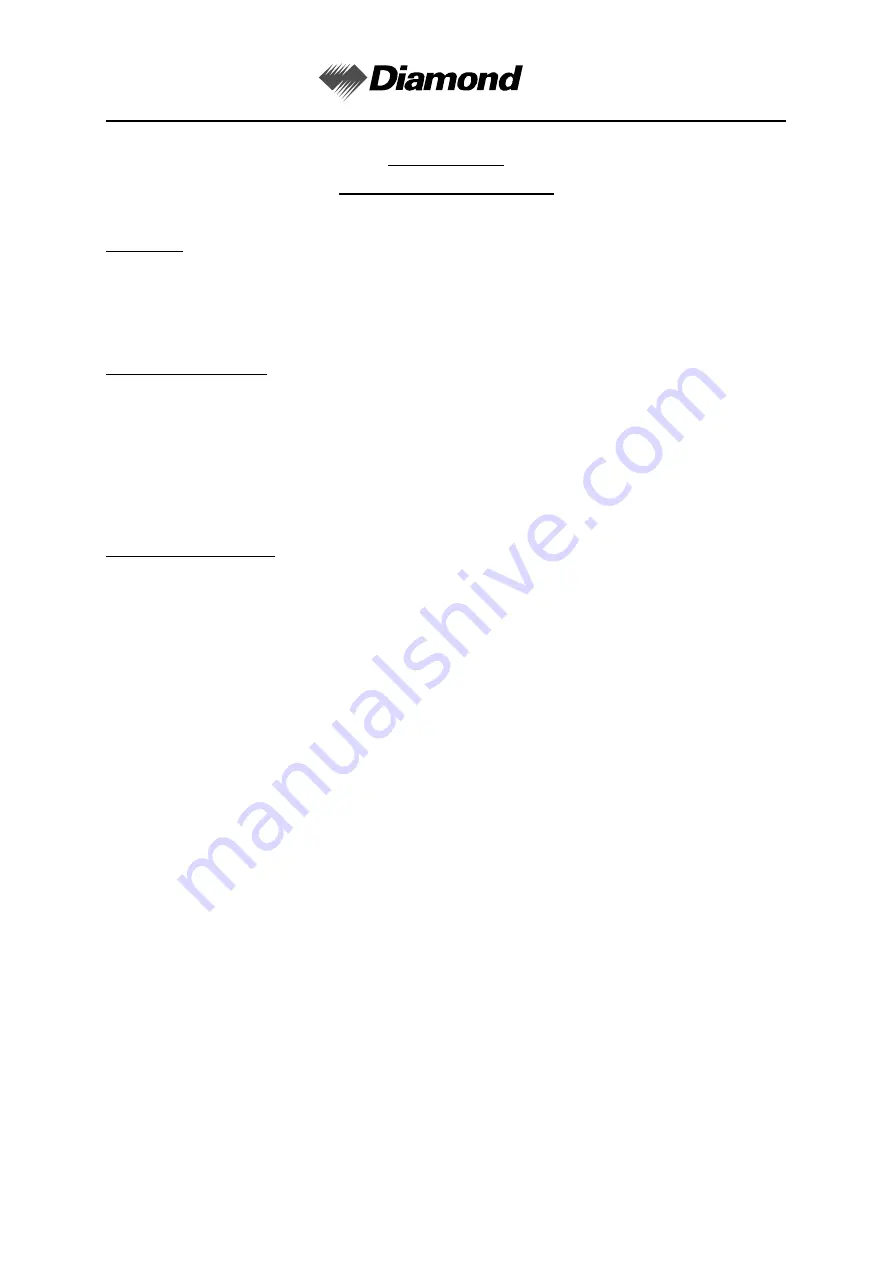
AIRCRAFT
DV 20 KATANA AMM
Time Limits /
Maintenance Checks
Doc # 4.02.02
Rev. 13
05-30-00
Page 1
15 Dec 2018
Section 05-30
GENERAL INSPECTIONS
1. General
Preflight as well as postflight inspections are part of the general inspection procedure. In general these
inspections are performed on a daily base. These inspections are described in the Airplane Flight
Manual and are performed by the pilot.
2. Preflight Inspection
This inspection should be performed before the first flight of the day to determine the general condition
of the airplane and its engine.
Specific attention should be given to the preflight inspection, because many accidents were caused
by insufficient preflight inspection. It must be ensured that all switches are in the OFF position (also
refer to the Airplane Flight Manual) before any inspection is attempted.
%
3. Postflight Inspection
This inspection should be performed after the last flight of the day.
Measures supplementary to those described in the Airplane Flight Manual:
%
Check on-board log book for any open complaints, as well as for correct recording of all landings and
flight hours.
If required, moor the airplane (refer to Chapter 10).
Summary of Contents for DV 20 KATANA
Page 155: ...AIRCRAFT DV 20 KATANA AMM Dimensions and Areas Doc 4 02 02 Rev 13 06 00 00 Page 5 15 Dec 2018...
Page 173: ...AIRCRAFT DV 20 KATANA AMM Leveling and Weighing Doc 4 02 02 Rev 13 08 00 00 Page 3 15 Dec 2018...
Page 389: ...AIRCRAFT DV 20 KATANA AMM Fuel Doc 4 02 02 Rev 13 28 TITLE Page 1 15 Dec 2018 CHAPTER 28 FUEL...
Page 515: ...AIRCRAFT DV 20 KATANA AMM Structures Doc 4 02 02 Rev 13 51 10 00 Page 7 15 Dec 2018...
Page 516: ...AIRCRAFT Structures DV 20 KATANA AMM Page 8 15 Dec 2018 51 10 00 Doc 4 02 02 Rev 13...
Page 517: ...AIRCRAFT DV 20 KATANA AMM Structures Doc 4 02 02 Rev 13 51 10 00 Page 9 15 Dec 2018...
Page 518: ...AIRCRAFT Structures DV 20 KATANA AMM Page 10 15 Dec 2018 51 10 00 Doc 4 02 02 Rev 13...
Page 519: ...AIRCRAFT DV 20 KATANA AMM Structures Doc 4 02 02 Rev 13 51 10 00 Page 11 15 Dec 2018...
Page 520: ...AIRCRAFT Structures DV 20 KATANA AMM Page 12 15 Dec 2018 51 10 00 Doc 4 02 02 Rev 13...
Page 521: ...AIRCRAFT DV 20 KATANA AMM Structures Doc 4 02 02 Rev 13 51 10 00 Page 13 15 Dec 2018...
Page 522: ...AIRCRAFT Structures DV 20 KATANA AMM Page 14 15 Dec 2018 51 10 00 Doc 4 02 02 Rev 13...
Page 693: ......
Page 694: ......
Page 695: ......
Page 696: ......
Page 697: ......
Page 698: ......
Page 699: ......
Page 700: ......
Page 701: ......
Page 702: ......
Page 703: ......
Page 704: ......
Page 705: ......
Page 706: ......
Page 707: ......
Page 708: ......
Page 709: ......
Page 710: ......
Page 711: ......
Page 712: ......
Page 713: ......
Page 714: ......
Page 715: ......
Page 716: ......
Page 717: ......
Page 718: ......
Page 719: ......
Page 720: ......
Page 721: ......
Page 722: ...MAINTENANCE MANUAL DV 20 KATANA...
Page 723: ...MAINTENANCE MANUAL DV 20 KATANA...