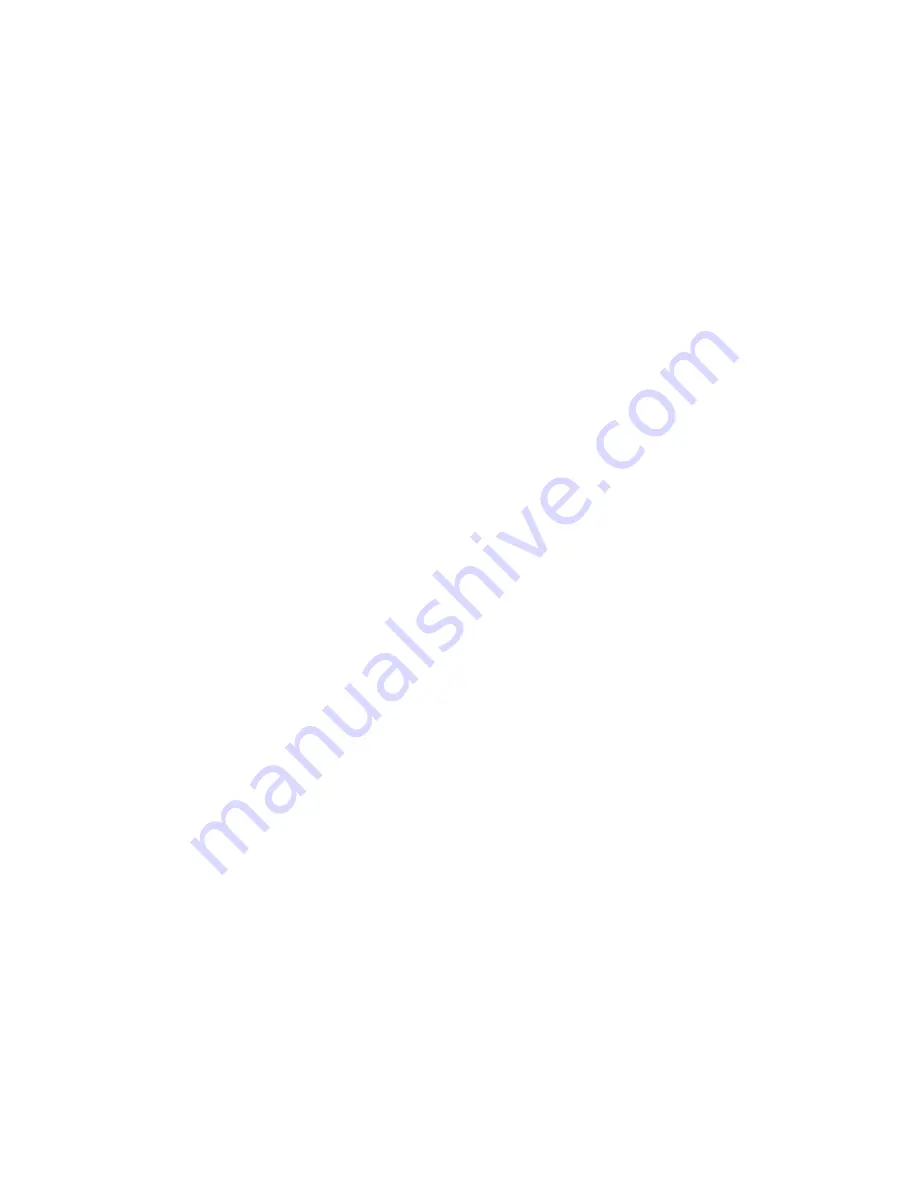
6
Photoresist is then put on top of the ITO coating and a photolithographic process is used to image the pattern. The exposed patterns are then developed and the glass is sent through an acid bath
where the excess ITO is removed, similar to the way a PC board is made. The remaining photoresist is then stripped away and the patterned segment and common plane electrodes remain on the
glass.
The next layer to be applied is the liquid crystal alignment layer. This is usually a polyimide type material and has been chosen for its environmental stability in high moisture and heat. More
importantly is its ability to cause the molecules of liquid crystal to align their long axis in the direction in which the polymer has been buffed.
We rub the two halves of the display at right angles to one another and since the liquid crystal molecules like to arrange themselves parallel to one another, we cause a helical structure to be
formed between the two electrode faces, see Fig 2 below. This helical structure forms a 90
o
rotation of the liquid crystal molecules from the top of the display to the bottom.
After the polymer is rubbed, a thermoplastic seal is printed along the perimeter of one piece of glass. This is a resin based material with a high curing temperature, about 200
o
C, that creates an
extremely durable barrier to outside moisture and contamination. Some manufacturers use a UV cured material for this seal as it speeds up the manufacturing process.
We then apply a crossover dot, usually a small spot of silver, to connect the common plane electrode on the top piece of glass to the segment plane which is on the bottom piece of glass. This is
somewhat analogous to a plated thru hole on a PC board.
To make the display uniform in appearance, spacers are then applied. These are usually glass or plastic spheres that have the desired diameter to produce a fixed gap between the glass plates.
Depending on the liquid crystal used, this gap can be between 4 and 8 microns.
The two halves of the display are then aligned, usually with a three point camera alignment system for accuracy, and brought together. A very thin, uniform, flat and empty bottle has been formed
with the thermoplastic seal essentially "gluing" the two pieces of glass together.
A liquid crystal is put inside this bottle by using a vacuum filling technique. The liquid crystal (the dielectric material of our capacitor) is selected for it's various physical properties. The
application may call for a liquid crystal fluid that has a very low operating voltage or the display may be used outdoors and require a very wide temperature range. Display manufacturers have
developed several liquid crystal mixtures to fulfill most applications.
Once the liquid crystal has been put inside the display and the port opening has been sealed, a polarizer is put on the front of the top glass and a second polarizer is put on the back of the bottom
glass to make sure that the light reaching the eye of the observer is oriented along the correct axis.