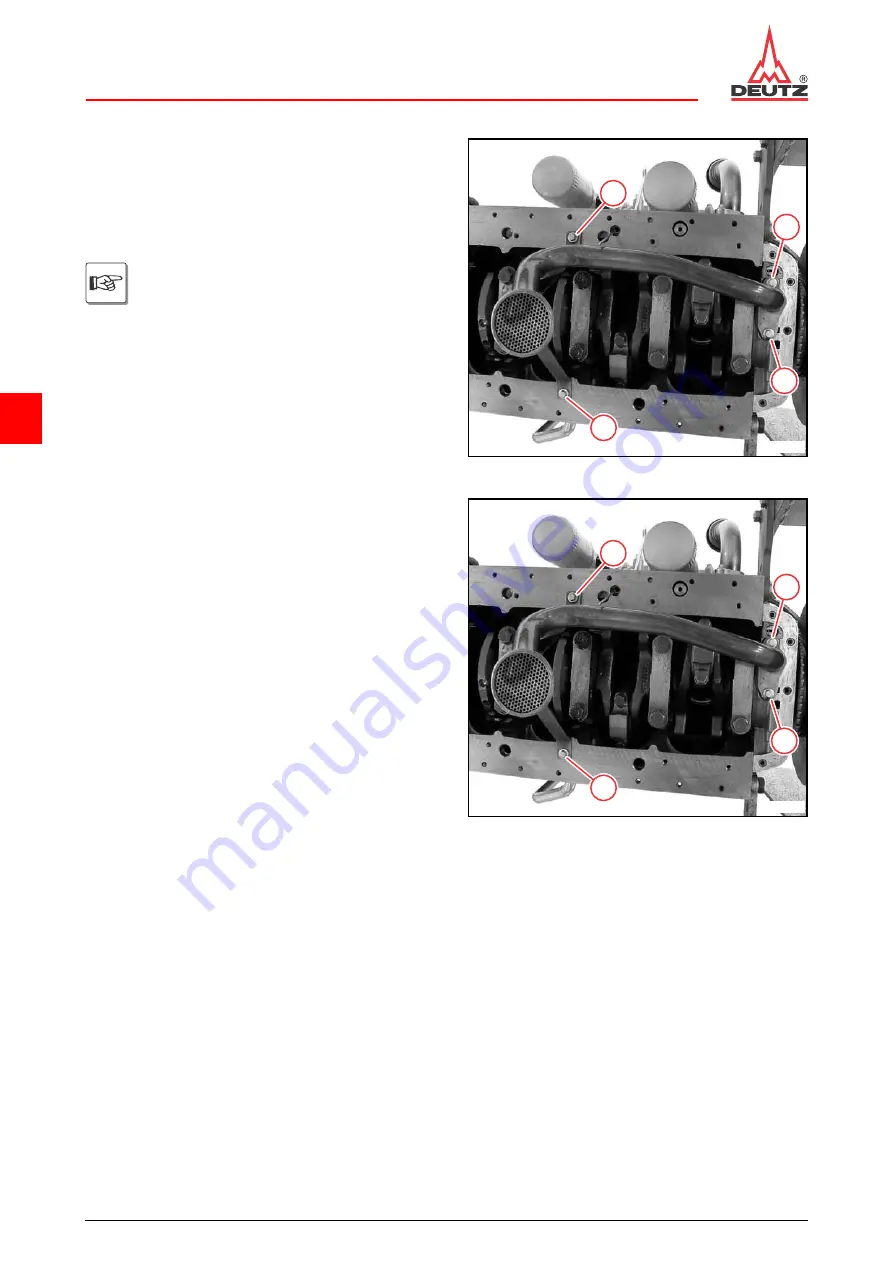
© 02/2010
OBJ_DOKU-21785-001.fm
2/2
6
Oil suction pipe
TCD 2013 2V
W 16-01-01
Installing the oil suction pipe
● Clean sealing surfaces.
● Mount new gasket.
● Mount oil suction pipe.
● Fasten screws.
Ensure that the installation location is free
from faults.
Pay attention to different screw lengths.
M8 x 25 mm (1)
M8 x 20 mm (2)
2
1
1
2
© 44478-0
● Tighten screws (1).
22 Nm
● Install lubricating oil pan.
