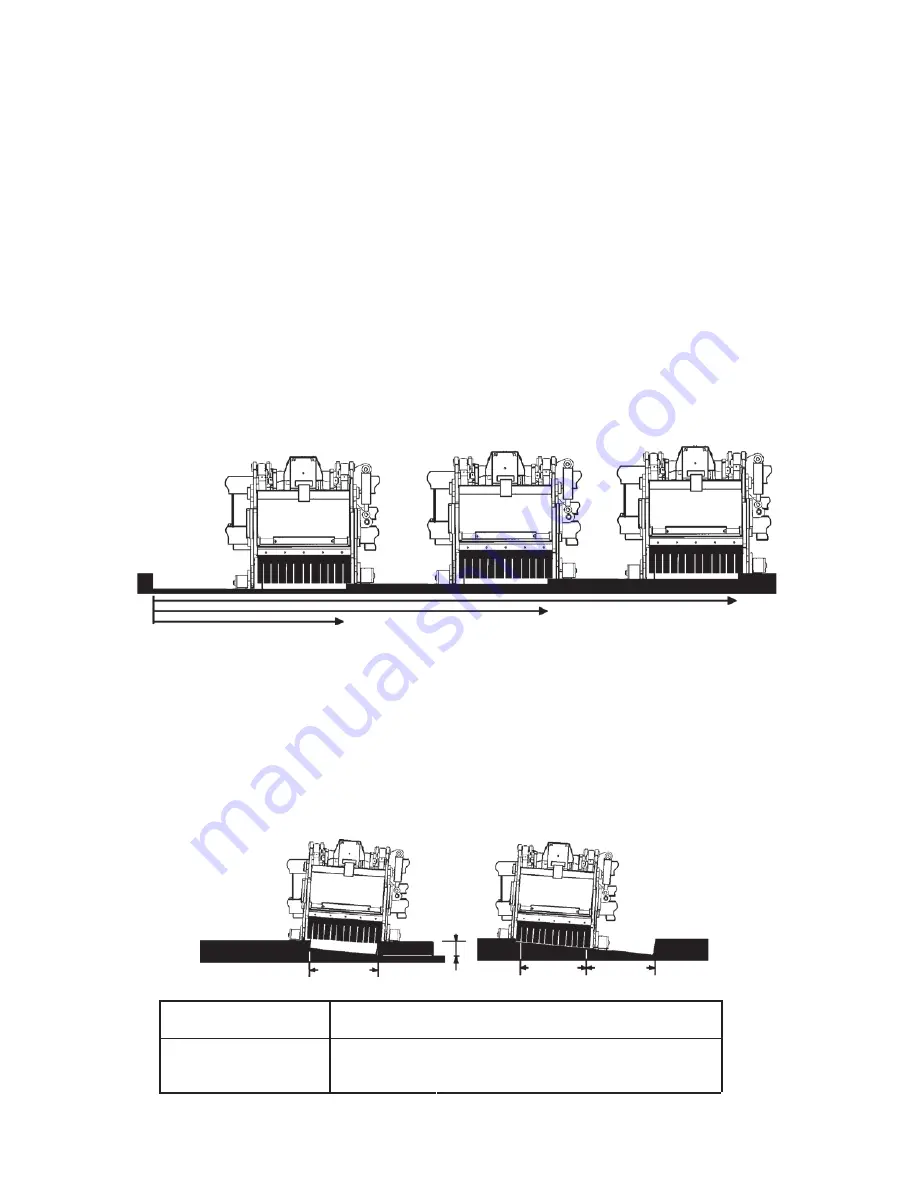
OPERATING INSTRUCTIONS
DEEP CUTS
To achieve a deep cut the width of the drum, make the first cut at the recommended depth for the material
being milled and then reposition the profiler at the beginning of the pass and reset for double the
recommended depth.
Example: Make the first cut with the depth controls set at 50mm and then set the depth control at 100mm
for the second pass and so on and so forth until the desired depth is obtained. To achieve a 150mm cut
of a large area it is recommended to cut the entire area at the recommended depth and then clear the
spoil from the area before making the second cut.
Removing the spoil between cuts will enhance the productivity of the profiler and maintain an even cut.
If trying to achieve a critical cutting depth it is recommended that the spoil from one cut be cleared away
before making another pass. This will eliminate the possibility of the profiler riding on and off the spoil
and creating an uneven surface.
REMOVE SPOIL
AFTER
3rd PASS
REMOVE SPOIL
AFTER
2nd PASS
REMOVE SPOIL
AFTER
1st PASS
3rd PASS
2nd
PASS
1st PASS
MILLING TAPER CUTS
When adding to or joining new paved surfaces to existing paving, a taper cut may be required at the
interacting joints so the new paving would appear seamless. See the chart below for the angle of cut
per size of
road profiler.
Example:
To achieve a taper cut from 0-100mm over a 1200mm distance with a 600mm wide road
profiler it is recommended that you set one side of the profiler at 50mm and the other at 100mm and the
tilt set at 4° for the first pass. Then make a second pass with both sides of the p
rofiler
set at 0mm and
the tilt still at 4°.
1st
PASS
100mm
2nd
PASS
1st
PASS
MODEL
25mm
ANGLE OF CUT PER OFFSET
50mm
75mm
100mm
450mm Road Profiler
3°
6°
8°
N
/
A
600mm Road Profiler
2°
4°
6°
N
/
A
PM-000068-A DECEMBER 2017
19
Summary of Contents for HP450
Page 1: ...OPERATOR S MANUAL HP450 HP600 ROAD PROFILERS FOR SKID STEER LOADERS PM 000068 A DECEMBER 2017...
Page 2: ...THIS PAGE IS INTENTIONALLY BLANK PM 000068 A DECEMBER 2017...
Page 4: ...THIS PAGE IS INTENTIONALLY BLANK PM 000068 A DECEMBER 2017 2...
Page 36: ...THIS PAGE IS INTENTIONALLY BLANK PM 000068 A DECEMBER 2017 34...