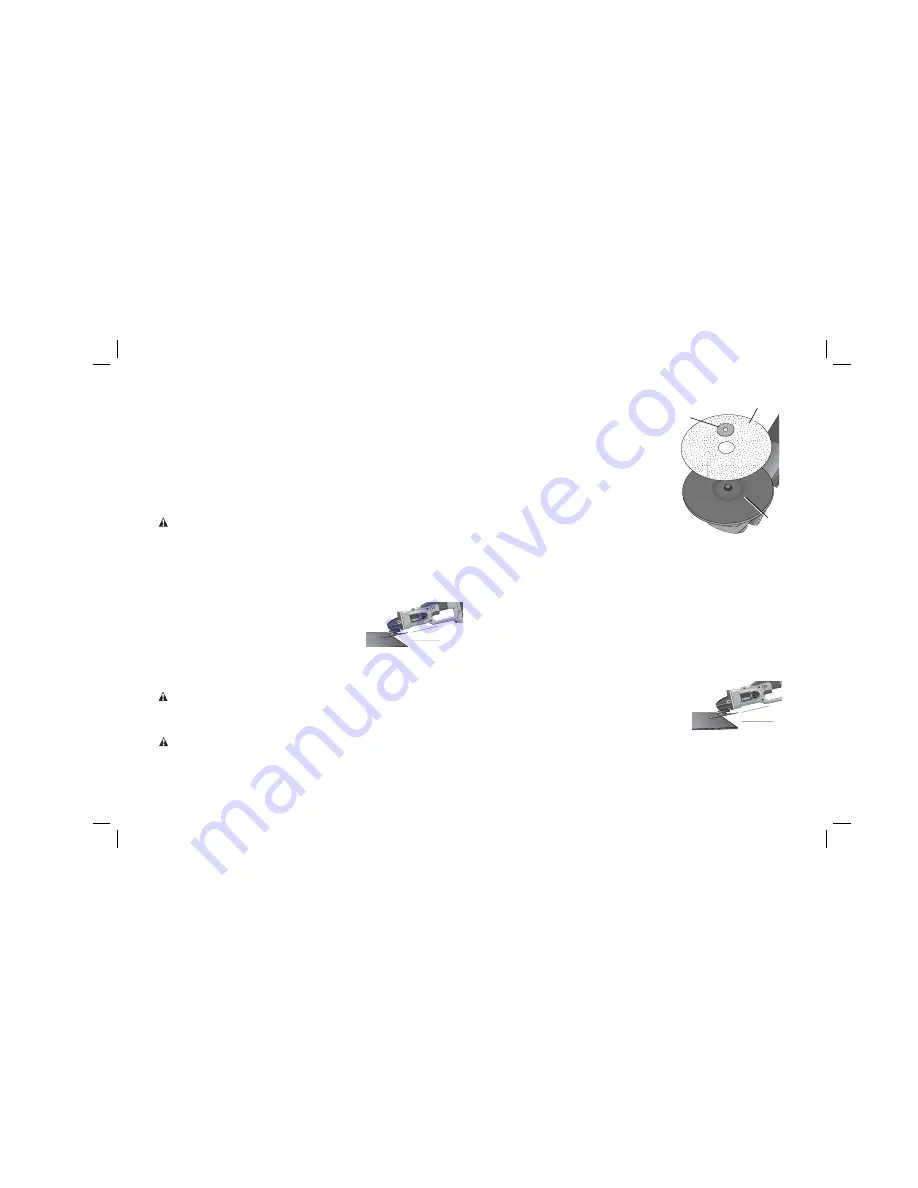
13
1. Allow the tool to reach full speed before touching the tool to the work surface.
2. Apply minimum pressure to the work surface, allowing the tool to operate at high
speed. Grinding rate is greatest when the tool operates at high speed.
3. Position yourself so that the open-underside of the wheel is facing away from you.
4. Once a cut is begun and a notch is established in the workpiece, do not change
the angle of the cut. Changing the angle will cause the wheel to bend and may
cause wheel breakage. Edge grinding wheels are not designed to withstand side
pressures caused by bending.
5. Remove the tool from the work surface before turning the tool off. Allow the tool
to stop rotating before laying it down.
WARNING:
Do not use edge grinding/cutting wheels for surface grinding
applications because these wheels are not designed for side pressures encountered
with surface grinding. Wheel breakage and serious personal injury may result.
SURFACE FINISHING WITH SANDING FLAP DISCS
1. Allow the tool to reach full speed before touching the tool to the work surface.
2. Apply minimum pressure to work surface, allowing the tool to operate at high
speed. Sanding rate is greatest when the tool operates at high speed.
3. Maintain a 5
˚
to 10
˚
angle between the tool and
5
˚
-10
˚
work surface.
4. Continuously move the tool in a forward and
back motion to avoid creating gouges in the work
surface.
5. Remove the tool from work surface before turning tool off. Allow the tool to stop
rotating before laying it down.
MOUNTING SANDING BACKING PADS
WARNING:
To reduce the risk of serious personal injury, turn tool off and and remove
battery pack before making any adjustments or removing/installing attachments or
accessories.
NOTE:
Guard may be removed when using sanding backing pads
CAUTION:
Proper guard must be reinstalled for grinding wheel, sanding flap disc,
wire brush or wire wheel applications after sanding applications are complete.
1. Place or appropriately thread backing pad (Q) on the spindle.
2. Place the sanding disc (R) on the backing pad (Q).
3. While depressing spindle lock, thread clamp nut
S
Q
R
(S) on spindle, piloting the raised hub on the
clamp nut into the center of san ding disc and
backing pad.
4. Tighten the clamp nut by hand. Then depress
the spindle lock button while turning the sanding
disc until the sanding disc and clamp nut are
snug.
5. To remove the wheel, grasp and turn the backing
pad and sanding pad while depressing the
spindle lock button.
USING SANDING BACKING PADS
Choose the proper grit sanding discs for your application. Sanding discs are available in
various grits. Coarse grits yield faster material removal rates and a rougher finish. Finer
grits yield slower material removal and a smoother finish.
Begin with coarse grit discs for fast, rough material removal. Move to a medium grit
paper and finish with a fine grit disc for optimal finish.
Coarse
16 - 30 grit
Medium
36 - 80 grit
Fine Finishing
100 - 120 grit
Very Fine Finishing
150 - 180 grit
1. Allow the tool to reach full speed before touching tool to the work surface.
2. Apply minimum pressure to work surface, allowing the tool to operate at high
speed. Sanding rate is greatest when the tool operates at high speed.
3. Maintain a 5
˚
to 15
˚
angle between the tool and
5
˚
-15
˚
work surface. The san ding disc should contact
approximately 25.4 mm (1") of work surface.
4. Move the tool constantly in a straight line to prevent
burning and swirling of work surface. Allowing the
tool to rest on the work surface without moving, or
moving the tool in a circular motion causes burning and swirling marks on the
work surface.
5. Remove the tool from work surface before turning tool off. Allow the tool to stop
rotating before laying it down.