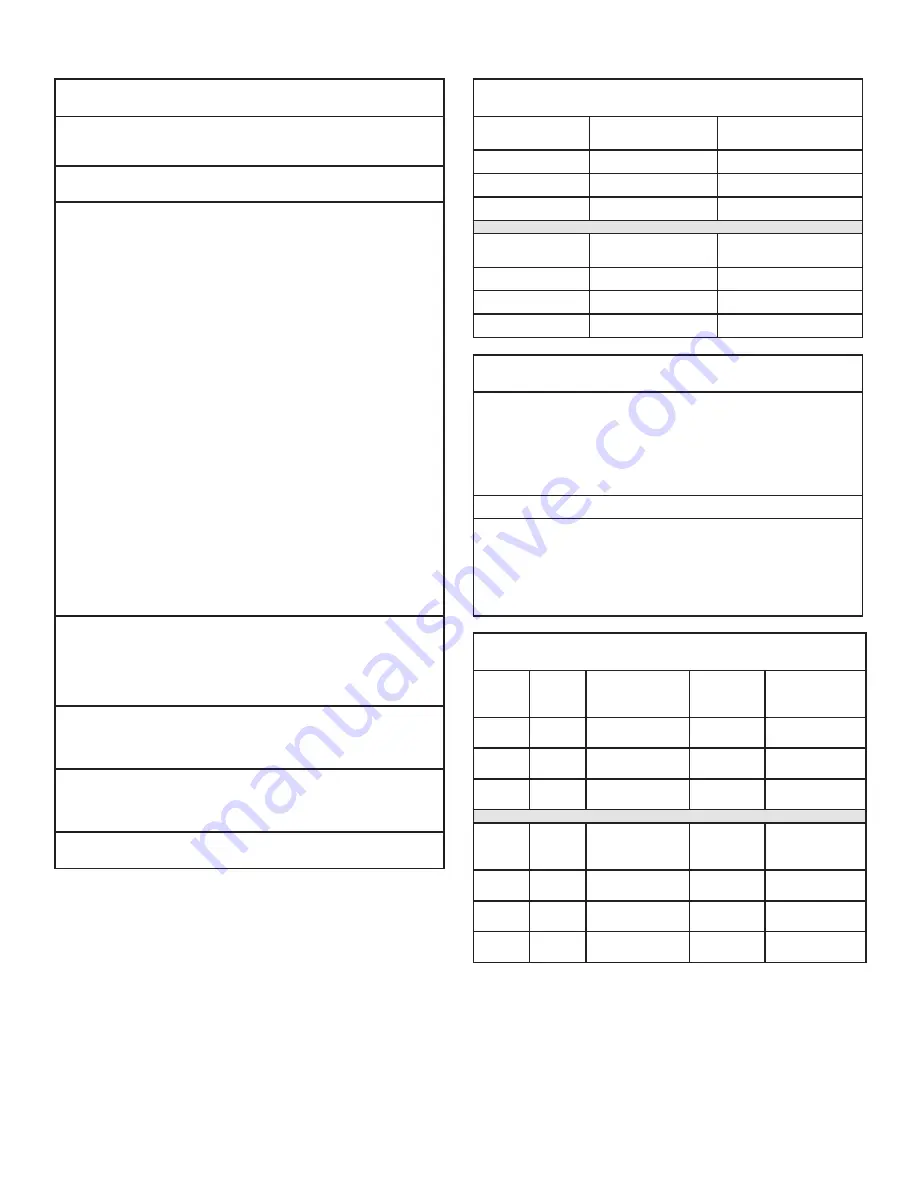
6
MN16022
Table 3 - Mounting Motors to C-Faced Reducers
For Clamp Collar Input Reducers
(Reference Figure 1 & 2)
Prepare the motor by checking the motor shaft extension for dirt or
damage. Use solvent to remove all traces of anti-rust coating that may
be on the shaft.
Check the input bore for dirt or damage. Clean the bore with solvent to
remove all traces of oil or anti-rust coating.
For NEMA motors ONLY: A special long, tall motor key is provided
with the Quantis unit.
1. Discard the motor key and replace it with the special key
provided. DO NOT USE THE MOTOR KEY.
2.
