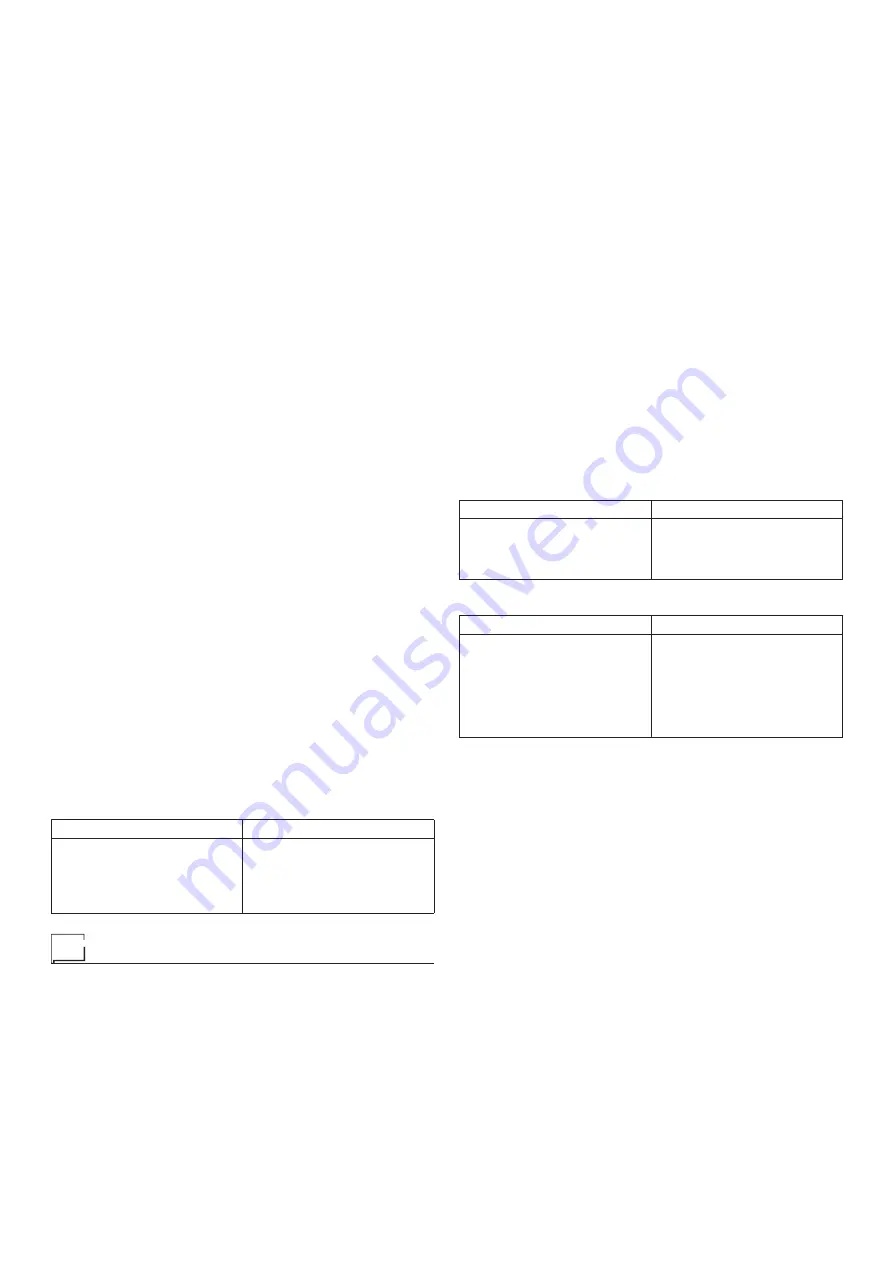
7
TIG WELDING WITH “Lift” TYPE STRIKING
4a) Open the gas cylinder and flow regulator.
5a) Put the electrode at the point at which welding is to begin, put
the TIG torch at an angle so that the edge of the gas nozzle
is not on top of the piece to be welded, keeping contact be-
tween the point of the electrode and the piece to be welded
(Fig. D-1).
6a) Press the torch button.
7a) The “Lift” function strikes the arc when the TIG torch electrode
comes into contact with the workpiece and is then removed
(Fig. D-2)
8a) Carry out TIG welding (Fig. D-3).
To end welding:
•
Lift the torch slowly, at a certain point the welding current
decreases, and then stop.
•
The welding power source follows an automatic down slope
along with extinguishing of the arc.
9a) When finished welding remember to shut off the gas cylinder.
TIG WELDING WITH HIGH FREQUENCY STRIKING (HF)
4b) Open the gas cylinder and flow regulator.
5b) Put the electrode at the point at which welding is to begin, put
the TIG torch at an angle so that the edge of the gas nozzle is
not on top of the piece to be welded, keeping a 2-3 mm gap
between the point of the electrode and the piece to be weld-
ed (Fig. E-1).
