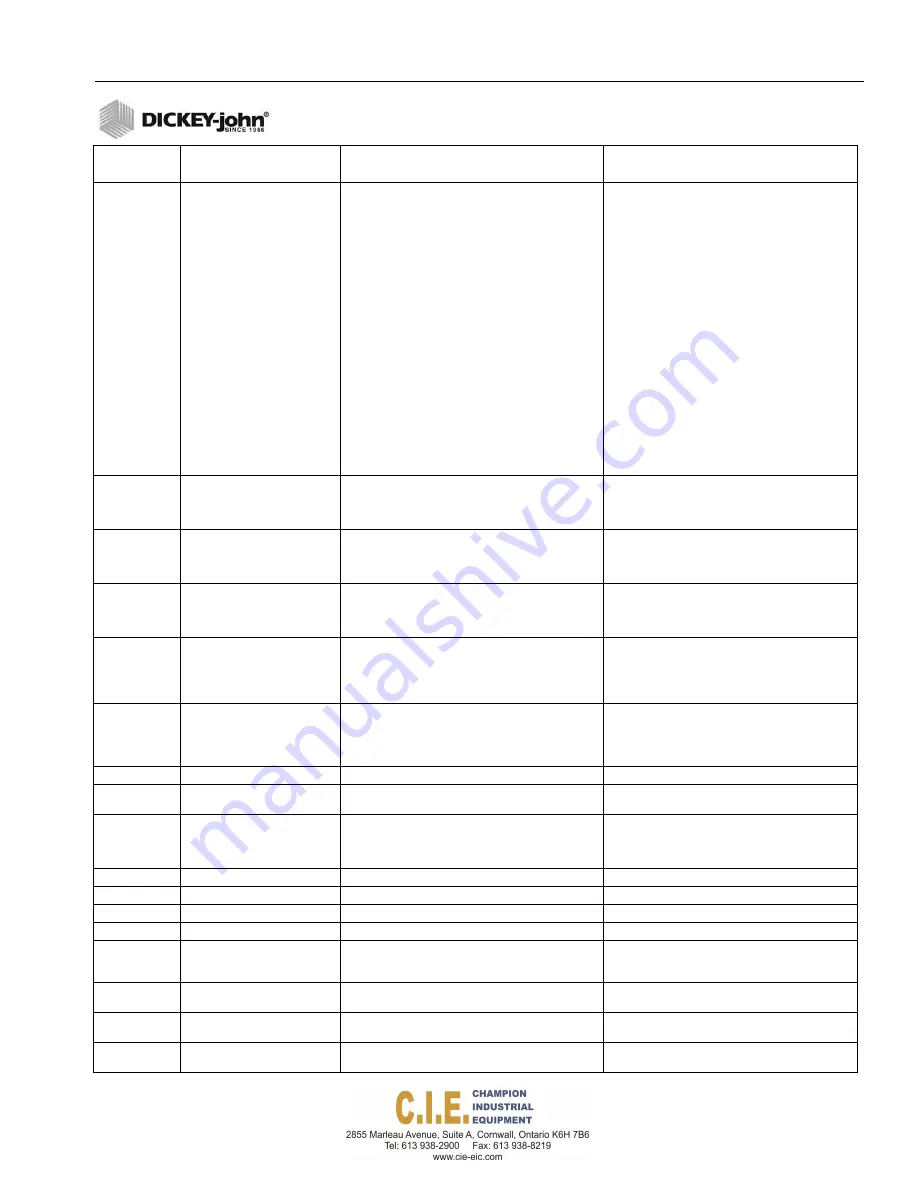
OPERATOR’S MANUAL
ERROR
CODE
ERROR
PROBABLE CAUSE
CORRECTIVE ACTION
208
“Channel” Application Rate
Error (liquid)
A fully open valve is indicated but the target APR
cannot be achieved.
1. Check to see if the liquid tanks are low, shutoff
valves are partially closed, bypass valves are
open too far, or an obstruction is in the liquid tank
outlet.
2. Check filters between the liquid tank and
suction side of the liquid pump for blockage.
3. Check for plugged nozzles or nozzles that are
too small to supply sufficient gallons per minute.
4. If using a electric liquid pump, check that the
nozzle pressure (spray bar pressure) does not
exceed 40 psi. Some electric pumps have an
internal pressure switch to shut pump off high
back pressure conditions.
5. Ensure a correct K-FACTOR is programmed.
Compare it against the number stamped on the
flowmeter body or recorded on the Calibration
Data Record Sheet. If original settings are not
available, run a liquid calibration.
