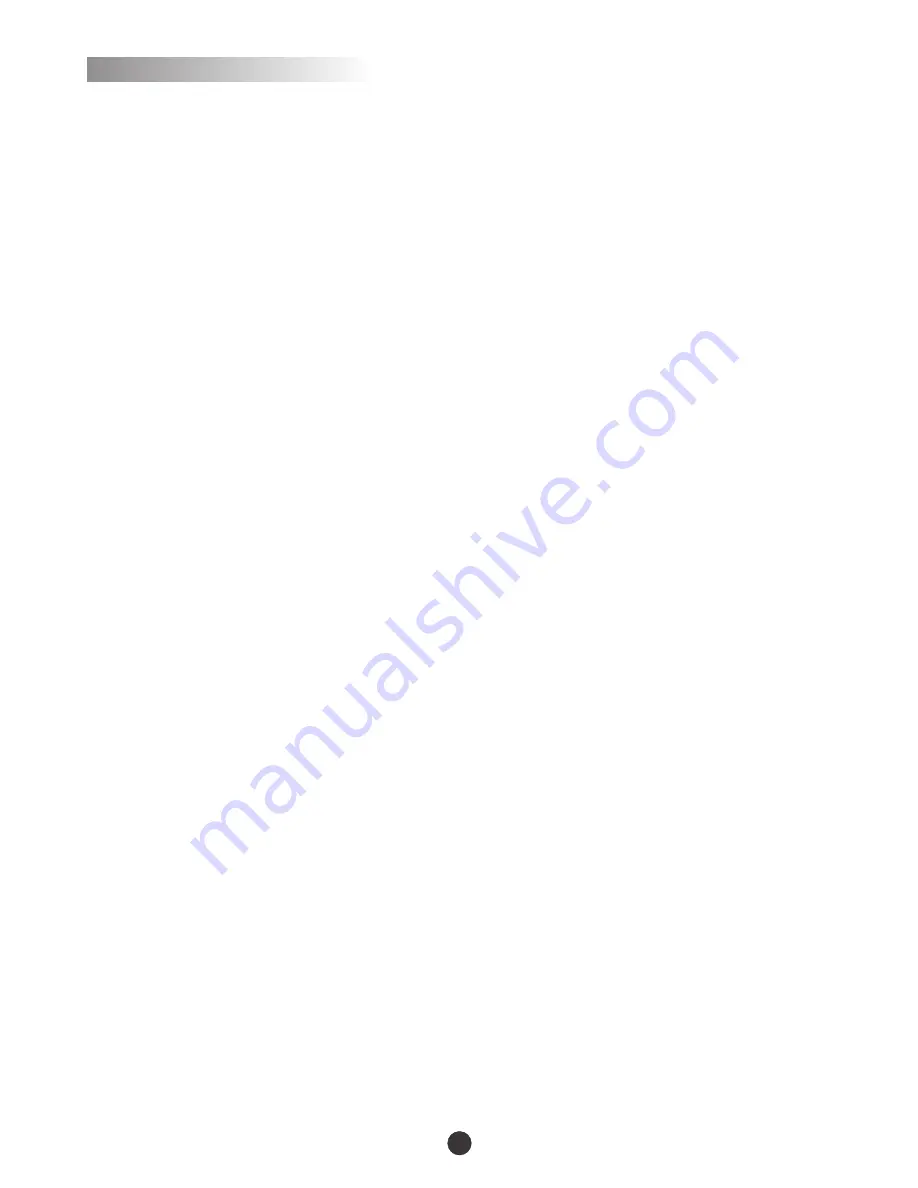
Terminology
Electronic speed controller (ESC)
An electronic circuit with the purpose to vary an electric motor's speed, its direction and possibly also to
act as a dynamic brake. ESCs are often used on electrically-powered radio controlled models.
