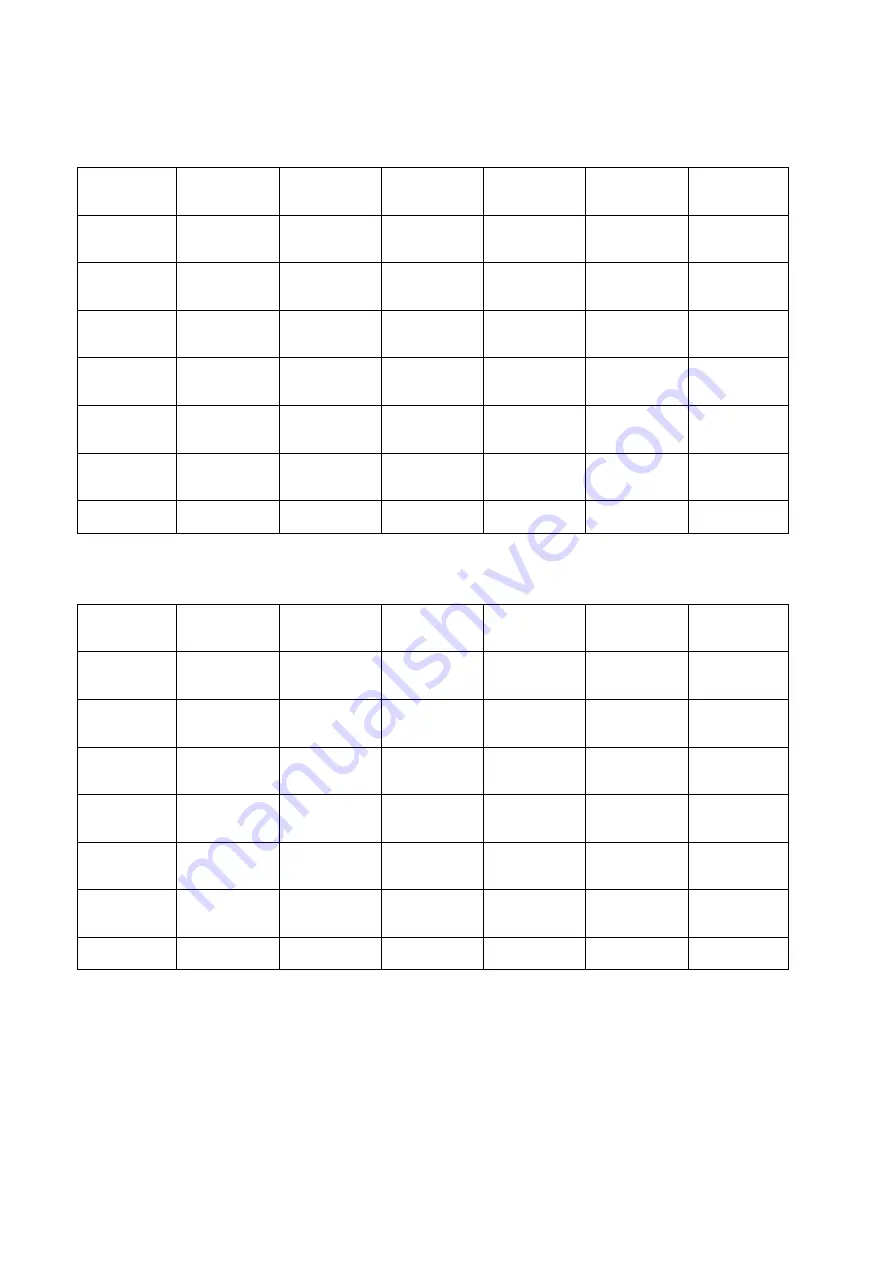
12
Lead temperature curve welding
41*41 BGA welding temperature setting
38*38 BGA welding temperature setting
31*31 BGA welding temperature setting
Preheating
Constant
Heating
Welding
1st
Welding
2nd
Reduction
Upper
heating
160
185
210
220
225
0
Constant
time
30
30
35
40
20
0
Bottom
heating
165
190
215
225
230
0
Constant
time
30
30
35
40
70
0
IR
preheating
110
120
130
140
150
0
Constant
time
30
30
35
40
70
0
Speed rate
2
2
2
2
2
0
Preheating
Constant
Heating
Welding
1st
Welding
2nd
Reduction
Upper
heating
160
185
210
215
220
0
Constant
time
30
30
35
40
20
0
Bottom
heating
160
185
215
220
225
0
Constant
time
30
30
35
40
40
0
IR
preheating
110
120
130
140
150
0
Constant
time
30
30
35
40
70
0
Speed rate
2
2
2
2
2
0