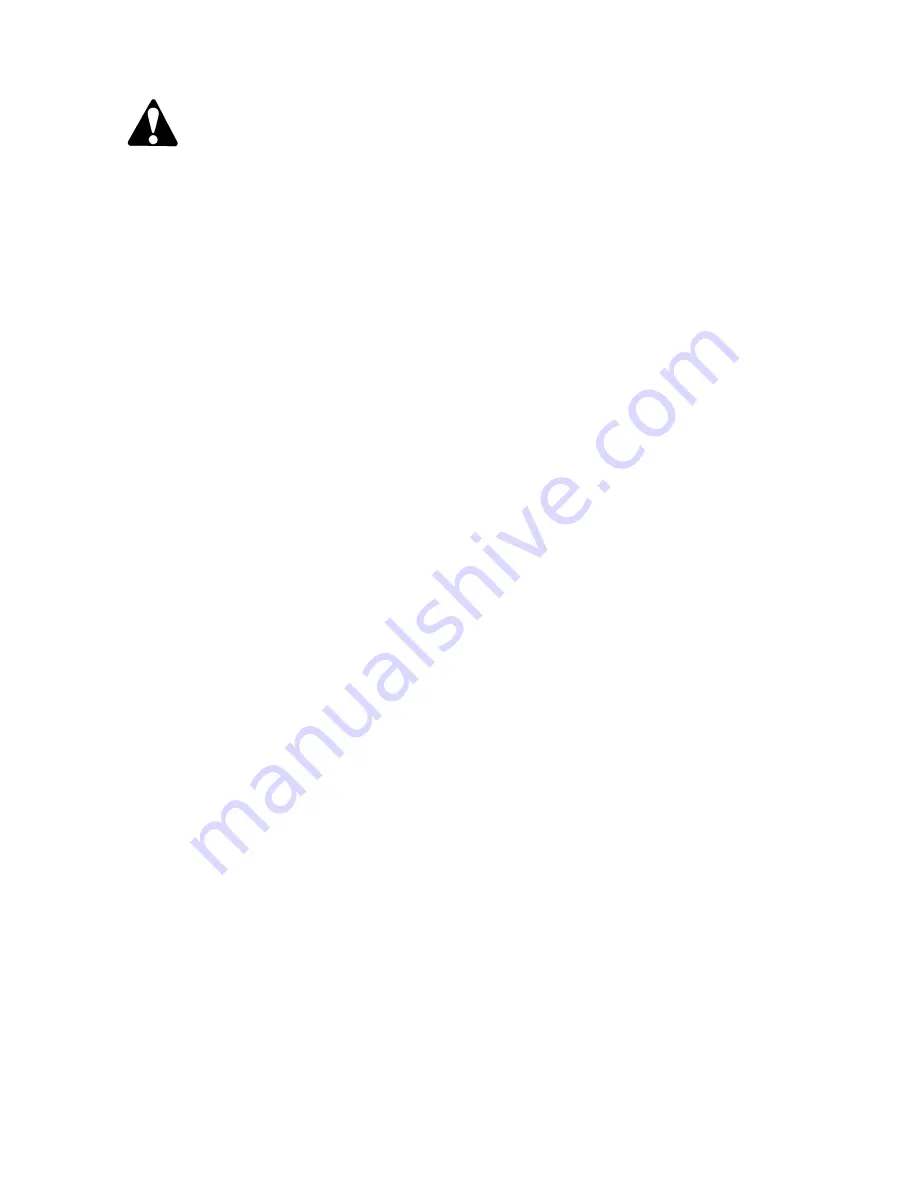
15
Safety Precautions
General
■
Your tractor was designed with safety very much in mind. However, there is no real substitute
for caution and attention in preventing accidents. Once an accident has happened, it is too late
to think about what you should have done.
■
Read this manual carefully before attempting to start, operate, service, refuel or carry on other
operating involving you tractor. A few minutes dedicated to reading will save time and trouble
later.
■
Remember that your tractor was designed and produced exclusively for agricultural use. If the
owner of the tractor is to use it for any other purposes, he has to get the prior authorization from
the Manufacturer in advance.
■
Keep a first aid tool handy.
■
Do not work with loose garments that could get caught in moving parts. Check that all rotating
parts connected to the power take-off shaft are properly shielded.
■
This tractor has to be operated by the people who were trained on the use and maintenance of it,
and they also have to be duly authorized to operate it in advance.
■
Do not attempt to increase the maximum engine rpm by altering the setting of the fuel injection
system.
■
Do not alter the pressure relief valve settings of the different hydraulic circuits hydraulic lift
and remote control valves.
■
Do not operate tractor if you feel unwell or physically unfit, in which case you should stop
working.
■
Always operate with the cab and rollover safety frame undamaged, complete of all components
and correctly installed on the tractor; periodically check fastenings for tightness and frame and
structures to make sure they are free from damages consequent on accidental impacts.
Starting the Tractor
■
Prior to starting the engine, check that the parking brake is on and transmission and PTO are in
neutral.
■
Make sure all implements are fully lowered down to ground before starting the engine.
■
Make sure, before starting the engine, that all guards, shields and protections are correctly
installed on your tractor.
■
Do not attempt to start or drive the tractor unless sitting in the operator’s seat.
■
Always make sure, before starting the tractor in motion, that there are no people or obstacle
within range.
■
Do not run the engine inside closed premises without adequate ventilation, as exhaust fumes
are harmful to health or may even become deadly.
Tractor Operation
■
Select the track width setting best suitable to work, always keeping tractor stability in mind.
■
Engage clutch gradually: abrupt engagements, particularly if pulling out of a rough area, a ditch
or muddy grounds, or driving over a steep gradient, may cause dangerous tractor pitching.