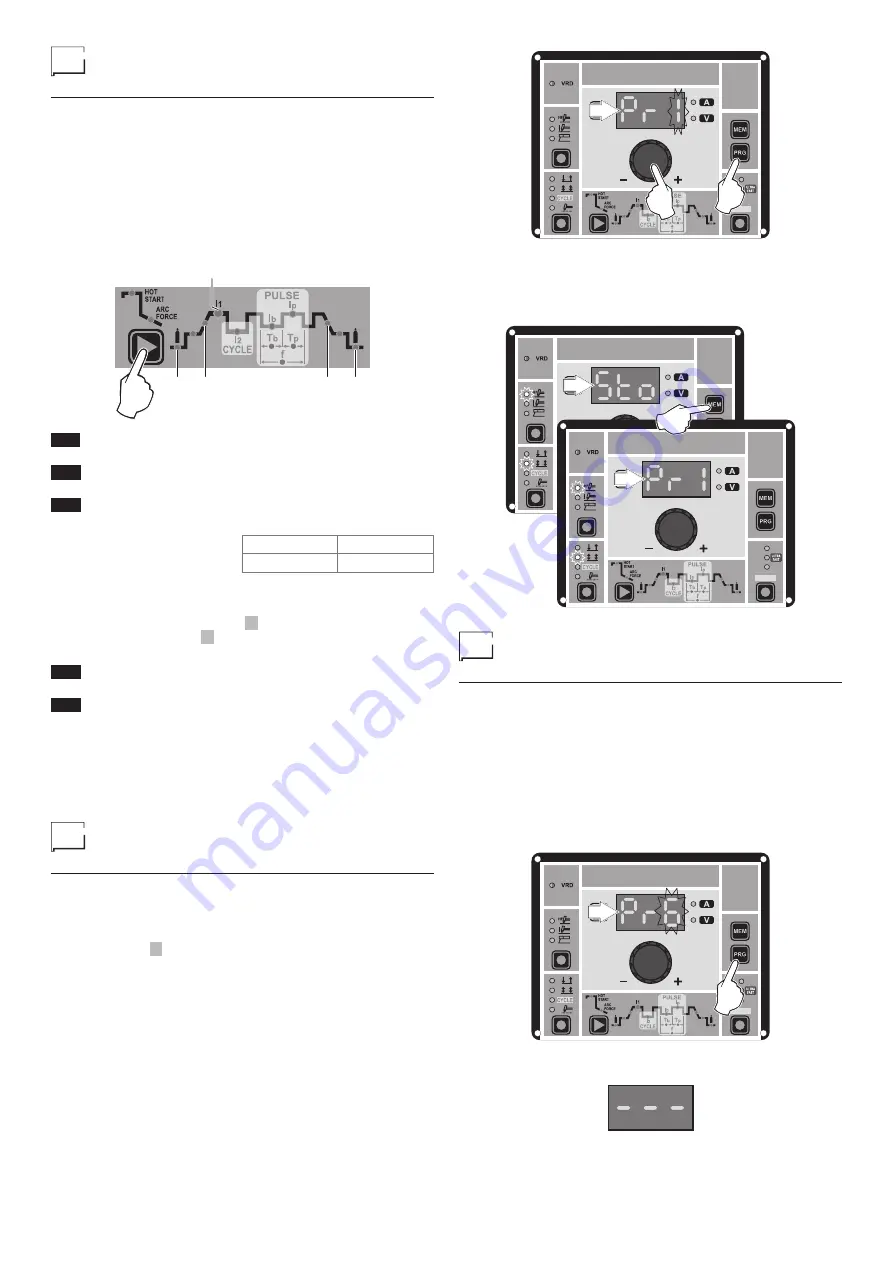
24
Editing the maximum and minimum
limits for welding parameters
Welding power source in STANDARD (Std) configuration:
During TIG welding with HF ignition, the units allow you to modify
the MINIMUM and MAXIMUM LIMITS for some WELDING
PARAMETERS, thereby providing a more skilled welder and a
more versatile welding power source.
Proceed as follows:
1) Switch on the welding power source holding down the WELD-
ING PARAMETERS SELECTION key (T7).
2) Press the WELDING PARAMETERS SELECTION Key (T7)
a number of times to set the limits for the following welding
parameters:
L10
L16
L15
L12
L11
T7
L11
PRE-GAS duration (maximum limit settable from 1,00
to 2,50 sec)
L12
SLOPE UP duration (maximum limit settable from 5,00
to 10,0 sec)
L10
MINIMUM CURRENT for remote controls - minimum
limit settable:
1906.M HF
2506.M HF
5 ÷ 220 A
5 ÷ 300 A
WARNING: If the minimum limit setting (for the remote control
MINIMUM CURRENT) is greater than or equal to the value for the
PRINCIPAL welding CURRENT I
1
, you will weld at the PRINCI-
PAL welding CURRENT I
1
, irrespective of the setting you have
chosen for the remote control.
L15
SLOPE DOWN duration (maximum limit settable from
8,00 to 15,0 sec)
L16
POST-GAS duration (maximum limit settable from 10,0
to 25,0 sec)
To exit the setting phase, hold the WELDING PARAMETERS
SELECTION key (T7) down for about
1 second
. The values set
are now active and welding can begin.
Creating and memorising automatic
welding points
Once you have defined the parameters the operator requires to do
their work properly, you can save them in the memory and create
a WELDING PROGRAM by proceeding as follows.
WARNING: To access the setting saving phase, the PRINCIPAL
CURRENT LED I
1
must be switched on without flashing.
1) Hold the “PRG” PROGRAM Key (T2) down for at least
5
con-
secutive seconds until the DISPLAY (D) reads
Pr
, accom-
panied by a flashing number (e.g. Pr 1).
In order to be able to choose WELDING PROGRAM that is
free, simply rotate the ENCODER knob (E) and look for a
program for which the control panel has all the LEDs for the
various settings switched off.
It is also possible to overwrite a program already saved.
PULSE
SYN
FAST
SLOW
T2
D
E
2) To SAVE the PROGRAM hold the “MEM” SAVE Key (T1) down
until the DISPLAY reads
“Sto”
.
3) The WELDING PROGRAM has now been saved and its num-
ber appears in the DISPLAY (D) along with the other settings
saved (corresponding LEDs on without flashing).
PULSE
SYN
FAST
SLOW
PULSE
SYN
FAST
SLOW
D
T1
D
PROGRAMMED and/or
MANUAL welding
PROGRAMMED WELDING
When the WELDING PROGRAM has been saved, the operator
can weld using only pre-set values as they cannot edit any type
of parameter/function. To edit, switch to MANUAL welding mode.
MANUAL WELDING
To go back to set/edit the parameters selected or to create a new
program, proceed as follows:
1) Hold the “PRG” PROGRAM Key (T2) down (about
3
sec-
onds) until the DISPLAY (D) shows the number of the program
selected flashing (e.g.
Pr6
).
PULSE
SYN
FAST
SLOW
T2
D
2) Turn the ENCODER Key (E) anticlockwise until the DISPLAY
(D) shows 3 dashes.
3) Press and release the “PRG” PROGRAM key (T2) and the
welding power source goes back to the initial operation con-
dition.
Summary of Contents for DIX TIG GO 1906.M HF
Page 5: ...5 FIG A ...
Page 10: ...10 Wiring diagram DIX TIG GO 1906 M HF ...
Page 11: ...11 2101WA31 ...
Page 12: ...12 Wiring diagram DIX TIG GO 2506 M HF ...
Page 13: ...13 2101WB24 ...