modulated
(PWM) and 24V DC digital (ON/OFF). The frequency output is used as a throttle signal for the
engine.
The PWM signal is used as a throttle signal for the Caterpillar engine. It has a base frequency
of 500 Hz and the duty cycle varies from 10% to 90%.
Pressure Control
The discharge pressure is controlled by manipulating the engine speed and compressor inlet
valve position. The inlet valve position is controlled pneumatically and the engine speed is
determined by the WEDGE controller. The WEDGE measures the pneumatic system
regulation pressure and computes an engine throttle setting. This throttle setting is sent to the
engine via the frequency throttle, PWM or J1939 throttle, depending on which technique is
used. The engine controller will control engine speed to this throttle setting.
Summary of Contents for 10/370
Page 2: ...2...
Page 6: ...6...
Page 7: ...7 Foreword...
Page 8: ...Operating Maintenance Manual Foreword 8 Add in PDF Page for CE Mark...
Page 11: ...11 Safety...
Page 19: ...Safety Operating Maintenance Manual 19...
Page 20: ...Operating Maintenance Manual Safety 20...
Page 21: ...Safety Operating Maintenance Manual 21...
Page 23: ...Safety Operating Maintenance Manual 23...
Page 26: ...Operating Maintenance Manual Safety 26...
Page 27: ...27 Noise Emission...
Page 33: ...33 General Data...
Page 36: ...36...
Page 37: ...37 Operating Instructions...
Page 52: ...52...
Page 53: ...53 Maintenance...
Page 66: ...66...
Page 67: ...67 Lubrication...
Page 71: ...71 Troubleshooting...
Page 82: ...82...
Page 83: ...83 Electrical...
Page 88: ...88...
Page 89: ...89 Electrical Schematics...
Page 90: ...Operating Maintenance Manual Electrical Schematics 90...
Page 91: ...Electrical Schematics Operating Maintenance Manual 91...
Page 92: ...Operating Maintenance Manual Electrical Schematics 92...
Page 93: ...Electrical Schematics Operating Maintenance Manual 93...
Page 94: ...94...