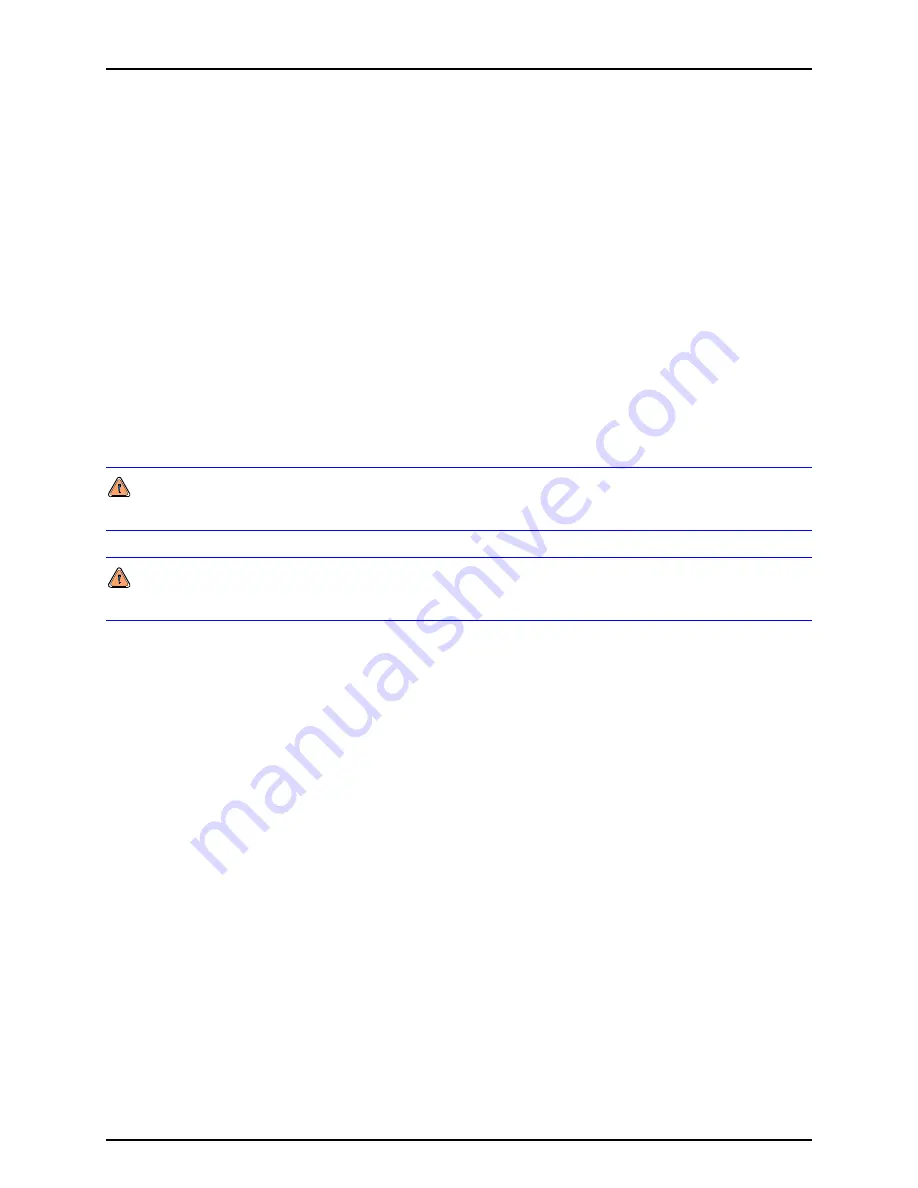
GB-75™ AND GB-152™ OPERATION AND MAINTENANCE MANUAL
©1998-2008 DH Instruments, a Fluke Company
Page 20
5.7
LEAKS
Pressure leaks are the most common problem found in pressure handling equipment. Normally, the first
step is to determine if the leak is within the booster or outside of the unit.
•
To determine if the leak is within the unit, disconnect at the booster high pressure
OUT port
and
plug it. Establish similar conditions under which the leak was observed and determine if the leak is
still present. For small leaks, it may be necessary to install an appropriate pressure sensing device
at the
OUT port
. In some cases, it is useful to perform simple leak checks on the most common
outside sources before disconnecting the test system. Note that leaks inside the booster are unusual
unless there has been some disassembly.
•
More than one leak can exist in a system. Fixing one leak does not guarantee a leak tight system.
Therefore, continue executing the troubleshooting procedures until all leaks are located
and corrected. Since it is impractical to produce a troubleshooting guide that will cover every
conceivable leak, the source of your leak may not be covered in this guide.
•
Check all fittings and components for leaks. Use leak detection fluid for small leaks. Tighten loose
fittings or replace damaged fittings. Repair or replace leaking regulators.
Never tighten a fitting while it is under pressure. If pressure is in the system and the fitting should fail
while being tightened, you or those around you may be injured.
Do not over-torque the DH500 fittings that are inside the booster. To do so will damage them, requiring
their replacement. Recommended torque on a DH500 fitting gland is 15 Nm.
It is possible that a leak exists in the high pressure section of the gas booster. These leaks are very
difficult to isolate and detect. If no leaks can be found following the above procedures, it is likely the
problem is within the booster. Contact a
DHI
Authorized Service Provider for assistance (see Section 6).
5.8
GAS CONTINUOUSLY VENTS THROUGH
EXHAUST MUFFLER
When the booster does not run and gas is venting through the muffler, the boosters air cycling valve
(spool valve) is stuck between its toggle points. This is normally caused by a low gas flow rate.
There are two methods for restoring proper operation. It is recommended to perform them in the
order below:
•
Put the drive air
SHUTOFF valve
in the OFF position. Plug the booster high pressure
OUT port
.
Increase drive air pressure, using the
DRIVE ADJUST regulator,
to about 500 kPa (75 psi). Put the
drive air
SHUTOFF valve
into the ON position quickly. If the booster begins to operate normally, set
the drive air
SHUTOFF valve
to OFF and reset the regulator to previous settings. Repeat the
process until the booster begins normal operation.
•
Put the drive air
SHUTOFF valve
in the OFF position. Plug the booster high pressure
OUT port
.
Increase drive air pressure using the
DRIVE ADJUST regulator
to about 500 kPa (75 psi). Remove
the exhaust muffler and use your hand to plug the vent port. Put the drive air
SHUTOFF valve
into
the ON position quickly. When the build-up of pressure begins to leak past your hand, quickly
remove it. If the booster begins to operate normally, set the drive air
SHUTOFF valve
to OFF,
reinstall the muffler and reset regulators to previous settings. Repeat the process until the booster
begins normal operation.
If normal operation cannot be restored, contact a
DHI
Authorized Service Provider.