6. Observe the PWM SAT under the Liquid
Configuration screen. Compare against original
setting. If not available, run a system response on
the liquid channel.
250
Prewet Channel Disabled
Prewet is not linked to a granular channel.
The system cannot run as configured.
1. Setup a granular channel to use as a reference
for the prewet application.
2. Or change the prewet channel type.
300
Invalid Gate Height Sensor
Configuration
The calibration points of the gate height are
incorrect. Most likely, the values do not follow an
increasing or decreasing only pattern.
1. Check calibration numbers and re-run
calibration.
2. or accept default values and continue
calibration.
301
Invalid Gate Height Open
Calibration
The open calibration point is near zero. A zero full
open position is not valid.
1. Check calibration numbers and re-run
calibration.
2. or accept default values and continue
calibration.
302 Invalid
Temperature
Calibration
Temperature calibration did not complete.
1. Verify temperature sensor adapter is
connected and the temperature sensor is
disconnected. With adapter connected and
sensor unplugged, the signal should toggle
between 0.7V and 2.7V.
400
GPS Signal Low
Poor GPS signal
1. Verify GPS is enabled at the F10 screen.
2. GPS signal may be blocked. Move to a clear
area.
3. Check that receiver connection is secure.
401
Data Memory Near Full
Memory for storing operation data is running low.
1. Export data to a USB memory device.
402
Data Log Memory Full
Memory for operation is full and no additional data
can be saved.
1. Export data to a USB memory device.
403
Invalid Task Data
A task controller device error may occur on systems
with previous software versions when loading new
software.
1. Acknowledge alarm and follow onscreen
instructions
2. Insert a USB memory device.
3. Export files.
500
Gate High
Gate is above the open or highest calibrated point.
1. Check sensor and calibrations.
501
Gate Low
Gate is below the closed or lowest calibrated point.
1. Check sensor and calibrations.
502
Bed Height Too High
Bed is above the alarm value.
1. Lower bed or check sensor.
503
Down Pressure Too High
Down pressure has exceeded the alarm threshold.
1. Reduce down pressure or check sensor.
504
TankPressureLow
Tank level has dropped below alarm level.
1. Fill Tank.
2. Adjust alarm level setting.
3. Check sensor.
505
Air Temp Below Alarm Value
1
Temperature has dropped below alarm threshold.
1. Adjust alarm setting.
2. Check sensor.
506
Air Temp Below Alarm Value
2
Temperature has dropped below alarm threshold.
1. Adjust alarm setting.
2. Check sensor.
507
Air Temp Below Alarm Value
3
Temperature has dropped below alarm threshold.
1. Adjust alarm setting.
2. Check sensor.
Flex4 Pro
TM
Control System
6010541 Rev A
TROUBLESHOOTING / 139
Summary of Contents for Flex4
Page 1: ...FLEX4 PRO PUBLIC WORKS CONTROL SYSTEM Operator s Manual SINCE 1966 FLEX PRO...
Page 5: ...OPERATOR S MANUAL Flex4 ProTM Control System 6010541 Rev A SAFETY NOTICES 2...
Page 7: ...OPERATOR S MANUAL 4 INTRODUCTION Flex4 ProTM Control System 6010541 Rev A...
Page 29: ...OPERATOR S MANUAL 26 INSTALLATION Flex4 ProTM Control System 6010541 Rev A...
Page 49: ...OPERATOR S MANUAL 46 OPERATION Flex4 ProTM Control System 6010541 Rev A...
Page 55: ...OPERATOR S MANUAL 52 FLEX4 PROTM PROGRAMMING Flex4 ProTM Control System 6010541 Rev A...
Page 105: ...OPERATOR S MANUAL 102 SYSTEM PROGRAMMING Flex4 ProTM Control System 6010541 Rev A...
Page 123: ...OPERATOR S MANUAL 120 CALIBRATIONS Flex4 ProTM Control System 6010541 Rev A...
Page 131: ...OPERATOR S MANUAL 128 CAPTURE SCREEN SHOT Flex4 ProTM Control System 6010541 Rev A...
Page 139: ...OPERATOR S MANUAL 136 DIAGNOSTICS Flex4 ProTM Control System 6010541 Rev A...
Page 145: ...OPERATOR S MANUAL 142 TROUBLESHOOTING Flex4 ProTM Control System 6010541 Rev A...
Page 150: ...6010541 Rev A...
Page 151: ...OPERATOR S MANUAL APPENDIX C Flex4 ProTM Control System 6010541 Rev A APPENDIX C 147...