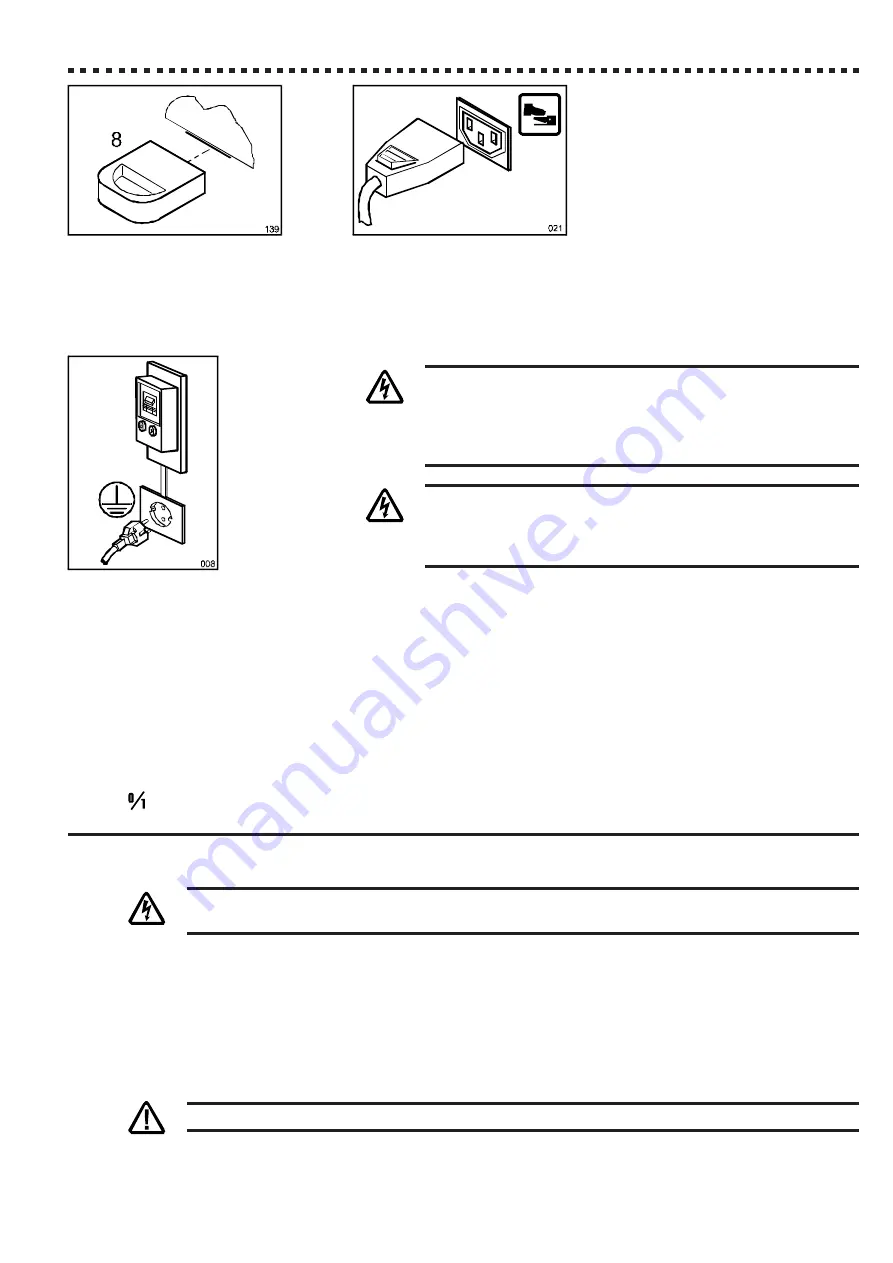
English
Operating instructions
7
Z15.027
V01
—
install drip tray [8] in the appropriate slot in the front panel;
—
In models equipped with pedal dispensing control, connect the pedal’s plug in the relevant socket, marked by the
appropriate symbol. It is possible to use the dispensing push-button also when the pedal is connected.
4.3
Electrical connection
T
HE
ELECTRICAL
SAFETY
OF
THIS
MACHINE
IS
REACHED
ONLY
WHEN
THE
SAME
IS
CORRECTLY
CONNECTED
,
BY
QUALIFIED
AND
CERTIFIED
PERSONNEL
,
TO
AN
ELECTRICAL
PLANT
PRO
-
VIDED
WITH
AN
EFFICIENT
EARTHING SYSTEM,
MADE
AS
REQUIRED
BY
IN
FORCE
SAFETY
REGULATIONS
.
M
AKE
SURE
THAT
THE
VOLTAGE
PRESENT
IN
THE
ELECTRICAL
NETWORK
IS
SUITABLE
WITH
THE
VOLTAGE
REQUESTED
BY
THE
MACHINE
(
GIVEN
ON
THE
TECHNICAL
DATA
PLATE
OR
IN
THE
TECHNICAL
HANDBOOK
).
The manufacturer shall not be responsible for any damages caused by a faulty electrical supply or earthing
plant.
Check that the electrical capacity of the plant is adequate to the maximum requirements of the machine as indicated in
the technical data plate. Make sure that the cable section of the plant is sufficient for the power required by the machine.
It is required, for a safe and correct installation of the machine, to arrange a suitable socket controlled by a power breaker
provided for in current safety regulations, with an associated differential safety breaker, positioned so to be easily reached
by the operator.
The socket must also be protected by fuses with sizes and capacity adequate to the power required by the machine,
indicated on the technical data plate or on the Technical Handbook.
Verify that the plant complies with the above said characteristics and insert the plug in the socket. Only the green
POWER
indicator must turn on.
5
M
ACHINE
’
S
OPERATION
O
PERATING
THE
MACHINE
,
AS
ANY
OTHER
ELECTRICAL
DEVICE
,
ENTAILS
OBSERVING
SOME
VERY
IMPORTANT
SAFETY
RULES
,
IN
PARTICULAR
:
—
Do not touch it with wet or damp feet or hands.
—
Do not operate when barefoot.
—
Do not pull electrical feeding cable to unplug.
—
Do not expose machine to rain and prevent any water from entering, i.e. during washing.
—
In case of failure and/or malfunction and any time there is apparent damage to the power supply cable, cut
power off and call Assistance Service.
ALWAYS
FOLLOW
SAFETY
MEASURES
(
REF
. C
HAPTER
1).