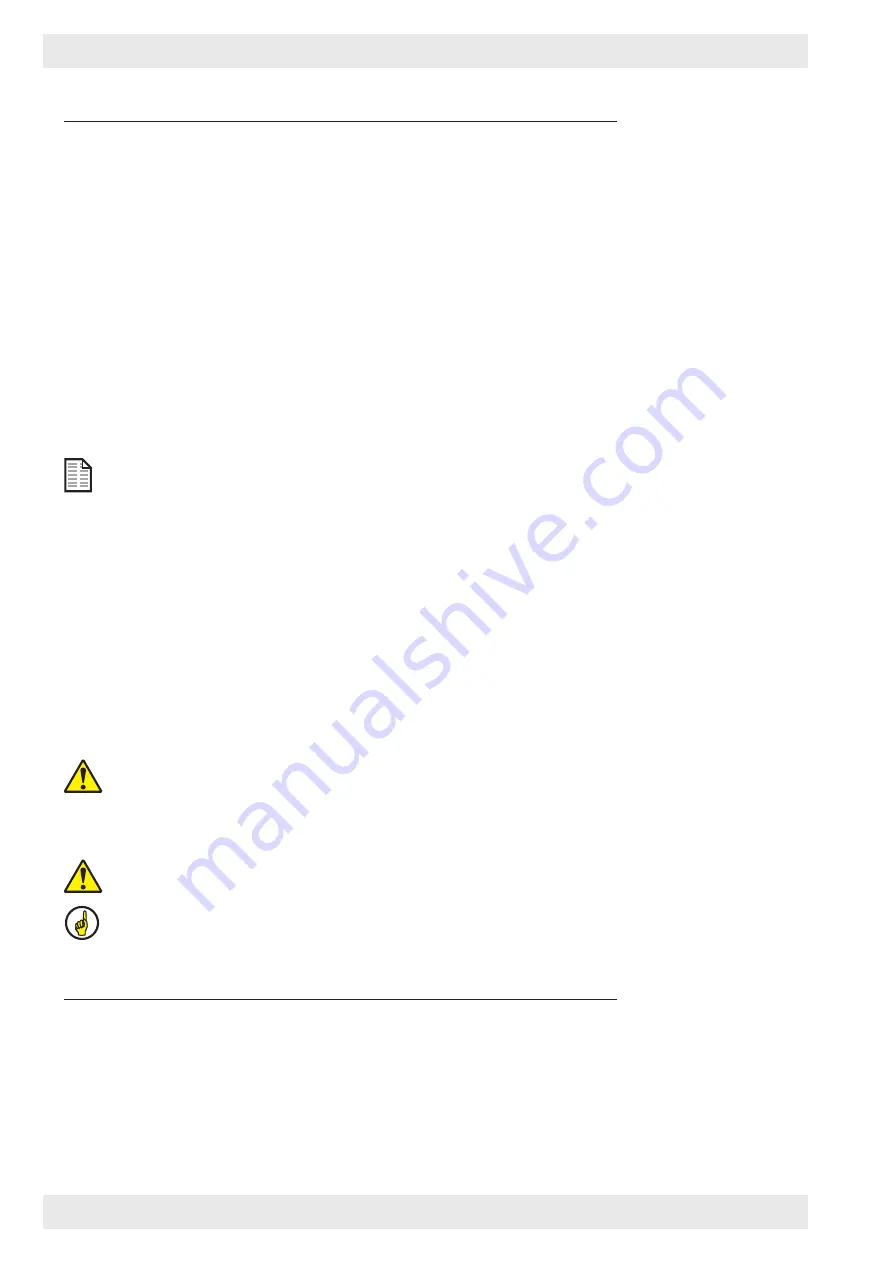
Installation, Operation and Maintenance manual
22
DFPRE Large Dust Collectors
Routine inspection
To maintain the optimum performance of the dust collector, a routine inspection should
be made to minimise down-time in the event of equipment malfunction, particularly
on continuous performance applications and to ensure the equipment is maintained
to its original supply condition.
Any abnormal change in differential pressure across the filter cartridges indicates a
change in operating conditions and a fault to be rectified. For example, a prolonged
stoppage of compressed air will cause an excessive build-up of dust on the cartridges,
resulting in a greatly increased pressure drop.
After the fault has been rectified, resumption of compressed air cleaning will usually
return the filter to normal efficiency. However, it is advis able to operate the in still-air
conditions for a short period to dislodge any accumulated dust before putting the
collector into operation.
Filter resistance can be checked by viewing the display on the front panel of the
controller. This will give a continuous indication of the state of the filter. Once running,
the operating resistance will be relatively stable, the actual value depending on the
air volume and the characteristics of the dust being handled.
If the differential pressure exceeds 120 mm WG, check the following:
•
The compressed air supply is installed correctly, is free of water or oil and
is maintained at the recommended pressure (refer to Table 3).
•
The differential pressure connections are not blocked.
•
The solenoid and diaphragm valves are functioning correctly.
•
The controller is operational.
•
The dust container is properly sealed.
If the differential pressure still exceeds 120 mm WG after checking the above,
then reduce the pulse cleaning interval time to see if this will improve the
cleaning of the filter cartridges and, in turn, lower the differential pressure
(details of pulse interval settings are provided in the controller manual).
If the differential pressure exceeds 150 mm WG, then the cartridges have
reached the end of their lifetime and need replacing.
Ignition minimising fans are fitted with a lining inside the casing. As this may
only offer protection for a limited period, if there is any upset condition leading
to rubbing, then the fan must be switched off immediately and the condition
corrected.
It is recommended to periodically inspect the general casing integrity.
Do not operate above recommended compressed air pressure. Excessive
pressure will reduce the working life of components.
Servicing schedule
A record of all pressure checks should be kept in a log book to aid the speedy diagnosis
of faulty operation.
Daily
1. Check level of contents in dust container and cyclopeel if applicable, and empty
if ¾ full.