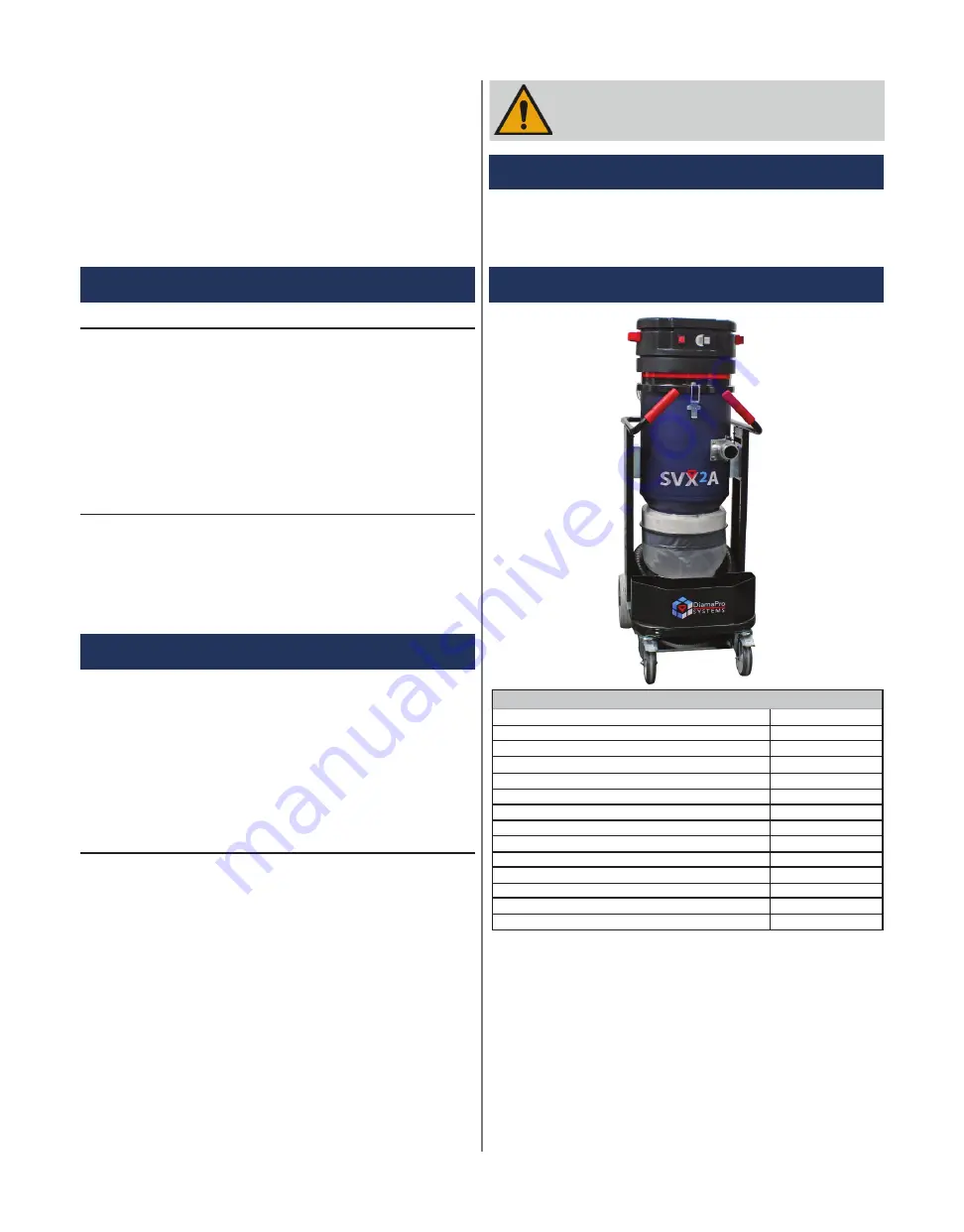
• Make sure that the power cable has no wear or damage. If replacing the
cable, always replace it with another of the same specifications as the orig
-
inal one: cables that are not approved or of inferior quality may overheat
and cause serious injury to the user
• Make sure that the machine is connected to an appropriate power source
in full working order (check the presence of a fully functional grounding
socket)
• Repairs must only be carried out by authorized personnel and only when
the machine is turned off and disconnected from the power source
• Never allow unauthorized personnel to use the machine
• Make sure that all safety devices are in full working order before turning
on the machine
• Never cover the vacuum cleaner during use
7. INSTALLATION
7.1 DELIVERY AND HANDLING
All machines are carefully tested and checked by DiamaPro before
delivery. The machine is transported inside a protective box or wrapped
in a protective film that allows the courier to see the item during transport
and is securely fixed to a pallet. If any part of the machine is not intact or
has been damaged during transport, file an immediate complaint with the
courier. Parts that have been damaged or broken due to incorrect transport
or handling of the machine will not be recognized by the manufacturer’s
warranty. The machine must be lifted and moved using a forklift truck in
accordance with the relevant safety regulations in force in the workplace
7.2 CHECK THE PROPER ELECTRICAL
CONNECTION
Connect the industrial plug to the power cable and connect the plug to a
socket that has the same amp rating and is protected by a line-isolating
switch; in the case of the three-phase vacuum cleaner, it is necessary to
check before use that the motor rotates in the correct direction (clockwise)
as shown by the die-cast indicator on the turbine; if rotation occurs in an
anti-clockwise direction, it is necessary to disconnect the machine from
the power source, invert one of the three phase cables inside the plug and
check again for correct rotation
8. PERIODICAL MAINTENANCE
Maintenance and cleaning operations must ALWAYS be carried out when
