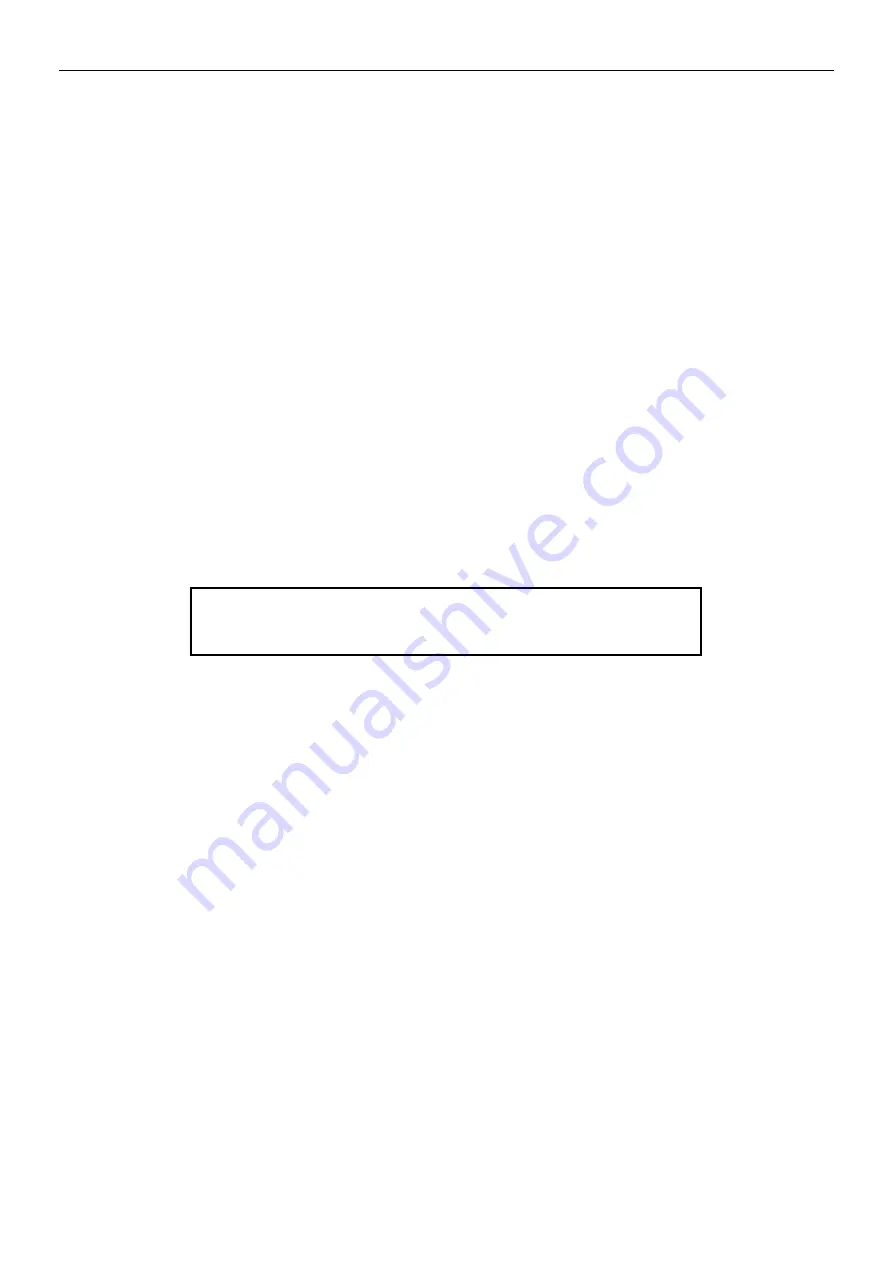
PARTS ORDERING
79
7/125 - 9/115, 7/125 - 10/110, 14/90
For parts, service or information regarding your local distributor (Europe, Middle East, Africa) please contact:
For Service information contact:
For Parts information contact:
Office hours:
Monday to Friday 8:30 a.m. to 5:15 p.m. (GMT)
For parts, service or information regarding your local distributor (U.S, Latin America or Asia Pacific) please contact:
Office hours:
Monday to Friday 8:00 a.m. to 5:30 p.m. (EST)
Facility:
Telephone:
Fax:
Doosan Portable Power EMEA Aftermarket
Drève Richelle 167
B-1410 Waterloo
Belgium
+32 (2) 404 0811
+32 (2) 371 6915
Facility:
Telephone:
Fax:
Doosan International USA, Inc
1293 Glenway Drive
Statesville
North Carolina 28625-9218
800-633-5206 (US & Canada)
305-222-0835 (Latin America)
65-860-6863 (Asia Pacific)
336-751-1579 (US & Canada)
336-751-4325 (Latin America)
336-751-4325 (Asia Pacific)
or visit our website and dealer locator at
www.doosanportablepower.com
Summary of Contents for 10/110
Page 2: ......
Page 4: ......
Page 13: ...GENERAL INFORMATION 9 7 125 9 115 7 125 10 110 14 90 KHD Variable Height LRG Less Running Gear...
Page 72: ...68 MACHINE SYSTEMS 7 125 9 115 7 125 10 110 14 90...
Page 84: ......