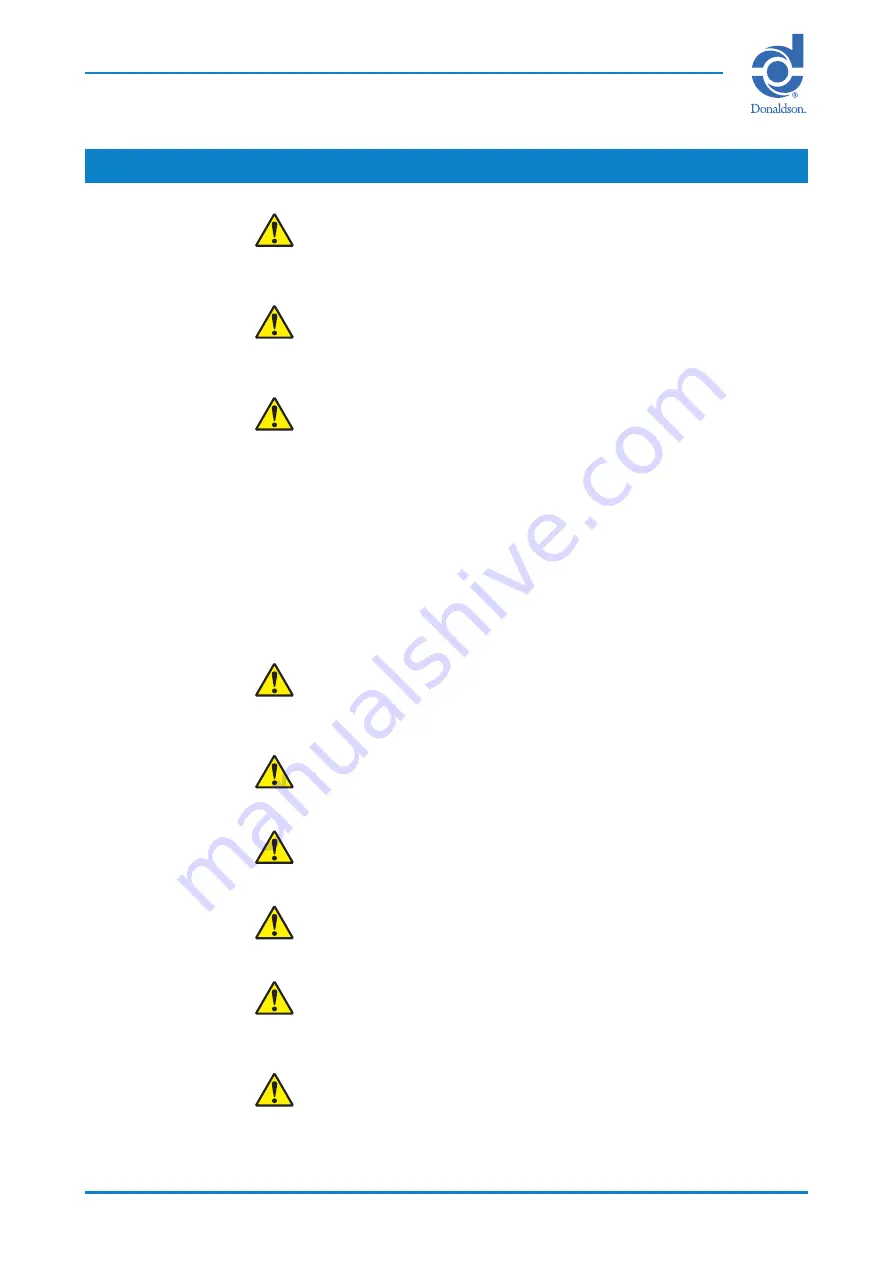
Installation, Operation and Maintenance Manual
DCE 2000 Series Dust Collectors
5
General safety reQuIrements
The collector should be stored as supplied. Only remove packaging to install.
For the purposes of storage:
Collector with specification for inside use = IP50.
Collector with specification for outside use = IP54.
The dust collector should be used only when it is in a technically acceptable
condition. Regular maintenance, as set out in this manual, is required to
minimise technical failure. Third party supplied components (for example
motors) should be maintained according to the manufacturer's instructions.
You should ensure any persons carrying out work on the supplied equipment
follow any relevant recognised standards/codes, have received adequate
training and are competent to do so. Areas requiring a competent person
include:
Maintenance on any component identified as a potential ignition source.
Lifting and erection.
Electrical installation, inspection and maintenance work.
Pneumatic installation, inspection and maintenance work.
Any access to internal classified potentially explosive atmospheres where
there may be a risk due to explosion.
During assembly/installation or dismantling of equipment, potential ignition
sources may occur that were not considered in the risk assessment of the unit
in operation (for example, grinding, welding sparks, etc.)
You should use the dust collector in full accordance with the conditions set
out in the Order Acknowledgment and relevant Scope of Delivery. Failure to
do so may compromise product reliability, warranty and safety. The Scope of
Delivery is an integral part of the manual.
Other items of equipment, not supplied under the Scope of Delivery from
Donaldson, should be installed, operated and maintained according to the
documentation supplied with the respective equipment.
Any modification carried out on the 'as supplied' equipment may reduce
reliability and safety, and will nullify warranty; such actions fall outside the
responsibility of the original supplier.
The hopper should not be used as a storage vessel. To prevent damage to
the collector, care should be taken to avoid an excessive build up of heavy
materials.
Where necessary for safety, the dust collector is fitted with fixed guards.
Removal of these guards and any subsequent work should only be carried
out after adequate precaution is taken to ensure it is safe to do so. All guards
should be refitted before re-energising.
The access door requires tools to open. To avoid danger from rotating fan
impellor, ensure fan is isolated and allow sufficient time for fan to become
stationary.
Summary of Contents for DCE 2000 Series
Page 43: ......