the vacuum is turned off and disconnected from the power source. No
particular measures must be taken for the maintenance, cleaning or lubri-
cation of the suction unit. However, it is important to remember that correct
use and servicing are essential if the safety and efficiency of the vacuum
are to be guaranteed.
To ensure regular and constant operation and to prevent the warranty from
becoming void, always use genuine DiamaPro spare parts when repairs
are needed.
8.1 BEFORE TURNING ON AND TURNING OFF
EVERY DAY
• Visually check that the suction hose has not been damaged in any way (it
must not be damaged, torn, crushed)
• Check that the electrical switches are in full working order and are not
damaged in any way
• Check the level of waste inside the main barrel N.B. Empty the main
barrel if you are using an DiamaPro model empty the main barrel
• Check that the suction hose has not been damaged in any way
• Check that the motor head is correctly positioned on the filter chamber
and that the latter is correctly placed on the main barrel
• If the vacuum cleaner is moved, ensure that the power voltage of the play
in this new location corresponds to the one on the technical data plate
8.2 AT EVERY 200 HOURS OF OPERATION
• Check the condition of the primary filter: it must not have tears, holes or
other damage: in this case replace it (see 14.)
• Check that the technical data plate is legible and not damaged in any
way: contact the manufacturer for a replacement if necessary
PERFORM THE FOLLOWING OPERATIONS AT
EVERY 10 HOURS OF OPERATION IF THE VACUUM
CLEANER IS AN DIAMAPRO MODEL
9. PRODUCT DISPOSAL
Dispose of the machine and any accessories according to the legislation of
the country. To avoid affecting the environment or your health or the health
of others it is recommended to separate the machine from other waste,
and if necessary properly recycle it.
10. TECHNICAL DATA
MODEL
CODE
CERTIFICATE
MOTORS
VOLTAGE
FILTER CLEANING
FILTRATION CLASS
USEFUL CAPACITY
CFM*
WATERLIFT
DIMENSIONS
INLET DIMENSION
TANK DIAMETER
WEIGHT
SOUND PRESSURE LEVEL (ISO 11201)
SVX2A
110V-60HZ
CE
2
110V-60 HZ
AUTOMATIC
HEPA
INFINITY BAGS
220
88 IN
31X25X54IN
2 IN
18 IN
218 LBS
<78
*Theoretical