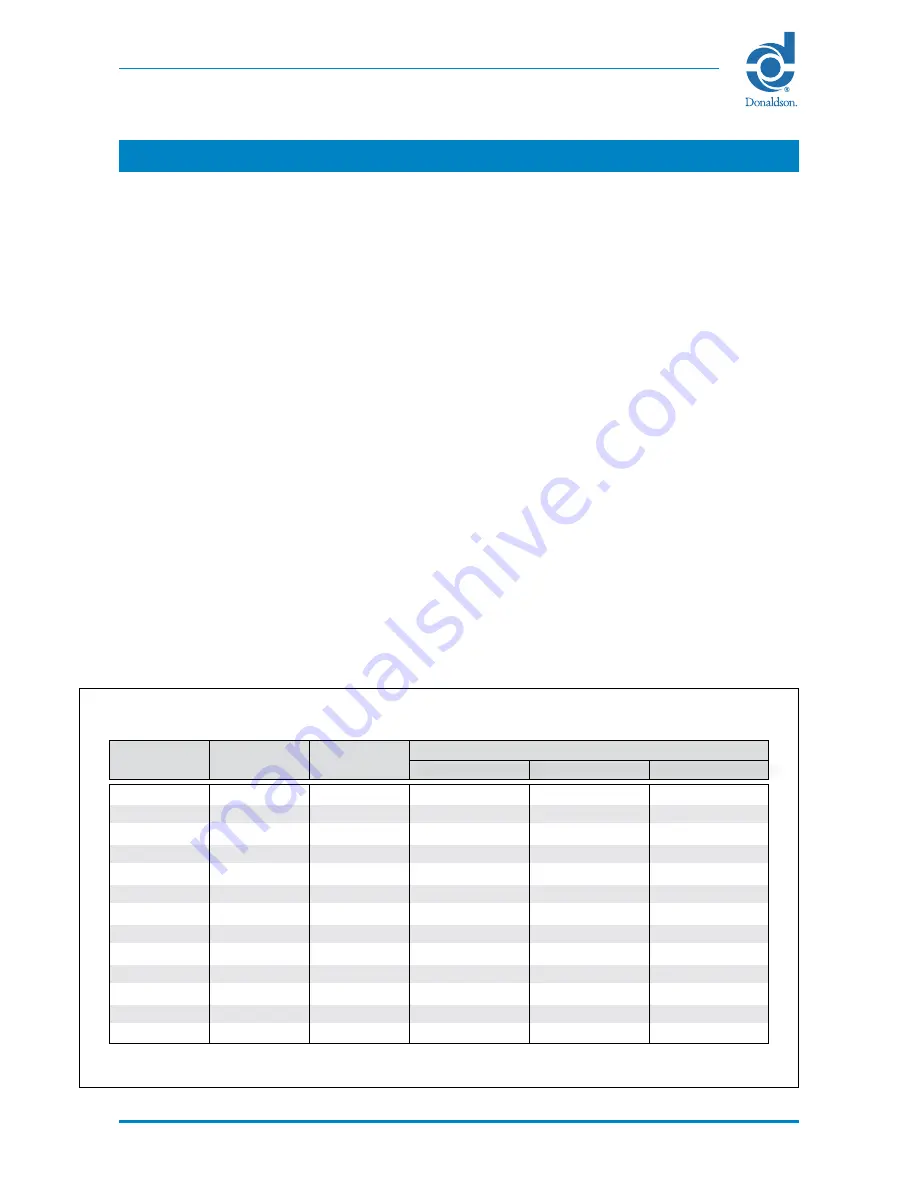
27
Dalamatic Insertable Dust Collectors – Series DLM V
Installation, Operation and Maintenance Manual
4 Undo and remove bolt in end of motor shaft holding the hub retaining washer.
5 Remove motor key by easing it out from keyway.
6 Using the location grooves machined into hub, pull impeller from motor shaft
and out through the front of fan case.
7 Slide spacer off motor shaft.
8 Remove the 4 nuts, bolts and washers holding motor to pedestal.
9 The motor can now be removed using suitable lifting equipment, taking
care not to damage sealing washer placed between motor endplate and
fan casing.
10 Place the new motor on support pedestal and locate rubber sealing washer
between fan case and motor.
11 Position motor on pedestal and secure loosely by replacing the 4 nuts, bolts
and washers.
12 Locate motor key into keyway on motor shaft.
13 Push motor shaft spacer onto motor shaft.
14 Align keyway of impeller hub onto key and slide impeller onto motor shaft.
15 Replace hub retaining washer and shakeproof washer. Apply thread lock
to motor end shaft bolt and replace bolt, ensuring impellor is pushed back
onto spacer.
16 Apply thread locks to grub screws holding hub and tighten into place.
17 Locate impeller, according to the dimension taken during removal, by moving
motor along pedestal, ensuring motor remains square to fan case.
MAINTENANCE
TABLE 1 – TORQUE VALUES FOR BOLTS WITH ISO METRIC THREAD
* For nuts and bolts to ISO 4017.
8 mm
1 mm
20.1 mm²
10.4 Nm
15.3 Nm
17.9 Nm
7 mm
1 mm
28.9 mm²
17.2 Nm
25 Nm
30 Nm
8 mm
1.25 mm
36.6 mm²
25 Nm
37 Nm
44 Nm
10 mm
1.5 mm
58 mm²
50 Nm
73 Nm
86 Nm
12 mm
1.75 mm
84.3 mm²
86 Nm
127 Nm
148 Nm
14 mm
2 mm
115 mm²
137 Nm
201 Nm
235 Nm
16 mm
2 mm
157 mm²
214 Nm
314 Nm
368 Nm
18 mm
2.5 mm
192 mm²
306 Nm
435 Nm
509 Nm
20 mm
2.5 mm
245 mm²
432 Nm
615 Nm
719 Nm
22 mm
2.5 mm
303 mm²
592 Nm
843 Nm
987 Nm
24 mm
3 mm
353 mm²
744 Nm
1060 Nm
1240 Nm
27 mm
3 mm
459 mm²
1100 Nm
1570 Nm
1840 Nm
30 mm
3.5 mm
561 mm²
1500 Nm
2130 Nm
2500 Nm
Nominal
diameter
Torque value*
Grade 8.8
Thread
pitch
Stress
area
Grade 10.9
Grade 12.9