6b) Press the torch button.
7b) The voltaic arc strikes even without contact between the TIG
torch electrode and the workpiece (Fig. E-2).
8b) To continue welding put the torch back in its normal position
(Fig. E-3).
IMPORTANT: The high frequency switches off automatically af-
ter switching on.
PART TO BE WELDED
The part to be welded must always be connected to ground in or-
der to reduce electromagnetic emission. Much attention must be
afforded so that the ground connection of the part to be welded
does not increase the risk of accident to the user or the risk of dam-
age to other electric equipment. When it is necessary to connect
the part to be welded to ground, you should make a direct con-
nection between the part and the ground shaft. In those countries
in which such a connection is not allowed, connect the part to be
welded to ground using suitable capacitors, in compliance with the
national regulations.
WELDING PARAMETERS
Table 3 shows the currents to use with the respective electrodes
for TIG welding. This input is not absolute but is for your guidance
only; read the electrode manufacturers’ instructions for a specific
choice. The diameter of the electrode to use is directly proportion-
al to the current being used for welding.
Table 3
Ø ELECTRODE (mm)
CURRENT (A)
1,2
1,6
2,4
3,2
4,0
10 ÷ 80
70 ÷ 150
140 ÷ 250
225 ÷ 400
300 ÷ 500
Electrode welding (MMA)
The welding electrode is used to weld most metals (various types
steel, etc.),for which rutilic and basic electrodes are used.
1) Connecting the welding cables (Fig. F):
Disconnect the welding power source from the mains power
supply and connect the welding cables to the output terminals
(Positive and Negative) of the welding power source, attaching
them to the clamp and ground with the polarity specified for the
type of electrode being used (Fig.F). Always follow the elec-
trode manufacturer’s instructions. The welding cables must be
as short as possible, they must be near to one another, posi-
tioned at or near floor level. Do not touch the electrode clamp
and the ground clamp simultaneously.
2) Switch the welding power source on by moving the power sup-
ply switch to
I
(Pos. 6, Fig. A).
3) Make the adjustments and select the parameters on the con-
trol panel (for further information see the control panel manu-
al).
4) Carry out welding by moving the torch to the workpiece. Strike
the arc (press the electrode quickly against the metal and then
lift it) to melt the electrode, the coating of which forms a protec-
tive residue. Then continue welding by moving the electrode
from left to right, inclining it by about 60° compared with the
metal in relation to the direction of welding.
PART TO BE WELDED
The part to be welded must always be connected to ground in or-
der to reduce electromagnetic emission. Much attention must be
afforded so that the ground connection of the part to be welded
does not increase the risk of accident to the user or the risk of dam-
age to other electric equipment. When it is necessary to connect
the part to be welded to ground, you should make a direct con-
nection between the part and the ground shaft. In those countries
in which such a connection is not allowed, connect the part to be
welded to ground using suitable capacitors, in compliance with the
national regulations.
WELDING PARAMETERS
Table 4 shows some general indications for the choice of elec-
trode, based on the thickness of the parts to be welded. The val-
ues of current to use are shown in table 5 with the respective
electrodes for the welding of common steels and low-grade al-
loys. These data have no absolute value and are indicative data
only. For a precise choice follow the instructions provided by the
electrode manufacturer.
Table 4
WELDING THICKNESS (mm)
Ø ELECTRODE (mm)
1,5 ÷ 3
3 ÷ 5
5 ÷ 12
≥ 12
2
2,5
3,2
4
Table 5
Ø ELECTRODE (mm)
CURRENT (A)
1,6
2
2,5
3,2
4
5
6
30 ÷ 60
40 ÷ 75
60 ÷ 110
95 ÷ 140
140 ÷ 190
190 ÷ 240
220 ÷ 330
The current to be used depends on the welding positions and the
type of joint, and it increases according to the thickness and di-
mensions of the part.
The current intensity to be used for the different types of welding,
within the field of regulation shown in table 5 is:
•
High for plane, frontal plane and vertical upwards welding.
•
Medium for overhead welding.
•
Low for vertical downwards welding and for joining small pre-
heated pieces.
A fairly approximate indication of the average current to use in
the welding of electrodes for ordinary steel is given by the follow-
ing formula:
I = 50 × (Øe - 1)
Where:
I = intensity of the welding current
Øe = electrode diameter
Example:
For electrode diameter 4 mm
I = 50 × (4 - 1) = 50 × 3 = 150A
Summary of Contents for DIX TIG GO 1906.M HF
Page 5: ...5 FIG A ...
Page 10: ...10 Wiring diagram DIX TIG GO 1906 M HF ...
Page 11: ...11 2101WA31 ...
Page 12: ...12 Wiring diagram DIX TIG GO 2506 M HF ...
Page 13: ...13 2101WB24 ...