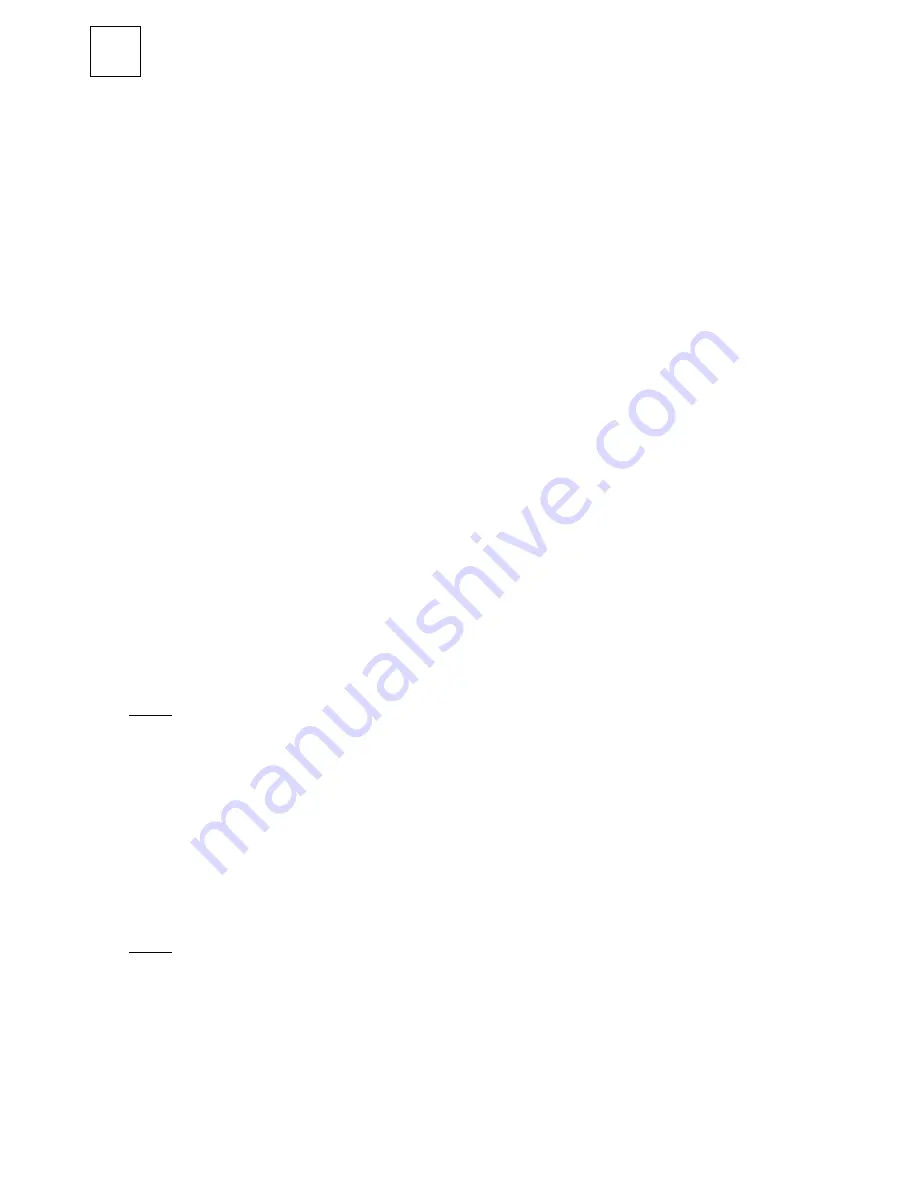
6
© 2007 ITW Finishing Systems and Products
E
INSTALLATION
IMPORTANT:
In order to ensure that this equipment reaches you in first class condition, protective
coatings, rust inhibitors, etc., have been used. Flush all equipment through with a suitable solvent before
use to remove these agents from material passages.
See figures 1 and 2 : Mount gun using the 12.7mm (1/2") diameter hole ‘X’ and secure with screw. An
additional 10mm diameter x 12.5mm deep dowel hole ‘Y’ has been provided to enable users to center
the spray gun with mounting fixtures of their own design.
HOSING
Use separate filtered regulated air supplies for atomizing and cylinder air.
Connect the cylinder air ‘A’ via a control valve. For fast cylinder operation the control valve should be
fitted as close to the gun as possible or an additional quick exhaust valve installed in the line.
Attach atomizing air hose to connector ‘B’
Connect material hose(s) ‘C’ to the spray head. If material re-circulation is not required, remove one of
the connectors and fit plug supplied with the gun.
EARTHING
the Spray gun must be earthed to dissipate any electrostatic charges which may be created
by fluid or air flows. This can be achieved through the Spray gun mounting, or conductive air/fluid hoses.
electrical bond from the spray gun to earth should be checked with an ohmmeter. A resistance of less
than 10
6
Ohms is recommended.
WARNING:
See instructions under “Replacement of Parts”.
Recommended hose sizes up to 10m (34ft) long:
Atomization Air: 8mm ( 5 /16") bore, Cylinder Air: 6mm ( 1 /4") bore, Material: 9.5mm ( 3 /8 ") bore.
OPERATION
See figure 2.
1. Mix, prepare and strain the material to be sprayed according to the paint manufacturers instructions.
Use a lint free mesh to strain the material.
2. Adjust the spray gun controls and atomizing pressure before turning material supply on.
3. Open valves ‘D’ marked FAN and ‘E’ marked ATOM by turning counter-clockwise.
4. To adjust fluid needle for full travel. Close fluid needle adjusting knob ‘F’ clockwise until resistance is
felt, then open by turning 5 to 6 full turns counter clockwise.
5. Regulate cylinder air pressure to 4.5 bar (65lbf/in2).
6. Adjust atomizing air pressure. Start with a regulated pressure of 2 bar (30lbf/in2). Turn on cylinder
air and trigger spray gun with control valve. Increase regulated pressure to achieve 0,7 bar
(10lbf/in²). Turn off atomizing air supply and trigger spray gun to release pressure.
NOTE
: Use pressure test unit or test cap kit to check the atomizing pressure at the cap (See
accessories)
7. Turn on material supply and adjust material pressure to 0.7 bar (10 lbf/in2). See chart 1 for
guidance.
8. Test spray and observe spray pattern. Adjust material or air atomization pressures until the desired
pattern is obtained. If it is not practical to control the material flow by pressure regulation, the fluid
needle adjusting knob has ratchet stops and zero sleeve to aid fine material adjustment by
restricting the fluid needle movement. Close knob by turning clockwise and gradually open using
ratchet stops until the correct material flow is achieved.
9. Other adjustments can be made using the valves marked ‘Fan’ and ‘Atom’. The fan valve will alter
the spray width from full fan to round. ‘Atom’ valve controls the degree of atomization from fine to
coarse.
NOTE
: If the process requires altering the spray width recheck and adjust the air cap atomizing
pressure (See 2.4 above)
PREVENTIVE MAINTENANCE
FLUSHING THE SYSTEM.
1. Turn off atomizing air supply and material supply.
2. Relieve system pressures, open material relief valve and trigger gun into booth or container.
3. Remove air cap.
4. Replace material with a suitable solvent.