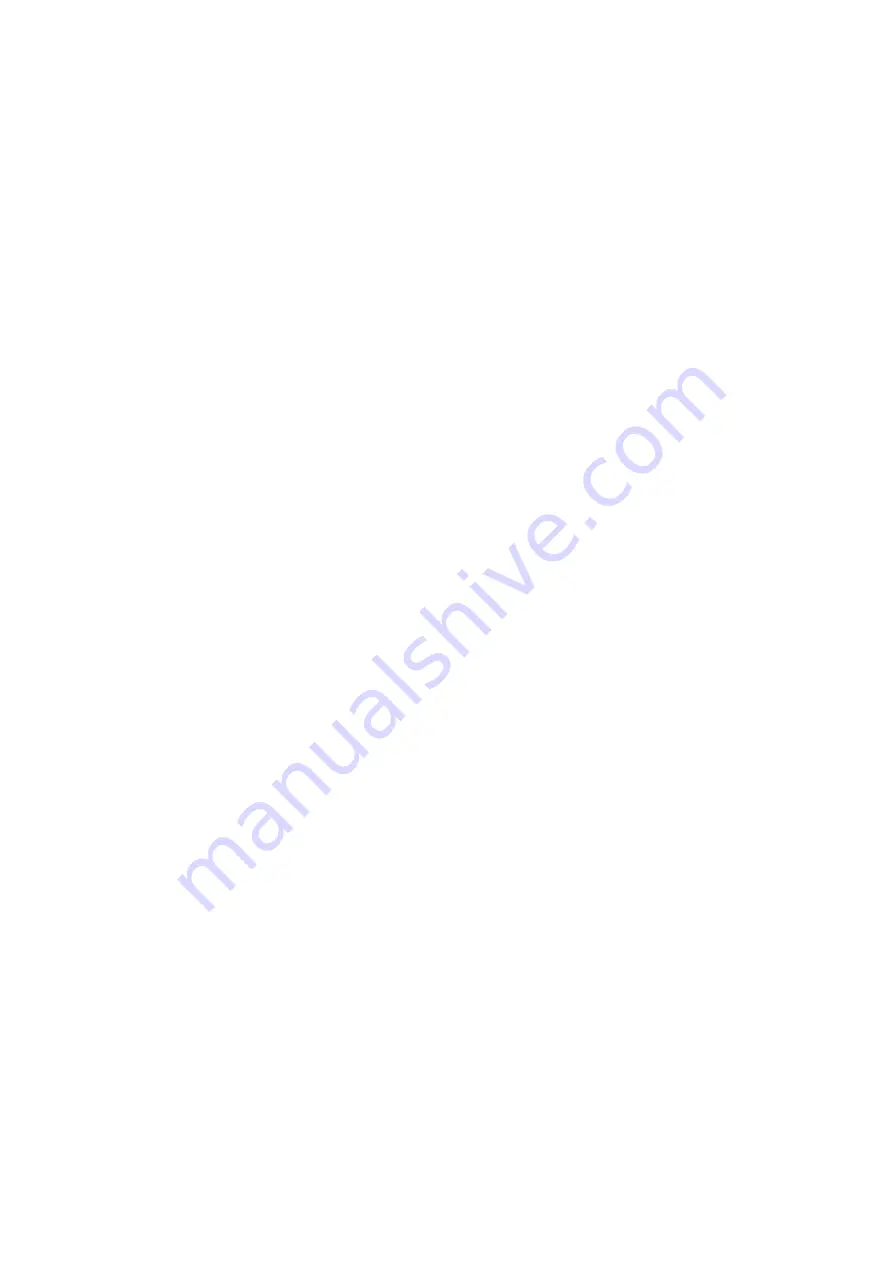
4
apron, and fire-resistant leggings. Avoid outer garments of untreated
cotton.
Bare skin protection:
Wear dark substantial clothing, Button
collar to protect chest and neck and button pockets to prevent entry
of sparks.
b) Eye and head protection
Protect eyes from exposure to arc. NEVER look at an electric arc
without protection. Welding helmet or shield containing a filter plate
shade no. 12 or denser must be used when welding. Place over face
before striking arc. Protect filter plate with a clear cover plate.
