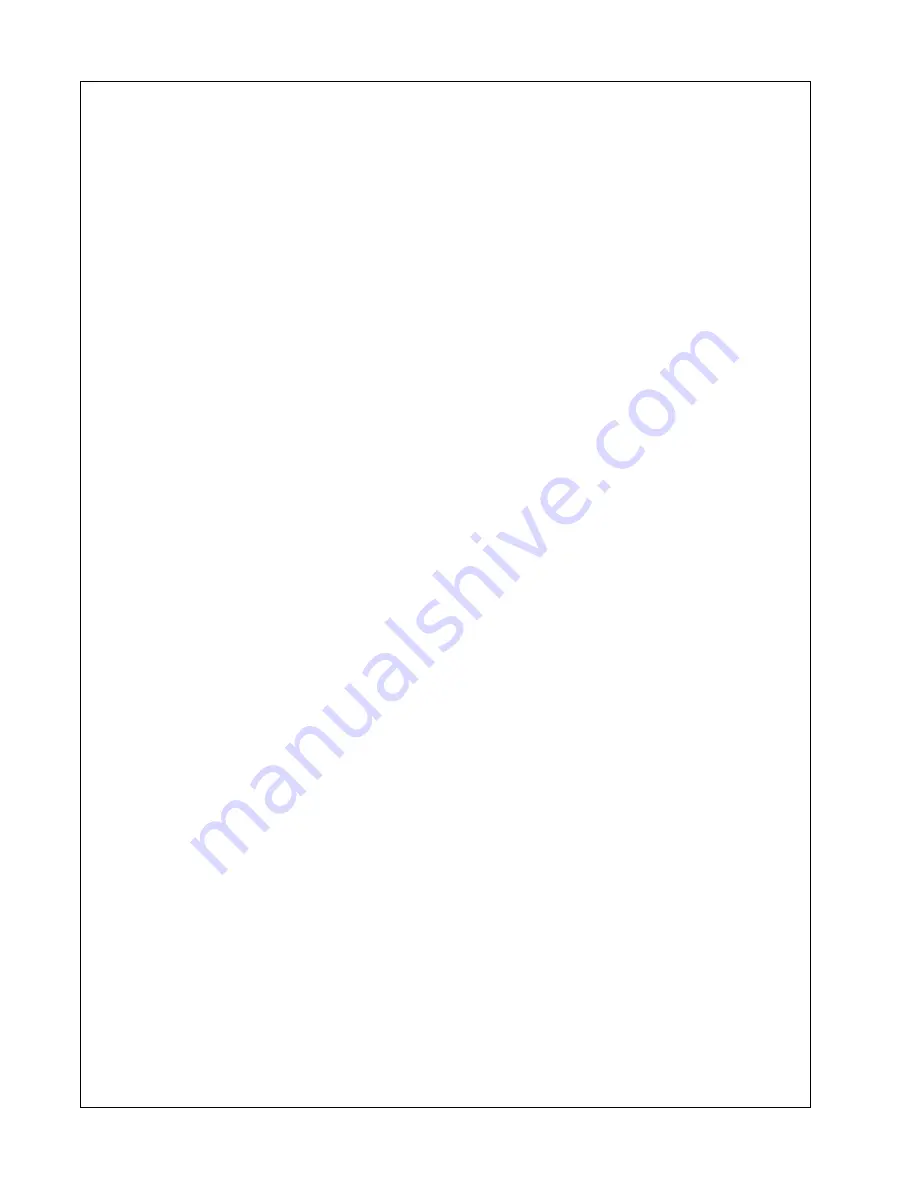
Operating & Maintenance Manual
Electrical
84
Electrical
General Information and Operational Theory
General
The machine has an electronic monitor and control system to provide discharge air pressure
control and engine and package monitor functions. The system uses the WEDGE controller to
perform these functions. The electrical system connects all the necessary switches, sensors
and transducers to the WEDGE controller in order for it to perform the monitor and control
functions.
Wedge Controller
The WEDGE controller is the heart of the machine monitor and control system. It provides data
collection, alarming and control functions for compressor operations. It is a micro controller
based unit with analog and digital inputs and outputs.
The WEDGE controller is attached to the back of the control panel. The LED annunciators are
part of the front panel of the WEDGE. They can be seen through the laminate on the front of
the control panel. The WEDGE is attached to the control panel with four #10 size nuts.
The first function of the WEDGE is to scan all analog and digital inputs at a fixed interval.
These inputs are scanned every 50 milliseconds. The analog values are then compared
against minimum and maximum values and an ALERT or SHUTDOWN is issued, if a value is
out of range. The various ALERTS and SHUTDOWNS are listed in the trouble shooting
section.
The second function of the WEDGE controller is machine discharge pressure control. The
WEDGE monitors the regulation system air pressure and varies the engine throttle to maintain
the setpoint discharge air pressure. The setpoint pressure is set using the regulator on the
separator tank.
The third function of the WEDGE controller is to communicate with the diesel engine via the
J1939 CAN network. The WEDGE controller provides the engine throttle setting to the engine
controller and retrieves diagnostic information from the engine.
A PWM (Pulse Width Modulated) throttle is used to communicate with the CAT engine. The
WEDGE controller receives diagnostic and run time data from the engine over the J1939 CAN
network. A PWM throttle interface is used with the engine.
It has a base frequency of 500 Hz and the duty cycle varies from 10% to 90%.
Figure 8-2 shows the signals between the engine controller and the WEDGE controller.
Summary of Contents for 10/370
Page 2: ...2...
Page 6: ...6...
Page 7: ...7 Foreword...
Page 8: ...Operating Maintenance Manual Foreword 8 Add in PDF Page for CE Mark...
Page 11: ...11 Safety...
Page 19: ...Safety Operating Maintenance Manual 19...
Page 20: ...Operating Maintenance Manual Safety 20...
Page 21: ...Safety Operating Maintenance Manual 21...
Page 23: ...Safety Operating Maintenance Manual 23...
Page 26: ...Operating Maintenance Manual Safety 26...
Page 27: ...27 Noise Emission...
Page 33: ...33 General Data...
Page 36: ...36...
Page 37: ...37 Operating Instructions...
Page 52: ...52...
Page 53: ...53 Maintenance...
Page 66: ...66...
Page 67: ...67 Lubrication...
Page 71: ...71 Troubleshooting...
Page 82: ...82...
Page 83: ...83 Electrical...
Page 88: ...88...
Page 89: ...89 Electrical Schematics...
Page 90: ...Operating Maintenance Manual Electrical Schematics 90...
Page 91: ...Electrical Schematics Operating Maintenance Manual 91...
Page 92: ...Operating Maintenance Manual Electrical Schematics 92...
Page 93: ...Electrical Schematics Operating Maintenance Manual 93...
Page 94: ...94...