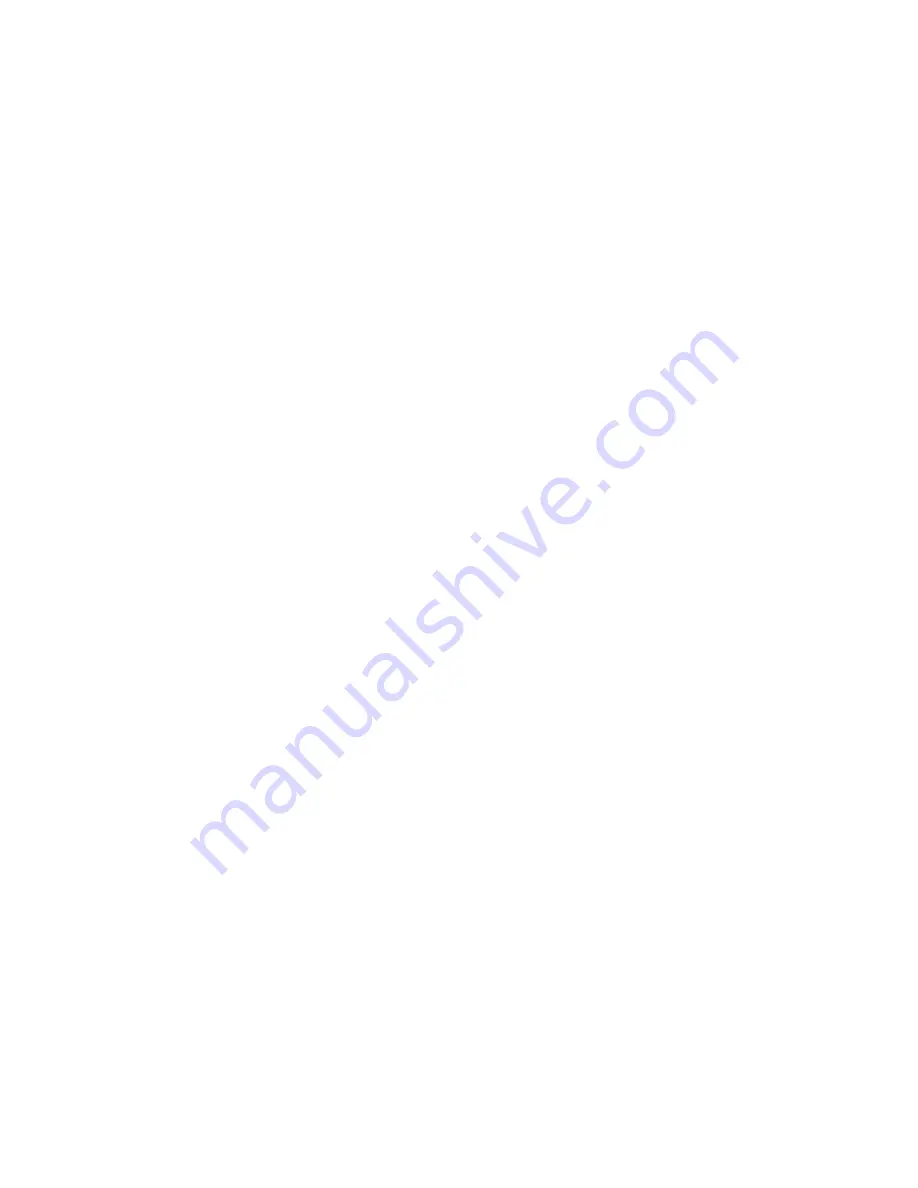
19
cal properties, precautionary measures to take, and first aid measures as stated in the Safety Summary before
performing any maintenance with the hydraulic system.
4.
Oil level too low. Oil level should be just under the vent cap port when the lift is down. Relieve all hydrau
LICPRESSUREANDADDOILASREQUIRED
s
Oil Blows out Breather of Power Unit
)FOILBLOWSOUTOFTHEBREATHEROFTHEPOWERUNITTAKETHEFOLLOWINGACTIONS
/ILRESERVOIROVERlLLED2ELIEVEALLPRESSUREANDSIPHONOUTHYDRAULICmUIDUNTILATAPROPERLEVEL
,IFTLOWEREDTOOQUICKLYWHILEUNDERAHEAVYLOAD,OWERTHELIFTSLOWLYUNDERHEAVYLOADS
s
Motor Hums and Will Not Run
)FTHEMOTORHUMSBUTFAILSTORUNTAKETHEFOLLOWINGACTIONS
,IFTOVERLOADED2EMOVEEXCESSIVEWEIGHTFROMLIFT
7!2.).'
4HEVOLTAGESUSEDINTHELIFTCANCAUSEDEATHORINJURYTOPERSONNEL)NTHEFOLLOWINGSTEPSMAKESURETHATA
QUALIlEDELECTRICIANISUSEDTOPERFORMMAINTENANCE
2.
Faulty wiring..….... Call electrician
"ADCAPACITORx#ALLELECTRICIAN
4.
Low voltage........... Call electrician
s
,IFT*ERKS'OING5PAND$OWN
1.
If the lift jerks while going up and down, it is usually a sign of air in the hydraulic system. Raise lift all the
WAYTOTOPANDRETURNTOmOOR2EPEATTIMES$ONOTLETTHISOVERHEATPOWERUNIT
s
/IL,EAKS
/ILLEAKCAUSESATTHEPOWERUNITANDCYLINDERSARENORMALLYCAUSEDBYTHEFOLLOWING
0OWERUNITIFTHEPOWERUNITLEAKSHYDRAULICOILAROUNDTHETANKMOUNTINGmANGECHECKTHEOILLEVELINTHE