Cracked or broken helmet or shield should NOT be worn; radiation
can pass through to cause burns. Cracked, broken, or loose filter
plates must be replaced IMMEDIATELY. Replace clear cover plate
when broken, pitted, or spattered. WE SUGGEST you wear flash
goggles with side shields under the helmet, to give some protection
to the eyes should the helmet not be lowered over the face before an
arc is struck. Looking at an arc momentarily with unprotected eyes
(particularly a high intensity gas-shielded arc) can cause a retinal
burn that may leave a permanent dark area in the field of vision.
Before welding whilst wearing contact lenses, seek advice from your
optician.
c) Protection of nearby personnel
For production welding, a separate room or enclosed bay is best. In
open areas, surround the operation with low reflective, non-
combustible screens or panels. Allow for free air circulation,
particularly at floor level. Provide face shields for all persons who will
be looking directly at the weld. Others working in the area should
wear flash goggles. Before starting to weld, make sure that screen or
bay doors are closed.
5.3.2 Toxic fume prevention
Comply with precautions in 2B. Generator engine exhaust must be
vented to the outside air. Carbon monoxide can kill.
5.3.3 Fire and explosion prevention
Comply with precautions in 2C. Equipment’s rated capacity. Do not
overload arc welding equipment. It may overheat cables and cause a
fire. Loose cable connections may overheat or flash and cause a fire.
Never strike an arc on a cylinder or other pressure vessel. It creates a
brittle area that can cause a violent rupture or lead to such a rupture
later under rough handling.
5.3.4 Shock prevention
Exposed live conductors or other bare metal in the welding circuit, or
in unearthed, electrically-LIVE equipment can fatally shock a person
whose body becomes a conductor. DO NOT STAND, SIT, LIE, LEAN ON,
OR TOUCH a wet surface when welding, without suitable protection.
5.3.5 Protection for wearers of electronic life supp’t devices
(pacemakers)
Magnetic fields from high currents can affect pacemaker operation.
Persons wearing electronic life support equipment (pacemaker)
should consult with their doctor before going near arc welding,
gouging, or spot welding operations.
5.3.6 To protect against shock:
Keep body and clothing dry. Never work in damp area without
adequate insulation against electrical shock. Stay on a dry duckboard,
or rubber mat when dampness or sweat can not be avoided. Sweat,
sea water, or moisture between body and an electrically LIVE part -
or earthed metal - reduces the body surface electrical resistance,
enabling dangerous and possibly lethal currents to flow through the
body.
a) Earthing the equipment
When arc welding equipment is earthed according to the National
Electrical Code, and the workpiece is earthed, a voltage may exist
between the electrode and any conducting object.
Examples of conducting objects include, but are not limited to,
buildings, electrical tools, work benches, welding power source cases,
workpieces, etc. Never touch the electrode and any metal object
unless the welding power source is off. When installing, connect the
frames of each unit such as welding power source, control, work
table, and water circulator to the building earth.
Conductors must be adequate to carry earth currents safely.
Equipment made electrically LIVE by stray current may shock,
possibly fatally. Do NOT EARTH to electrical conduit, or to a pipe
carrying ANY gas or a flammable liquid such as oil or fuel.
b) Electrode holders
Fully insulated electrode holders should be used. Do NOT use holders
with protruding screws or with any form of damage.
c) Connectors
Fully insulated lock-type connectors should be used to join welding
cable.
d) Cables
Frequently inspect cables for wear, cracks and damage.
IMMEDIATELY REPLACE those with excessively worn or damaged
insulation to avoid possibly lethal shock from bared cable. Cables
with damaged areas may be taped to give resistance equivalent to
original cable. Keep cable dry, free of oil and grease, and protected
from hot metal and sparks.
e) Terminals and other exposed parts
Terminals and other exposed parts of electrical units should have
insulating covers secured before operation.
f) Electrode
a) Equipment with output on/off control (contactor) Welding power
sources for use with the gas metal arc welding, gas tungsten arc
welding and similar processes normally are equipped with devices
that permit on/off control of the welding power output. When so
equipped the electrode wire becomes electrically LIVE when the
power source switch is ON and welding gun switch is closed. Never
touch the electrode wire or any conducting object in contact with the