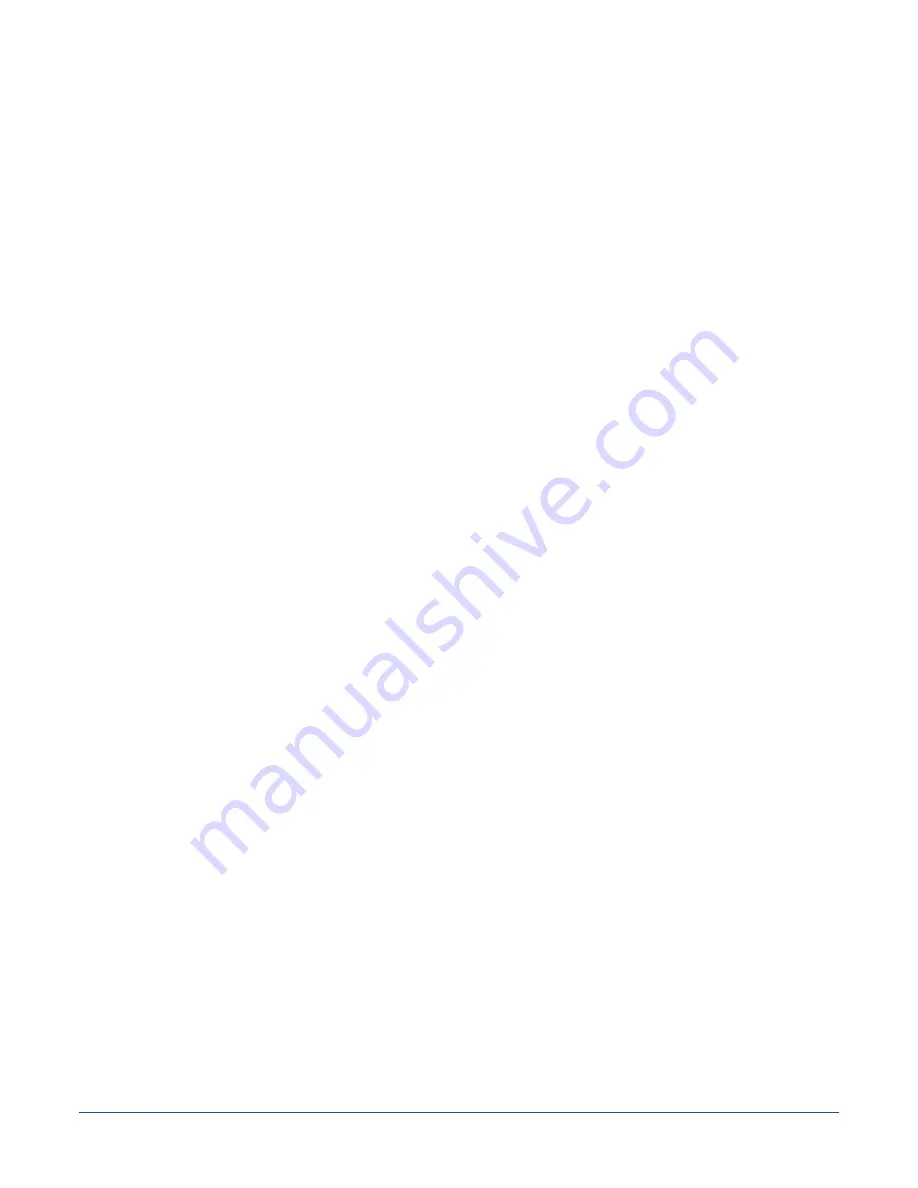
/16
WWW.DIAQUIP.CO.UK
ABOUT DIAMOND BITS
Without adequate water, the bit would overheat and be destroyed. With too much water
and not enough feed pressure, there would not be adequate erosion of the bond matrix (the
diamonds not exposed) and the bit becomes dull (diamond segments polish smooth). This is
called glazing and luckily the bit can be de-glazed (sharpened). If the bit seems to refuse to cut
anymore, you know that it is glazed.
See page xx: “SHARPENING A GLAZED BIT”
Never use a sharp motion or the bit will be damaged. Conversely, don’t feed too gently or the
diamond segments will become glazed. Keep the bit steadily working, but don’t be abusive or
give the bit shock impacts into the work surface.
If the cut is very deep, the core plug may be obstructing the flow of cooling water. In this case,
stop drilling, and chisel out the core plug before continuing.
CAUTION: If the bit gets stuck, do not try to rock it loose by turning the switch on and
off. That is hazardous and could damage the motor. Rather, unplug the machine and use
a wrench on the bit mounting to work it loose.
If embedded steel such as rebar is encountered take special care. When the steel is
encountered, the water will generally go clear and vibration will begin. Change to a lower gear
if available. Reduce the feed pressure by about 1/3 and let the bit go at its own pace, if there
is too much vibration the bit will be destroyed. Once the steel is passed, continue normally. A
properly sharp bit with good diamond exposure should be able the cut through rebar if handled
well. When the cut is finished keep the motor running until the bit is removed from the cut to
avoid it getting stuck.
CAUTION: Drilling operations are very stressful to the motor and at the end of the cut,
the motor temperature will be very hot, always run the motor at no load for a few minutes
until the temperature returns to a normal range before shutting off. Turn the water feed
down to a very small amount of flow (not off), just enough to keep the water seals from
overheating when you perform this step.
Then turn off the switch and allow the coasting bit
to stop before setting it down.