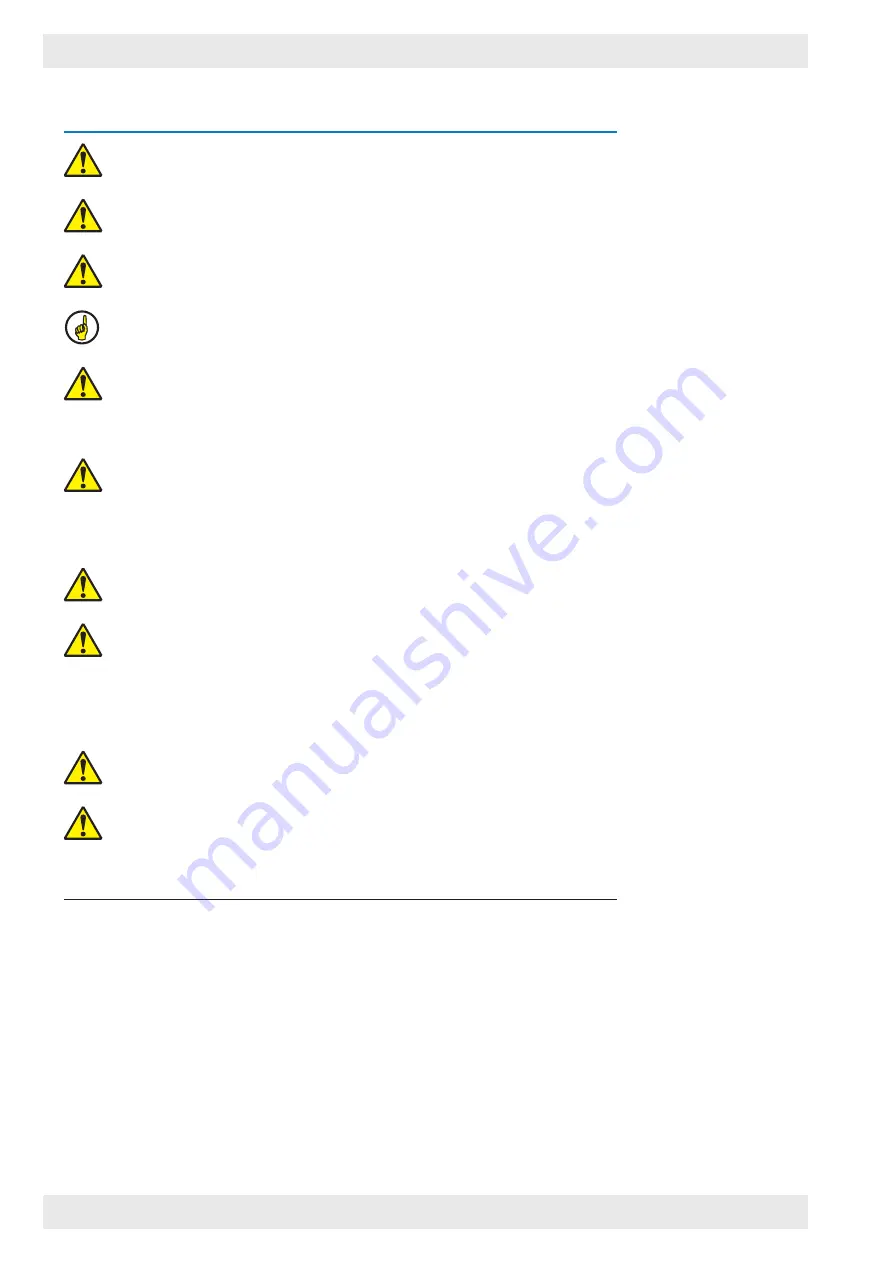
Installation, Operation and Maintenance manual
16
PowerCore
®
Dust Collectors - Series CPV
MAINTENANCE
A platform should be used when carrying out maintenance where the position
of the technician’s feet is greater or equal to 2 metres above ground level.
Before any work is carried out, ensure the equipment is adequately isolated
and safe.
Ensure the pneumatic system is fully isolated and depressurised before any
work is carried out.
For ancillary equipment not manufactured by Donaldson, refer to manufacturer’s
instructions.
If it is unavoidable to work on the equipment while a potentially explosive
atmosphere is present, care should be taken to avoid introducing ignition
sources not present during expected operation. Non-sparking tools should
be used.
Access to the dirty air chamber of the equipment may create risks and hazards
that under normal circumstances are not present and as such this work must
be carried out by competent personnel. These risks include inhalation of dust
and potential explosion hazards. Appropriate personal protection equipment
(PPE) should be used, e.g. dust mask, safety hat, gloves etc.
In order to maintain the original collector specification and to ensure the same
level of safety, only genuine spare parts should be fitted.
Every care has been taken to avoid the risk of ignition of a flammable
atmosphere. The measures taken to avoid ignition should not be altered since
this may result in unsafe operation. Particular care should be taken during
maintenance and component replacement to ensure the same level of safety
is maintained. When replacing fan impellers, avoid any rubbing of components
(to prevent mechanical sparks).
Care should be taken during cleaning and maintenance to avoid creating static
discharges that have the potential to ignite a flammable atmosphere.
When carrying out maintenance always follow typical best practice to local
regulations (e.g. TRGS 560).
Routine inspection
To maintain the optimum performance of any dust collector, a routine inspection should
be made to minimise down-time in the event of equipment malfunction, particularly
on continuous performance applications and to ensure the equipment is maintained
to its original supply condition.
Any abnormal change in pressure differential across the filter packs indicates a change
in operating conditions and a fault to be rectified. For example, a prolonged stoppage
of compressed air will cause an excessive build-up of dust on the filter packs, resulting
in a greatly increased pressure drop.
After the fault has been rectified, resumption of compressed air cleaning will usually
return the filter packs to normal efficiency. However, it is advis able to operate the
controller in still-air conditions for a short period to dislodge any accumulated dust
before putting the collector into operation.