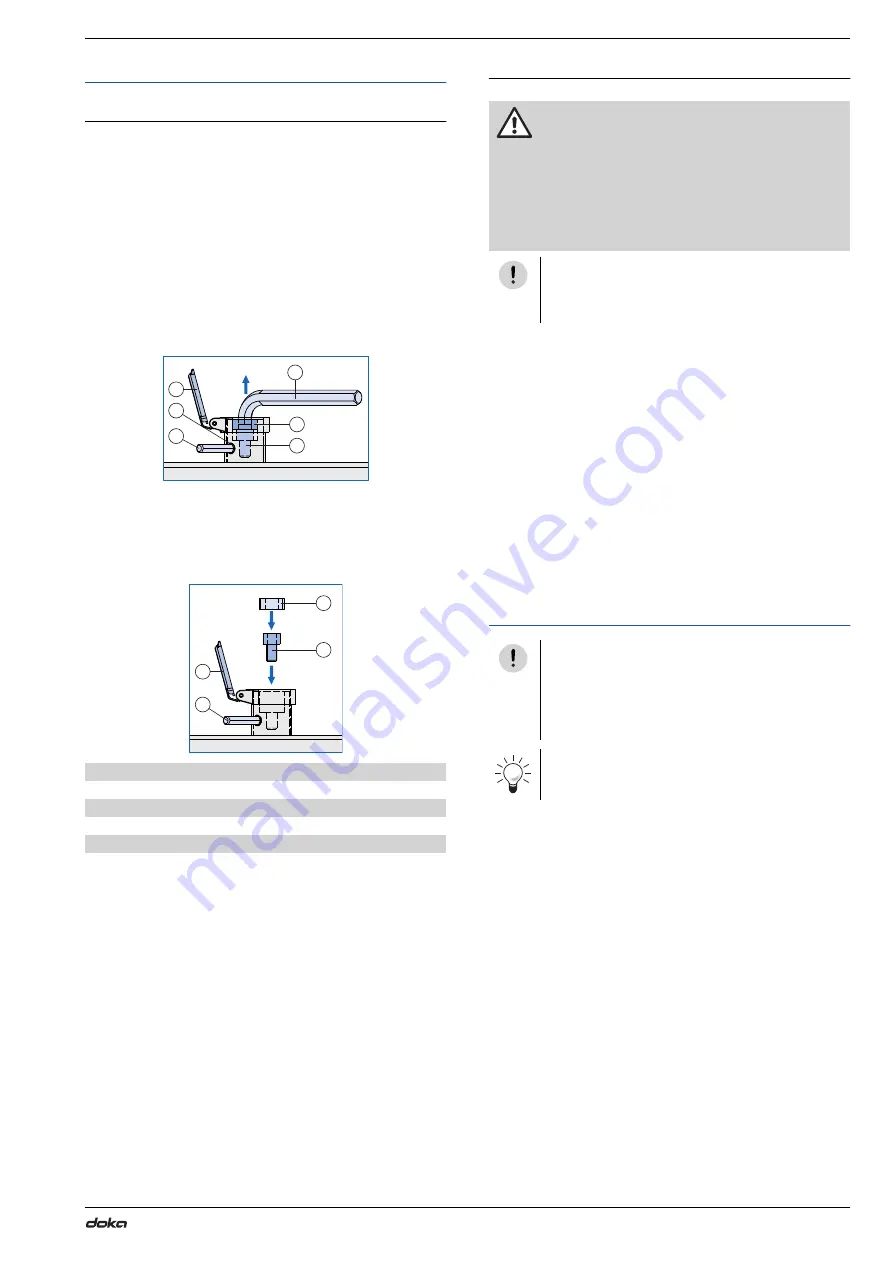
Original Operating Instructions
Framax stripping corner I hydraulic
13
999239002 - 07/2018
Maintenance
Changing the drive
Note:
The drive hexagon socket (width-across 8 mm) has to
be replaced if it is damaged.
There are 3 spare cylinder screws M10x20 - 10.9 in the
documents container.
➤
Open the blue drive flap.
➤
Insert the bit (width-across 8 mm) into the locking
bore.
➤
Loosen locknut (width-across 12 mm) with hexagon-
socket screw key (width-across 12 mm).
➤
Remove cylinder screw M10x20 - 10.9 and replace it
with a new cylinder screw M10x20 - 10.9.
Width-across, hexagon socket 8 mm
➤
Retighten the locknut (width-across 12 mm).
Changing the oil
➤
Unscrew the plug with a hexagon-socket screw key
(width-across 5 mm).
➤
Lift the unit on to a used-oil drum and drain the oil
into the drum.
➤
Re-seal the plug with Teflon tape, and screw it back
in.
➤
Open the screw at the oil filling opening.
Width-across 17mm
➤
Refill the reservoir with approx. 3
litres of hydraulic
oil (up to the maximum mark). Use 'Shell Tellus S2
V15' hydraulic oil.
➤
Re-seal the oil filling opening.
➤
Dispose of the waste oil and soiled cleaning utensils
correctly. Observe all relevant national laws.
Transport
A
Drive flap
B
Locking bore
C
Bit (width-across 8 mm)
D
Locknut (width-across 12 mm) (painted red
E
Hexagon-socket screw key (width-across 12 mm)
F
Cylinder screw M10x20 - 10.9 (drive hexagon socket (width-
across 8 mm)
F
A
9239-203-01
D
B
E
C
A
C
9239-203-02
F
D
CAUTION
Risk of burns or scalds if an oil change is
attempted while the hydraulic oil is still hot!
➤
If the hydraulic unit has been in operation for
a lengthy period, allow the hydraulic oil to
cool down before changing the oil.
Maximum oil temperature for oil changes:
40°C.
NOTICE
Interval for oil change:
▪
once a year
NOTICE
Do not put the hydraulic unit on its side!
Putting the hydraulic unit on its side causes
damage to the unit and leakage of hydraulic
oil.
The handles or the strap can be used for trans-
porting the Hydraulic unit Framax V4.