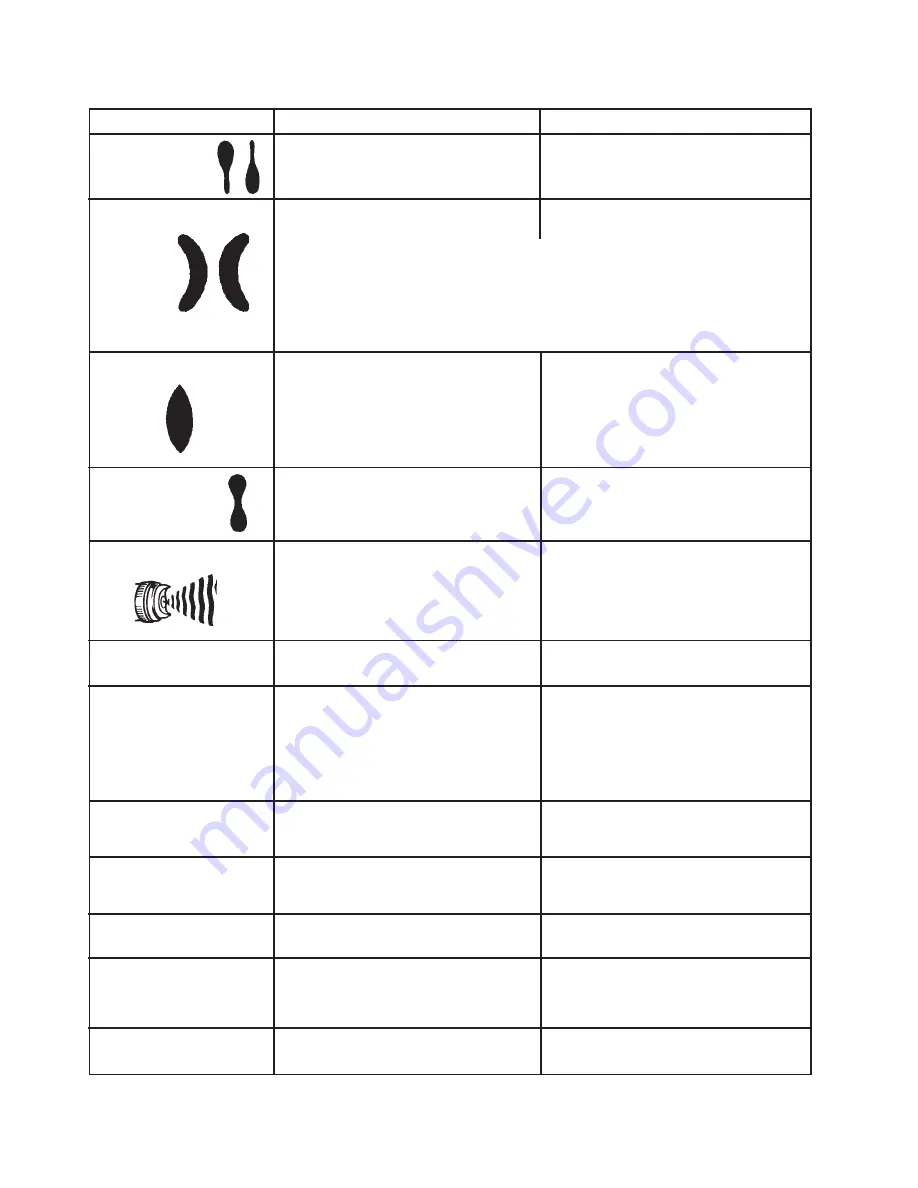
Page 6 SB-2-252-J
TROUBLESHOOTING
CONDITION
CAUSE
CORRECTION
Heavy top or
Horn holes plugged.
Clean. Ream with non-metallic point.
bottom pattern
Obstruction on top or bottom of fluid tip.
Clean.
Cap and/or tip seat dirty.
Clean.
Heavy right or left side
Left or right side horn holes plugged.
Clean. Ream with non-metallic point.
pattern
Dirt on left or right side of fluid tip.
Clean.
Remedies for the top-heavy, bottom-heavy, right-heavy and left-heavy patterns:
1) Determine if the obstruction is on the air cap or the fluid tip. Do this by making a test spray
pattern. Then, rotate the cap one-half turn and spray another pattern. If the defect is inverted,
obstruction is on the air cap. Clean the air cap as previously instructed.
2) If the defect is not inverted, it is on the fluid tip. Check for a fine burr on the edge of the fluid
tip. Remove with #600 wet or dry sand paper.
3) Check for dried paint just inside the opening. Remove paint by washing with solvent.
Heavy center pattern
Fluid pressure too high for atomization
Balance air and fluid pressure.
air (pressure feed).
Increase spray pattern width with spreader
adjustment valve.
Material flow exceeds air cap's capacity.
Thin or lower fluid flow.
Spreader adjustment valve set too low.
Adjust.
Atomizing pressure too low.
Increase pressure.
Material too thick.
Thin to proper consistency.
Split spray pattern
Atomization air pressure too high.
Reduce at transformer or gun.
Fluid pressure too low (pressure feed only).
Increase fluid pressure (increases gun handling
speed).
Spreader adjusting valve set too high.
Adjust.
Jerky or fluttering spray
*Loose or damaged fluid tip/seat.
Tighten or replace.
Material level too low.
Refill.
Container tipped too far.
Hold more upright.
Obstruction in fluid passage.
Backflush with solvent.
Loose or broken fluid tube or fluid inlet nipple.
Tighten or replace.
Dry or loose fluid needle packing nut.
Lubricate or tighten.
Unable to get round spray
Spreader adjustment screw not seating properly.
Clean or replace.
Air cap retaining ring loose.
Tighten.
Will not spray
No air pressure at gun.
Check air supply and air lines.
Internal mix or pressure feed air cap and tip
Change to proper suction feed air cap and tip.
used with suction feed.
Fluid pressure too low with internal mix cap
Increase fluid pressure at tank.
and pressure tank.
Fluid needle adjusting screw not open enough.
Open fluid needle adjusting screw.
Fluid too heavy for suction feed.
Thin material or change to pressure feed.
Starved spray pattern
Inadequate material flow.
Back fluid adjusting screw out to first thread
or increase fluid pressure at tank.
Low atomization air pressure (suction feed).
Increase air pressure and rebalance gun.
Excessive overspray
Too much atomization air pressure
Reduce pressure.
Gun too far from work surface.
Adjust to proper distance.
Improper stroking (arcing, gun motion too fast).
Move at moderate pace, parallel to work surface.
Excessive fog
Too much, or too fast-drying thinner.
Remix properly.
Too much atomization air pressure.
Reduce pressure.
Dry Spray
Air pressure too high.
Reduce air pressure.
Gun tip too far from work surface.
Adjust to proper distance.
Gun motion too fast.
Slow down.
Gun out of adjustment.
Adjust.
Fluid leaking from
Packing nut loose.
Tighten, do not bind needle.
packing nut
Packing worn or dry.
Replace or lubricate.
*Most common problem.