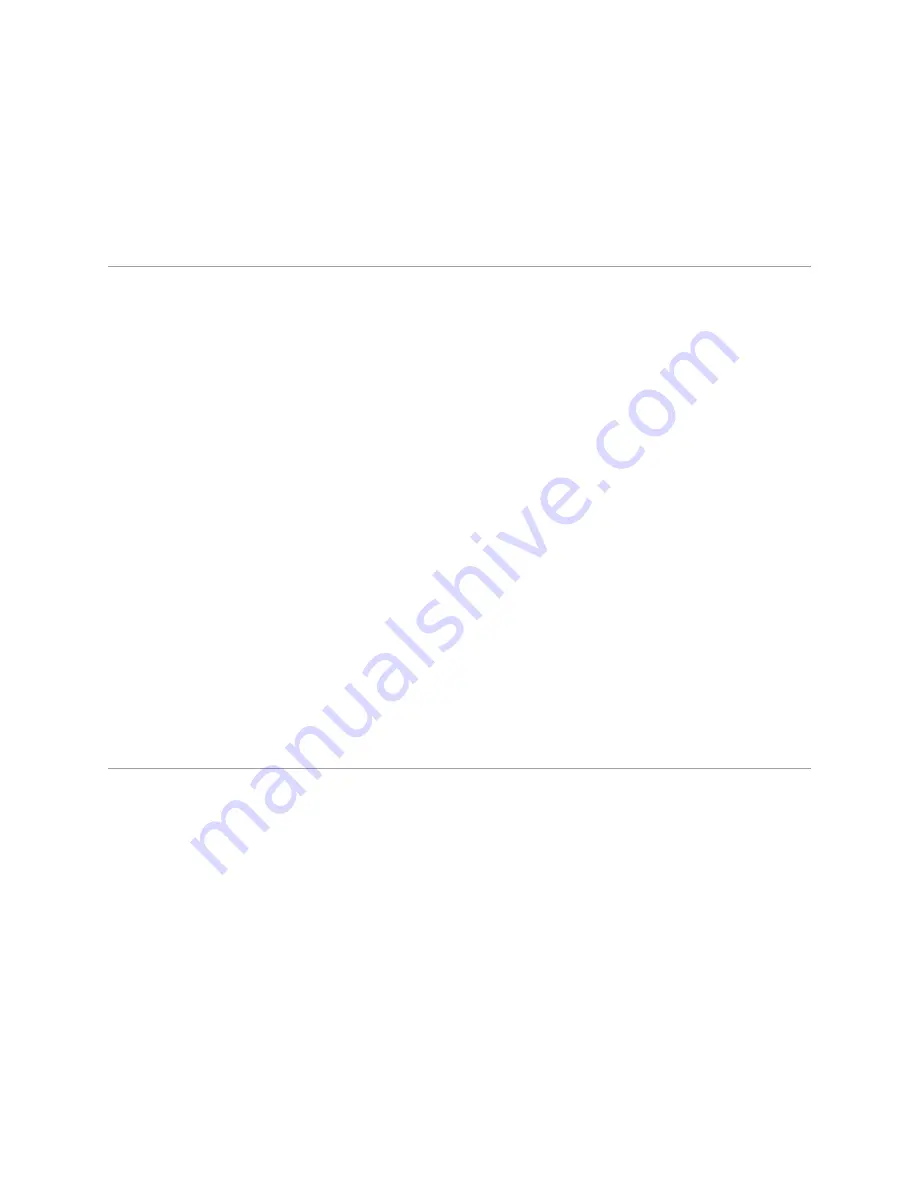
Valid CAN Control Frame received
within the last 100ms. The specified
control mode resulted in a Negative
Duty Cycle being Motor Output
LEDs blink Red in a counter-clockwise circular pattern
(LED1
→
LED4
→
LED3
→
LED2
→
LED1). The LED
update rate is proportional to the duty cycle of the output
and increases with increased duty cycle. At 100% duty
cycle, all 4 LEDs are illuminated Red.
5 Brake / Coast Mode
The DMC60C's response when a neutral duty cycle is applied to the output depends on the
Brake/Coast setting. When the DMC60C is configured for Brake Mode, the M+ and M- leads are
internally shorted when a neutral duty cycle is applied to the output, which causes an attached motor
to resist rotation. If an attached motor is spinning, then its speed decreases at a much quicker rate
than it would if the M+ and M- leads were allowed to float. When configured for Coast Mode, the M+
and M- leads float when a neutral duty cycle is applied to the output.
The current Brake/Coast setting is displayed by the Brake/Coast CAL LED, which is in the center of
the triangle located at the center of the housing. When the device is operating in Brake Mode, the
LED is illuminated Red. When the device is operating in Coast Mode, the LED is off. The
Brake/Coast setting can be toggled by pressing down on the center of the triangle, then releasing
the button.
The Brake/Coast setting is stored in non-volatile memory and is re-stored automatically after power
cycles.
When the DMC60C is connected to a CAN bus the Brake/Coast setting may be overridden by the
CAN control frame. When the Brake/Coast override is active the Brake/Coast CAL LED is overridden
to display the setting specified by the CAN control frame. During this time the DMC60C employs the
Brake/Coast mode that is specified in the CAN frame when applying the neutral duty cycle to the
output.
6 Input Signal Calibration
The DMC60C accepts PWM input signals with a positive pulse width between 0.6 and 2.4
milliseconds. Due to variations in controllers, it may be necessary to adjust, or calibrate, the pulse
widths that correspond to the maximum forward and reverse duty cycles, as well as the neutral input.
To perform calibration, follow these steps:
1. Press and hold the Brake/Coast CAL button. After approximately 5 seconds, the top and
bottom LEDs will begin to alternate between Blue and Off. This indicates that calibration has
started.
2. While continuing to hold the button, use the controller to move between full forward and
full reverse (perhaps by moving a joystick), making sure to reach both extremes. This may
be repeated more than once, but there is no required minimum.