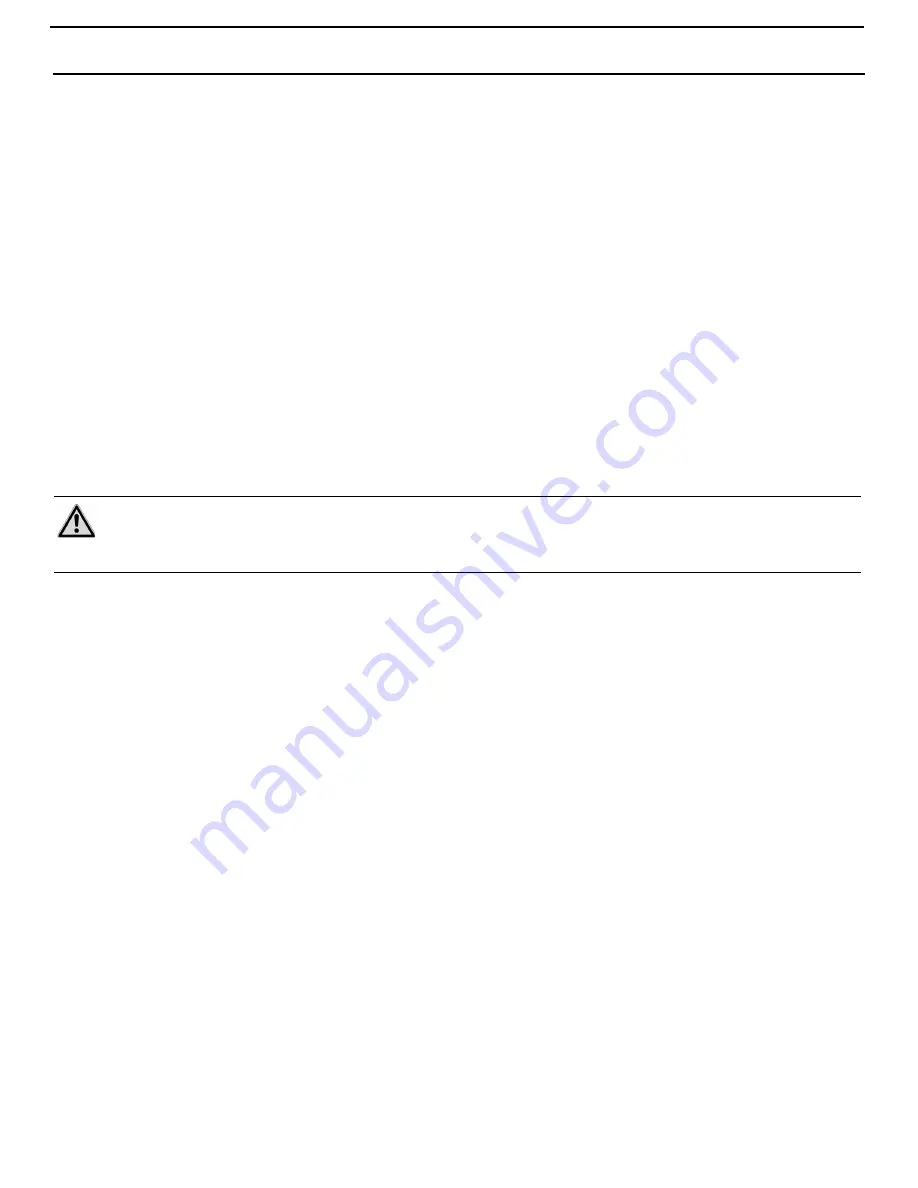
Service Valve Operation
DuraSea Condenser Installation, Start-Up & Service Manual
10
L-3153
I
NSTALL
F
ILTER
D
RIER
Every unit MUST have a filter drier in the liquid line.
Locate the filter drier(s) at the indoor unit, close to the evaporator coil's thermal expansion valve (TXV) inlets.