If the special key does not fit snugly in the motor shaft keyway,
prepare the key for assembly by nicking its bottom in a couple
of spots. A chisel may be used to accomplish this. This must
be done on a work surface away from the Quantis unit and the
motor. This nicking should widen the key bottom and cause it to
fit snugly in the motor keyway. Refer to Figure 2 for definition of
key bottom.
3.
Install the key in the motor shaft keyway by lightly tapping it in
place with a rubber mallet.
4.
Locate the key so that it sits flat in the motor shaft keyway. The
key will probably extend beyond the end of the motor shaft. This
is OK. The key MUST NOT sit tilted in the keyway. A tilted key
can occur when a motor shaft has a sled runner keyway, Refer to
Figure 2.
5.
Mark the clamp collar with a fine tipped marker on both sides
of the setscrew to indicate where the center of the set screw is
located. Run a line down both sides of the clamp collar that line
up with the line previously created.
6. Remove the socket head screw and set screw from the clamp
collar and apply Loctite 243 thread locker. Reinstall the screws
into the clamp collar. Install the clamp collar onto the reducer
input shaft and line up the mark previously made on the clamp
collar with the center of the keyway in the shaft. If the clamp
collar rotates freely, tighten the clamping screw slightly to keep
it from rotating during assembly. Make sure the marked line is
pointing to the center of the keyway.
The Dodge Quantis RHB C-Face reducer should be firmly anchored
to prevent sliding as the motor is mounted. The motor should be
rotated on its axis so the motor flange holes line up with the C-Face
adapter holes. Check to be sure the motor conduit box, grease fittings
and condensate drains (where fitted) will be oriented as needed by the
reducer mounting position.
Hoist motor level and in line with reducer input shaft. For EZ Kleen
Quantis reducers with 180TC or larger NEMA input, install the o-ring
provided onto the motor pilot to seal the input assembly from water
ingress.
Align the motor shaft with the gear reducer input bore making sure
that the motor shaft keyway is in line with the input bore key. Push the
motor into place. Motor shaft to input bore clearances are tight and
good alignment is essential.
Insert and tighten the motor retaining bolts. Tighten to the correct
torque value listed below.
Table 3 - Mounting Motors to C-Faced Reducers
For Clamp Collar Input Reducers
(Reference Figure 1 & 2)
NEMA Motor
Frame
Motor Bolt
Bolt Tightening
Torque
56C, 140TC
3/8-16
236 lb-in (27 Nm)
180TC,
1/2-13
516 lb-in (58 Nm)
IEC Motor
Frame
Motor Bolt
Bolt Tightening
Torque
71
M8
188 lb-in (21 Nm)
80, 90
M10
372 lb-in (42 Nm)
100
M12
648 lb-in (73 Nm)
FOR CLAMP COLLAR INPUT REDUCERS
(Reference Figure 1)
View the clamp collar through the access holes in the C-face adapter.
1. Rotate the clamp collar to locate the setscrew over the key, if
necessary.
2. Tighten the setscrew to the torque referenced below.
3.
Reach through the access hole in the C-face adapter with a hex
socket and tighten the clamp collar clamping bolt to the torque
value given below.
Replace the access hole plugs in the C-face adapter.
NOTE: A TEE handle hex key wrench is not stiff enough to
properly tighten the clamp collar bolt. A socket wrench extension
with a hex insert must be used in conjunction with a torque
wrench. Failure to tighten the clamp collar to the proper torque
may result in movement between motor and reducer shafts and
cause premature wear on the shafts and keys.
FOR CLAMP COLLAR INPUT REDUCERS
(Reference Figure 1)
NEMA
Motor
Frame
Clamp
Bolt
Clamp Bolt
Tightening
Torque
Setscrew
Size
Set Screw
Tightening
Torque
56
M6
132 lb-in
(15 Nm)
M4
27 lb-in
(3 Nm)
140
M6
132 lb-in
(15 Nm)
M4
27 lb-in (
3 Nm)
180
M8
312 lb-in
(35 Nm)
M6
90 lb-in
(10 Nm)
IEC
Motor
Frame
Clamp
Bolt
Clamp Bolt
Tightening
Torque
Setscrew
Size
Set Screw
Tightening
Torque
80
M6
132 lb-in
(15 Nm)
M4
27 lb-in
(3 Nm)
90
M8
312 lb-in
(35 Nm)
M6
90 lb-in
(10 Nm)
100
M8
312 lb-in
(35 Nm)
M6
90 lb-in
(10 Nm)