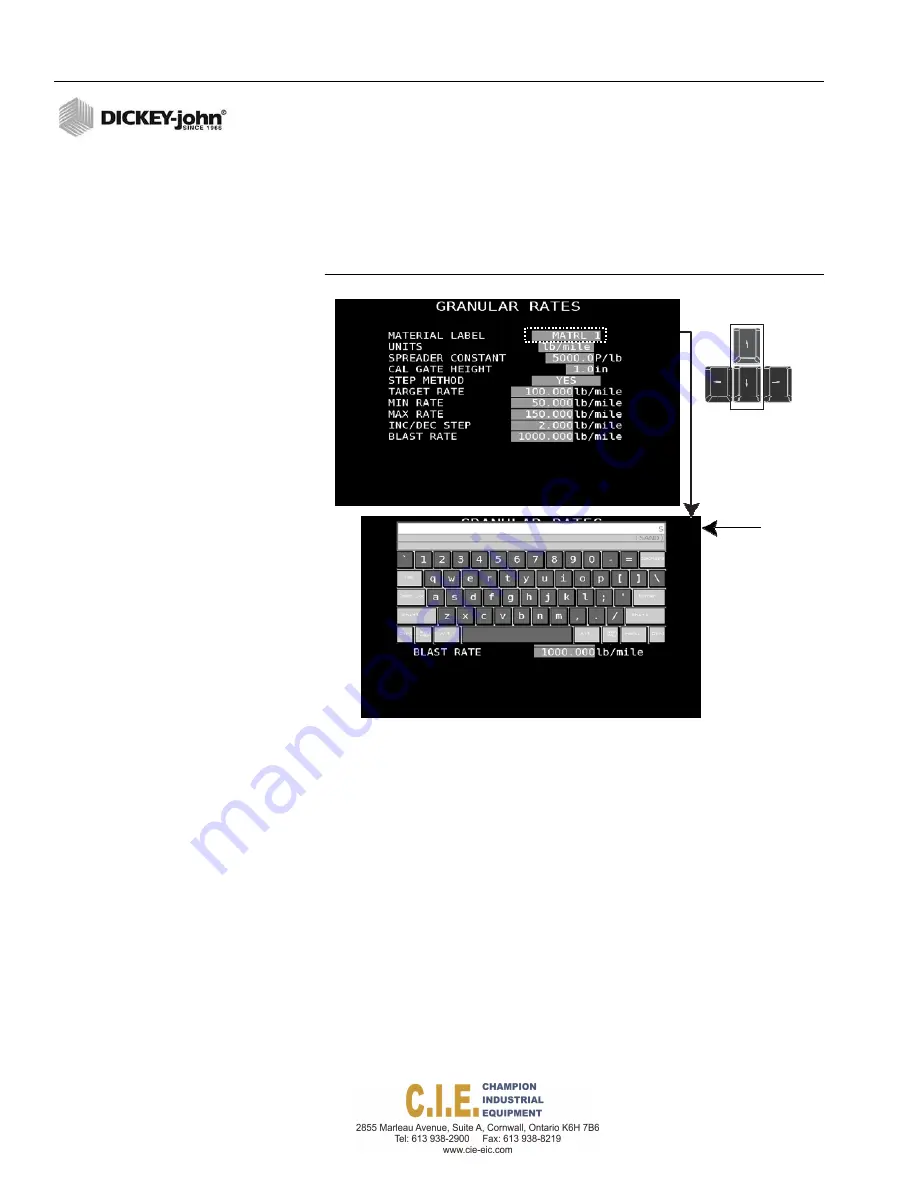
OPERATOR’S MANUAL
NOTE: The Enter button will not select
a text field.
LABEL ENTRIES
1. To create label names, such as a Material Name, highlight the field and
begin typing the name. A virtual keyboard displays onscreen and the
name as entered appears at top of the virtual keyboard.
2. Press the
Enter
button to accept the label entry.
Figure 49
Virtual Keyboard
Using
the
keyboard
up/down
arrow
buttons
select
and
highlight
a
parameter
Material
Label
50 / FLEX4 PROTM PROGRAMMING
Flex4 Pro
TM
Control System
6010541 Rev A
Summary of Contents for Flex4
Page 1: ...FLEX4 PRO PUBLIC WORKS CONTROL SYSTEM Operator s Manual SINCE 1966 FLEX PRO...
Page 5: ...OPERATOR S MANUAL Flex4 ProTM Control System 6010541 Rev A SAFETY NOTICES 2...
Page 7: ...OPERATOR S MANUAL 4 INTRODUCTION Flex4 ProTM Control System 6010541 Rev A...
Page 29: ...OPERATOR S MANUAL 26 INSTALLATION Flex4 ProTM Control System 6010541 Rev A...
Page 49: ...OPERATOR S MANUAL 46 OPERATION Flex4 ProTM Control System 6010541 Rev A...
Page 55: ...OPERATOR S MANUAL 52 FLEX4 PROTM PROGRAMMING Flex4 ProTM Control System 6010541 Rev A...
Page 105: ...OPERATOR S MANUAL 102 SYSTEM PROGRAMMING Flex4 ProTM Control System 6010541 Rev A...
Page 123: ...OPERATOR S MANUAL 120 CALIBRATIONS Flex4 ProTM Control System 6010541 Rev A...
Page 131: ...OPERATOR S MANUAL 128 CAPTURE SCREEN SHOT Flex4 ProTM Control System 6010541 Rev A...
Page 139: ...OPERATOR S MANUAL 136 DIAGNOSTICS Flex4 ProTM Control System 6010541 Rev A...
Page 145: ...OPERATOR S MANUAL 142 TROUBLESHOOTING Flex4 ProTM Control System 6010541 Rev A...
Page 150: ...6010541 Rev A...
Page 151: ...OPERATOR S MANUAL APPENDIX C Flex4 ProTM Control System 6010541 Rev A APPENDIX C 147...