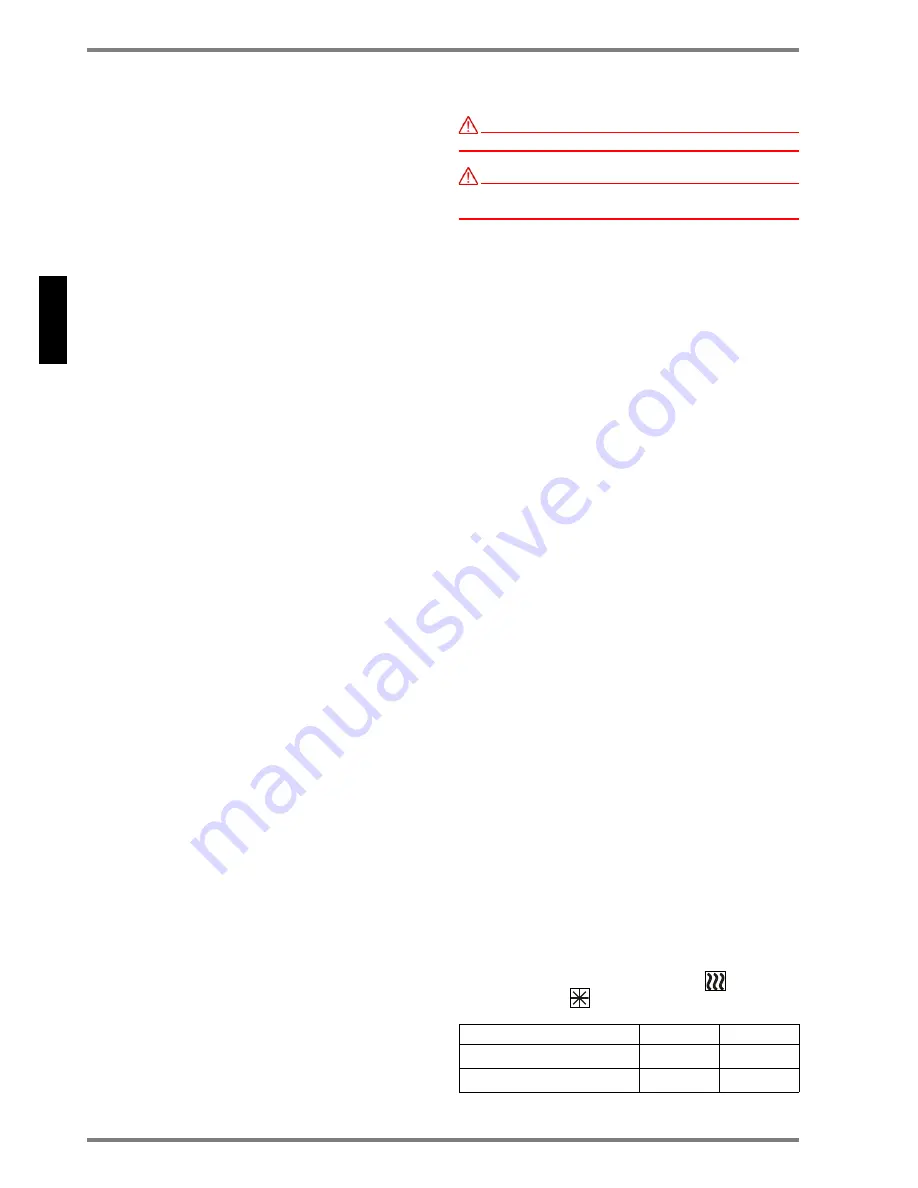
EN-18 SRX_C_gb · 09/15/B
www.dimplex.de/en
Englis
h
SRX 070ECM, SRX 120ECM, SRX 160ECM
3. Installation preparation
Remove packaging material.
Unscrew the four fixing screws from underside of de-
vice (see fig. 2) to remove casing cover. Store the cas-
ing cover such that it cannot be damaged during instal-
lation.
