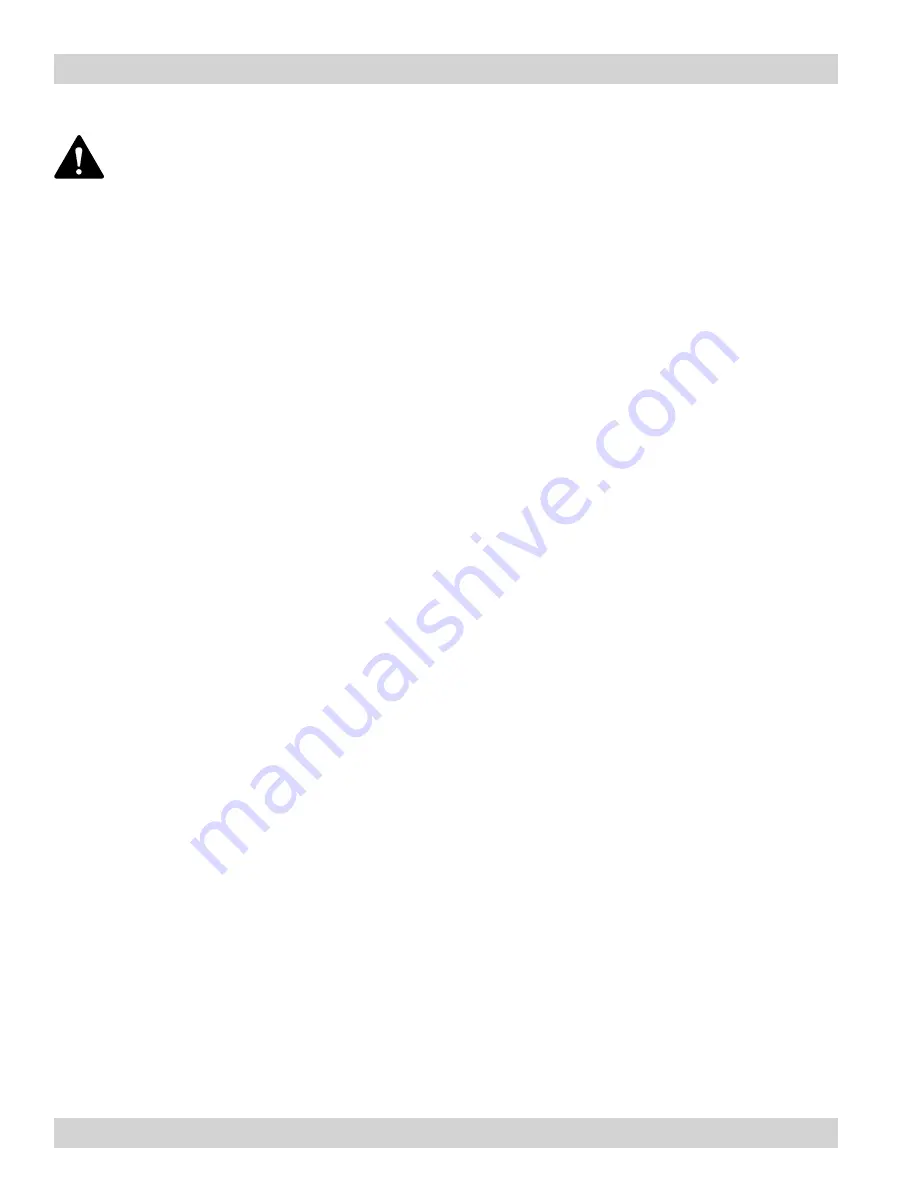
1
Donaldson Company, Inc.
Improper operation of dust collectors and/or dust control systems may contribute to conditions in a work
area or facility which could result in severe personal injury, and product or property damage. All dust
collection equipment should be used only for its intended purpose and should be properly selected and sized
for its intended use.
Process owners have important responsibilities relating to identifying and addressing potential hazards in
their processes. When the potential for handling combustible dust exists within a process the process owner
should include combustion hazards in their risk management activities and should comply with applicable
codes and standards related to combustible dust.
Electrical installation must be performed by a qualified electrician.
This equipment is not designed to support site ducts, piping, or electrical services. All ducts, piping, or
electrical services must be adequately supported to prevent injury and/or property damage.
Site selection must account for wind, seismic zone, and other load conditions.
Equipment may reach peak sound pressure levels above 80 dB (A). Noise levels should be considered when
selecting collector location.
Combustible Dust Hazards
Among other considerations, the current NFPA standards require owners whose processes involve potentially
combustible materials to have a current Dust Hazard Analysis, which can serve as the foundation for their process
hazard mitigation strategy. Mitigation may include but is not limited to:
• Prevention of all ignition sources from entering any dust collection equipment.
• Selection and implementation of fire and explosion mitigation, suppression, and isolation strategies
appropriate for the risks in their process.
• Development and use of work practices to maintain safe operating conditions, and to ensure combustible dust
does not accumulate within their plant or process equipment.
Donaldson designs, manufactures, and sells industrial air filtration products for a wide variety of applications. Some
applications may include processes or materials with inherent fire and explosion hazards. Donaldson is neither an
expert nor a certified consultant in fire, spark, or explosion detection, suppression, or control. Donaldson does not
provide engineering consulting services related to process or dust hazard analyses, or code and standard compliance.
Complying with applicable codes and standards and managing the risks associated with the process or materials
remains the responsibility of the process owner/operator. Donaldson may provide referrals to consultants, suppliers
of equipment or services related to the detection and/or mitigation of sparks, fires and/or explosions, but Donaldson
does not assume responsibility for any such referrals, nor does Donaldson assume any liability for the fitness of a
mitigation strategy or product for a particular installation or application. The process owner’s final selection of dust
collectors and risk mitigation strategies should be based on the outcome of a Dust Hazard / Process Hazard Analysis
performed by the process owner. Although early engagement of a dust collector supplier provides helpful insights on
the availability and features of various products, process owners should consult with a combustible dust expert and/or
a process safety expert before making actual product and mitigation strategy selections.
Donaldson recommends that all industrial air filtration system designs be reviewed and approved by an expert
consultant who is responsible for the integrity of the system design and compliance with applicable codes and
standards. It is the process owner’s responsibility to understand the risks in their process and mitigate those risks in
accordance with all applicable laws, regulations and standards, including those published by the NFPA. Donaldson
also recommends that proper maintenance and housekeeping procedures and work practices be evaluated,
developed, and followed to maintain any industrial air filtration products in safe operating condition.
Many factors beyond the control of Donaldson can affect the use and performance of Donaldson products in a
particular application, including the conditions under which the product is used. Since these factors are uniquely
within the user’s knowledge and control, it is essential the user evaluate the Donaldson products to determine whether
the product is fit for the particular purpose and suitable for the user’s application. All products, product specifications,
and data (airflow, capacity, dimensions, or availability) are subject to change without notice, and may vary by region or
country.
Safety Communication