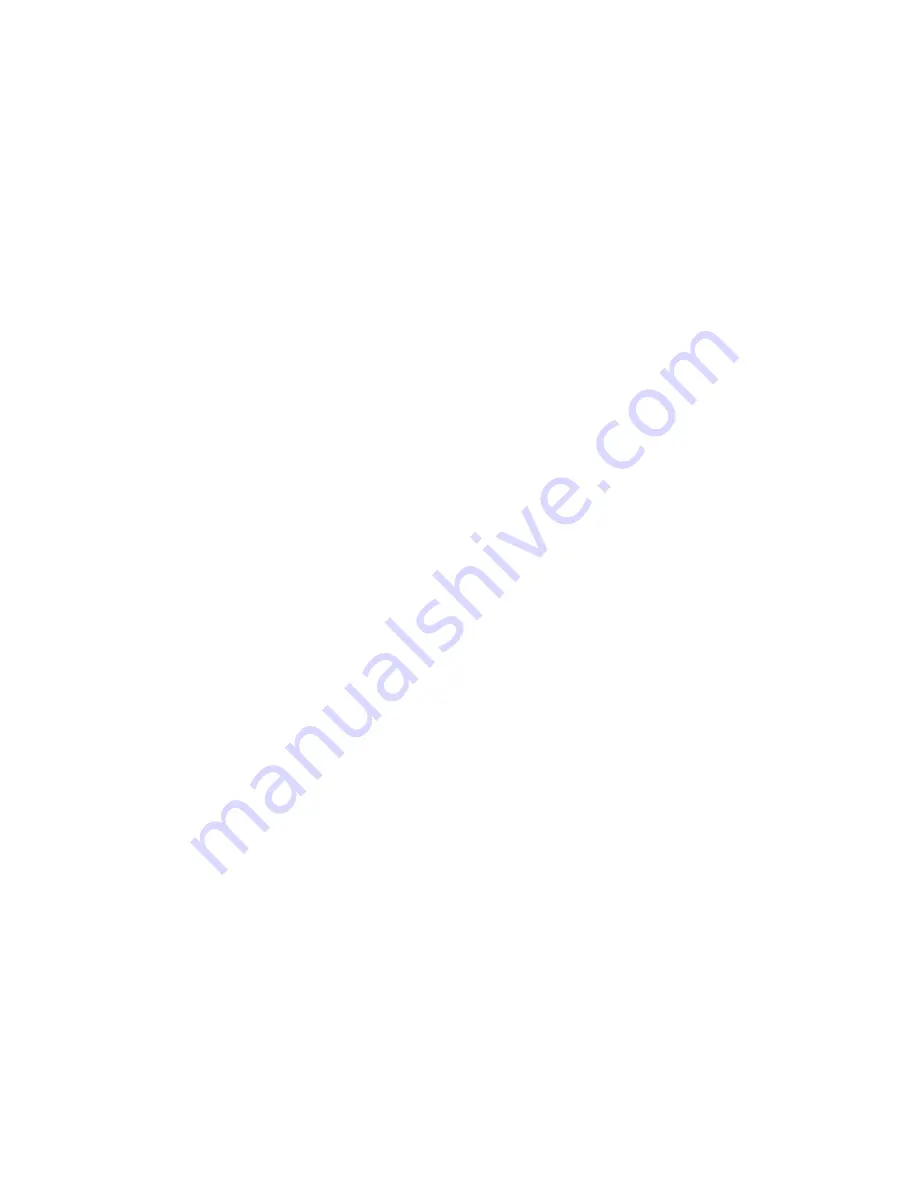
DSP222H_Manual_A
Page 5 of 17
The front-panel LED indication LED2 (LED1) is used to indicate the “Call” output of the
channels. LED3 (LED4) indicates the “Fail” condition of the loops. These outputs are
driven directly by the microcontroller. Monolithic voltage regulators provide a stable 12-
volt reference supply U3. Two additional 5-volt regulators provide stable 5-volt power to
the digital circuitry U2 and loop oscillators respectively U4.
An external reset signal is provided to reset the microcontroller with a low (ground true)
signal on pin C of the loop sensor unit. This is accomplished by using Q9 as an input
voltage comparator and phase inverter as well as a second phase inverter Q10. The
input signal is “noise” filtered with C15 and diode D5.
Front-panel switch S1 (S2) is used to input data to the microcontroller from the user.
The sensitivity setting and the choice of pulse or presence operation are routed directly
to the input ports of the microcontroller U1.
Transistor Q7 (Q8) is the high-current driver necessary to power the opto-isolator U5
outputs for external equipment.
The +24 volt input is protected with a power diode D6 to prevent damage to the unit if
power is connected incorrectly. In addition, an input resistor R36 is provided to reduce
inrush current when the unit is plugged into a “hot” card cage. The input voltage is well
filtered with C16.
6. Preventive Maintenance
Over the years, the electronic components used in inductive loop detectors have
become very reliable. Generally, most inductive loop sensor problems can be traced to
the loop system. The loop system is defined as the loop of wire(s) located in the street,
the lead-in wire(s) located between the street loop and the controller cabinet, and the
associated wiring in the controller cabinet itself.
The wire used in the street loop should be rated for direct burial. The wire should be of
the cross-linked polyethylene (XLPE) insulated type. PVC insulated type of wire should
always be avoided. The sealant should be carefully chosen to match the application and
pavement. A hard setting epoxy should never be used with asphalt.
The loop wires should be held into the bottom of the saw cut with backer rod. The loop
wire should be twisted with a minimum of 5 twists per foot between the loop itself and
the splice point. This is usually the hand hole or pull box at the side of the road.
At this point, the twisted loop wires must be soldered to the lead-in cable. If crimp type
connectors are used, they must be soldered after crimping. After soldering, the splices
must be protected with a moisture-proof seal.