During installation of the appliance - a helpful tip is to
use the plastic packaging and carton to cover the
appliance after it is installed - this prevents any building
materials such as plaster or paint entering the
appliance during renovation work on the property.
4. Fixing to the wall
For drywalls, use suitable fixing material (not supplied)!
Draw and drill four holes on a sturdy wall as shown in
fig. 5(b). All dimensions are in mm.
Insert dowels and pre-fit the two top screws (don't com-
pletely screw in yet).
Hang device on the two top screws.
Insert and tighten the two bottom screws, then tighten
the two top screws.
5. Hydraulic connection
To ensure a sufficient heating water flow rate through
the fan convectors, observe the following points:
The devices are not suitable for installation in sin-
gle-pipe systems.
The nominal width of the connection pipe must
have a minimum diameter of 15 mm.
If the devices are installed in a heating system with
various heat distribution systems (e.g. underfloor
heating), a separate circuit is required to guarantee
a sufficient water flow rate.
For optimum operation (heat output) of the fan con-
vectors, a hydraulic balance is required on the
heating system.
Fig. 6 shows the various hydraulic connection options
on the device. The recommended flow and return con-
nections are shown in fig. 6. The heating pipes can be
laid in the floor or in the wall. The device is supplied
with two copper pipes with a diameter of 15 mm that
are fitted on the heat exchanger at the factory.
Insulate the water flow and return pipe work.
Before and during filling of the heating system, all pipe
connections must be checked for leaks. During filling,
the bleeder valve (see fig. 5(c)) must be open such that
air can escape from the device. If necessary, bleed
again following commissioning (circulating pump run-
ning).
Connect the condensate pipe supplied to the outlet
nozzle and route to a suitable outlet with a gradient of a
least 5°C. (see fig. 10)
As an optional connection kit VS SRX with flow and re-
turn pipe and a valve block with actuator ETS DWU is
available.
There should be little or no water in the drip tray during
operation. All water flows out (see fig.11).
6. Electrical connection
ATTENTION!
The device must be grounded!
ATTENTION!
Phase conductor (brown) and neutral conductor (blue)
must not be swapped as this may cause malfunctions.
The electrical connection should have a supply voltage
of ~100-250V, 50/60 Hz.
The device must be installed by a qualified electrician
in compliance with the existing standards and local in-
stallation guidelines. Before performing installation, en-
sure that the power supply is switched off.
The device is equipped with a flexible 1 m connection
cable (4 x 0.75 mm²), which can be used to connect the
heater directly to the power supply via a suitable wall
socket.
In the electrical supply line, fit a circuit breaker for each
pole with a contact opening width of at least 3 mm. Au-
tomatic fuses are also permitted as separators with de-
layed tripping characteristic.
6.1 Conductor configuration of the connection cable:
Brown: 'L' – supply voltage phase conductor
Blue: 'N' – supply voltage neutral conductor
Green/yellow: 'PE' grounding conductor
Black: control conductor (temperature reduction;on/off)
For circuit diagram, see fig. 8.
Control conductor
The black control conductor has the following functions:
6.2 Lowering temperature using an external timer
or switch
By activating the control conductor, see fig. 8 on the
left, the set target temperature on the device is low-
ered.
The temperature reduction is forwarded to any down-
stream devices via the control conductor.
6.3 Operation with programming cassette
The control signals of the programming cassette, which
is plugged into the pilot device, are forwarded to any
downstream devices via the control conductor, see fig.
9 on the right.
How the set temperature is changed depends on the
selected operating mode:
In heating mode the set temperature is lowered
In cooling mode the set temperature is increased
If there is a control signal, then depending on the
selected mode, either the indicator lamp
(heating) or
the indicator light
(cooling) changes colour.
Programming
ON / OF
Lowering
RXPW 1 (7 day timer)
YES
NO
RXTI 24 (24 hours timer)
YES
NO