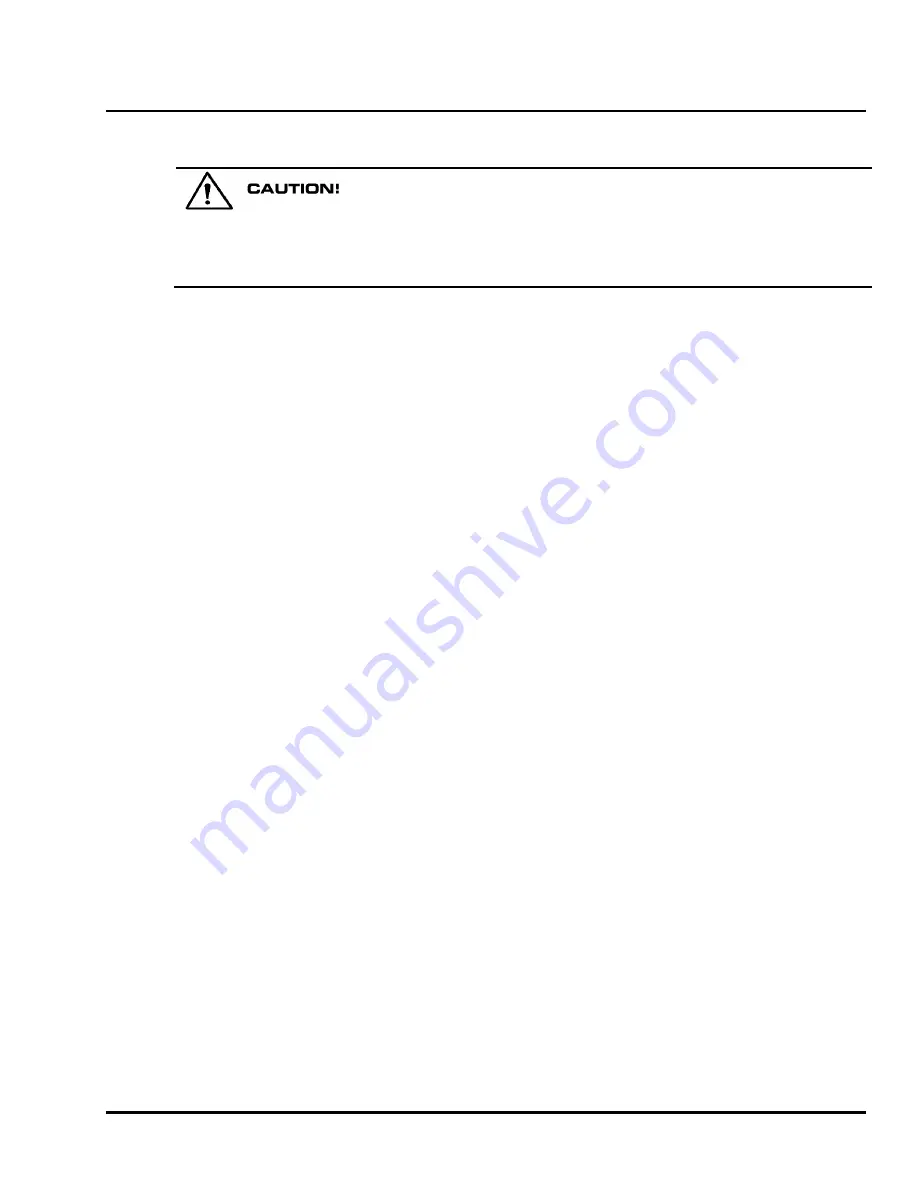
DeZURIK
APCO CSD-800 Slanting Disc Check Valves
July 2017
Page 5
D12012
Fusion/Powder Coated Valves
Valves with fusion/powder coated exterior paint require flat washers to be installed
under the flange nuts when installing the valve to the pipeline flange to prevent the
paint from cracking or chipping.
Maintenance
CSD-800 Valves
The APCO Slanting Disc Check Valve requires very little regular maintenance except for periodic
(approximately 6 months) greasing of pivot pins, and occasional observation of the disc position
indicator to ensure that the valve disc is opening.
The Pivot Pins (13) on each side of the valve should be lubricated at least once a year with white water
proof, FDA approved Lubriplate grease. The amount of grease to be injected depends on the size of
the valve. Two strokes of a hand grease gun is needed for sizes up to 24”, and 3 strokes for sizes 30”
and larger.
The Check Valve is fitted with 2 covered accessory openings, one in each body half. These covers
may be removed to observe inside the valve to determine whether any leakage or blockage is
occurring.
CSD-800-BMB Valves
The CSD-800-BMB Slanting Disc Check Valve is shipped from the factory fully lubricated and oil tanks
filled with hydraulic oil to their proper levels ready for installation. It requires a very minimal amount of
preventive maintenance.
Special care should be taken to the exposed area of the Buffer Rod when painting the valve. It should
be fully masked to prevent even a small amount of paint from getting on the Buffer Rod which could
damage the cylinder rod seal and cause the cylinder to leak.
CSD-800-TMD Valves
Through the course of operation the upper half of dashpot piping must be checked for the loss of
pressure. It is normal for the system to indicate an increased pressure when the valve opens due to the
transfer of oil from the cylinder to the hydro-pneumatic tank, which further compresses the pressurized
air in the tank. If system is losing pressure, check for oil leaks along the dashpot piping or on the
hydro-
pneumatic tank air valve and follow “Oil Filling Procedure”.