A R-410A rated filter drier is shipped in cartons near the base valves. Remove drier from packaging and install in the liquid
line(s) at the evaporator coil. Do not remove connection fitting plugs until ready to connect and braze the filter drier into the
liquid line position. Ensure the filter drier paint finish is intact after brazing. If the paint of the steel filter drier has been burned or
chipped, repaint or treat with rust preventative.
I
NSTALL
L
IQUID
L
INE
S
OLENOID
V
ALVE
It is recommended that a solenoid valve be placed in the main liquid line between the condensing unit and the evaporator coil.
Locate the solenoid valve at the outlet end of the liquid line, near the evaporator coil connections, with flow direction arrow
pointed at the evaporator coil. A liquid line solenoid valve is required when the liquid line length exceeds 75 ft [23 m]. This valve
prevents refrigerant migration (which causes oil dilution) to the compressor during the off cycle, at low outdoor ambient
temperatures.
S
ELECTING
AN
A
CCUMULATOR
Because all DuraSea models use scroll compressors, an accumulator is not required. Long refrigerant line applications may
require use of accumulator to protect compressor from excess charge. If an accumulator is to be added, check the accumulator
manufacturer's literature carefully for indication of its suitability for use with R-410A; look for minimum working pressure of 200
psig (1380 kPa). Select the accumulator first on the basis of its minimum capacity in tons to ensure oil return from the
accumulator, then on tube size or holding capacity.
M
AKE
P
IPING
C
ONNECTIONS
Piping connections at the DuraSea unit are base valves with stub tube extensions. Do not open the unit service valves until all
interconnecting tube brazing has been completed. The stub tube connections include 1/4-in SAE service fittings with Schrader
valve cores. Before making any brazed connections to the unit service valves, remove both Schrader valve caps and cores and
save for re-installation. Connect a source for nitrogen to one of these service fittings during tube brazing to prevent the
formation of copper oxides inside the tubes at brazed joints.
When brazing the field tubing to base valves, TXV valve, or filter drier, wrap the valves in wet rags to prevent overheating. Use
a brazing alloy of 5% minimum silver content. Do not use flux. Purge the refrigerant line with nitrogen during brazing to prevent
the formation of copper-oxide inside the refrigerant lines. After brazing quench the joints with water or a wet cloth to prevent
overheating of valves.
I
NSULATE
S
UCTION
L
INES
Insulation is necessary to prevent condensation from forming and dropping from the suction line. Apply Armaflex (or satisfactory
equivalent) closed-cell tubular insulation with ½" minimum wall thickness to all suction lines between evaporator coil connection
and unit's suction service valve. In severe hot and humid areas thicker wall insulation may be needed. Insulation must be
installed in a manner which protects tubing from damage and contamination.
R
OUTING
OF
L
IQUID
L
INE
The liquid line must be outside the suction line insulation. If part of the liquid line must run through an area that will be hotter
than 120°F (49°C), then that portion of the liquid line must be insulated. Be careful not to kink or dent the refrigerant lines.
Kinked or dented lines will cause poor performance or compressor damage.
S
ERVICE
V
ALVE
O
PERATION
The DuraSea condensing unit is equipped with service valves to ensure safe handling of the high-pressure R-410A refrigerant.
The unit is shipped with the valve frontseated (downward position) to contain the factory charge in the unit. Gauge hoses can be
connected and disconnected without the presence of system pressure. The gauge port is isolated from the system if the stem is
backseated. The gauge ports have a standard core valve, which can be removed and replaced while the stem is backseated.
R
EPLACEMENT
/R
ETROFIT
Replacement/retrofit installations require change-out of outdoor unit, metering device, and filter driers. Change-out of indoor coil
(evaporator) and interconnecting tubing is highly recommended.
CAUTION
Do not leave system open to atmosphere any longer than necessary for installation. The compressor PVE or POE oil
is extremely susceptible to moisture absorption and could cause compressor failure.
Ensure ends of tubing are sealed before and during installation.
Summary of Contents for DuraSea DCA120D
Page 27: ...NOTES ...