An ESC can be a stand-alone unit which plugs into the receiver's throttle control channel or incorporated
into the receiver itself, as is the case in most toy-grade R/C vehicles. Some R/C manufacturers that
install
proprietary hobby-grade electronics in their entry-level vehicles, vessels or aircraft use onboard electronics
that combine the two on a single circuit board.
Brush DC motors
A typical RC brushed motor looks like a small metal can with an axle sticking out of one end and battery
leads on the other end. The commutator shaft, armature, wires, brushes, and magnets are contained
inside that can. Those carbon brushes inside the can connect with the commutator shaft. When voltage
is applied through the battery leads to the brushes in contact with the commutator shaft it causes the motor
to spin and gives forward and reverse motion to the RC.
Brushed motors are rated by the number of turns of copper wire around the armature within the motor.
Stock unmodified brushed motors are usually 20 turn motors but can go all the way down to 7 turn modified
brush motors. A higher number of turns provides for more torque but also lower RPMs and less speed.
But it also provides longer battery life. The lower the number of turns of the brushed motor, the more voltage
can be applied with less torque and higher RPMs-resulting in more speed.
RC servos
Servos are hobbyist remote control devices typically employed in radio-controlled models, where they
are used to provide actuation for various mechanical systems such as the steering of a car, the control
surfaces on a plane, or the rudder of a boat.
Due to their affordability, reliability, and simplicity of control by microprocessors, RC servos are often
used in small-scale robotics applications.
RC servos are composed of an electric motor mechanically linked to a potentiometer. A standard RC
receiver sends Pulse-width modulation (PWM) signals to the servo. The electronics inside the servo
translate the width of the pulse into a position. When the servo is commanded to rotate, the motor is
powered until the potentiometer reaches the value corresponding to the commanded position.
RC servos use a three-pin 0.1" spacing jack (female) which mates to standard 0.025" square pins (which
should be gold-plated, incidentally). The most common order is Signal, +voltage, ground. The standard
voltage is 6VDC, however 4.8V and 12V has also been seen for a few servos. The control signal is a digital
PWM signal with a 50Hz frame rate. Within each 20ms timeframe, an active-high digital pulse controls
the position. The pulse nominally ranges from 1.0ms to 2.0ms with 1.5ms always being center of range.
Pulse widths outside this range can be used for "overtravel" -moving the servo beyond its normal range.
This PWM signal is sometimes (incorrectly) called Pulse Position Modulation (PPM).
The servo is controlled by three wires: ground, power, and control. The servo will move based on the
pulses sent over the control wire, which set the angle of the actuator arm. The servo expects a pulse
every 20 ms in order to gain correct information about the angle. The width of the servo pulse dictates
the range of the servo's angular motion.
A servo pulse of 1.5 ms width will typically set the servo to its "neutral" position or 45°, a pulse of 1.25 ms
could set it to 0° and a pulse of 1.75 ms to 90°. The physical limits and timings of the servo hardware varies
between brands and models, but a general servo's angular motion will travel somewhere in the range of
90° - 120° and the neutral position is almost always at 1.5 ms. This is the "standard pulse servo mode"
used by all hobby analog servos.
A hobby digital servo is controlled by the same "standard pulse servo mode" pulses as an analog servo.
Some hobby digital servos can be set to another mode that allows a robot controller to read back the
position of the servo shaft. Some hobby digital servos can optionally be set to another mode
actual
and
"programmed", so it has the desired PID controller characteristics when it is later driven by a standard
RC receiver.
5
Summary of Contents for HUNTER 8135
Page 1: ...1 10 Scale 4WD Brushed Short Course Truck Model 8135...
Page 11: ...8135 008 8135 007 8135 001 10...
Page 20: ...Optional Parts 19 8381 404 Set screws M3 3mm 8 pcs 8381 716 Set screws M4 10mm 16 pcs...
Page 21: ...20...
Page 23: ...Parts Diagrams 22...
Page 25: ...24...
Page 26: ...25...
Page 28: ......