1
1
1
1
© 44479-0
Summary of Contents for TCD 2013 2V
Page 5: ...02 2010 OBJ_DOKU 21737 001 fm 2 2 DEUTZ engines Table of contents...
Page 6: ...1 05 2005 OBJ_DOKU 21738 001 fm 1 4 DEUTZ engines Foreword 1 Foreword...
Page 7: ...1 05 2005 OBJ_DOKU 21738 001 fm 2 4 DEUTZ engines Foreword...
Page 9: ...1 05 2005 OBJ_DOKU 21738 001 fm 4 4 DEUTZ engines Foreword...
Page 10: ...2 11 2005 OBJ_DOKU 21739 001 fm 1 4 DEUTZ engines General 2 General...
Page 11: ...2 11 2005 OBJ_DOKU 21739 001 fm 2 4 DEUTZ engines General...
Page 13: ...2 11 2005 OBJ_DOKU 21739 001 fm 4 4 DEUTZ engines General...
Page 14: ...3 02 2010 OBJ_DOKU 21740 001 fm 1 8 DEUTZ engines User notes 3 User notes...
Page 15: ...3 02 2010 OBJ_DOKU 21740 001 fm 2 8 DEUTZ engines User notes...
Page 21: ...3 02 2010 OBJ_DOKU 21740 001 fm 8 8 DEUTZ engines User notes...
Page 23: ...4 02 2010 OBJ_DOKU 21741 001 fm 2 18 Technical data TCD 2013 2V Testing and setting data...
Page 31: ...4 02 2010 OBJ_DOKU 21741 001 fm 10 18 Technical data TCD 2013 2V Tightening specifications...
Page 41: ...5 02 2010 OBJ_DOKU 21742 001 fm 2 12 Job card overview TCD 2013 2V Sorted alphabetically...
Page 45: ...5 02 2010 OBJ_DOKU 21742 001 fm 6 12 Job card overview TCD 2013 2V Sorted alphabetically...
Page 47: ...5 02 2010 OBJ_DOKU 21742 001 fm 8 12 Job card overview TCD 2013 2V Sorted numerically...
Page 51: ...5 02 2010 OBJ_DOKU 21742 001 fm 12 12 Job card overview TCD 2013 2V Sorted numerically...
Page 52: ...6 11 2005 OBJ_DOKU 21743 001 fm 1 2 DEUTZ engines Job cards 6 Job cards...
Page 53: ...6 11 2005 OBJ_DOKU 21743 001 fm 2 2 DEUTZ engines Job cards...
Page 57: ...02 2010 OBJ_DOKU 21744 001 fm 4 4 6 Crankcase TCD 2013 2V W 01 01 01...
Page 63: ...02 2010 OBJ_DOKU 21745 001 fm 6 6 6 Front cover TCD 2013 2V W 01 02 01...
Page 79: ...02 2010 OBJ_DOKU 21749 001 fm 4 4 6 Crankcase TCD 2013 2V W 01 07 03...
Page 83: ...02 2010 OBJ_DOKU 21751 001 fm 2 2 6 Crankcase TCD 2013 2V W 01 13 01...
Page 99: ...02 2010 OBJ_DOKU 21754 001 fm 4 4 6 Cylinder liner TCD 2013 2V W 04 01 02...
Page 113: ...02 2010 OBJ_DOKU 21756 001 fm 2 2 6 Torsional vibration damper TCD 2013 2V W 05 02 01...
Page 117: ...02 2010 OBJ_DOKU 21757 001 fm 4 4 6 Flywheel TCD 2013 2V W 05 03 01...
Page 129: ...02 2010 OBJ_DOKU 21758 001 fm 12 12 6 Crankshaft TCD 2013 2V W 05 05 01...
Page 147: ...02 2010 OBJ_DOKU 21761 001 fm 8 8 6 Connecting rod TCD 2013 2V W 06 01 01...
Page 159: ...02 2010 OBJ_DOKU 21763 001 fm 4 4 6 Piston TCD 2013 2V W 07 01 02...
Page 165: ...02 2010 OBJ_DOKU 21764 001 fm 6 6 6 Piston TCD 2013 2V W 07 02 02...
Page 179: ...02 2010 OBJ_DOKU 21767 001 fm 6 6 6 Cylinder head TCD 2013 2V W 08 02 01...
Page 183: ...02 2010 OBJ_DOKU 21768 001 fm 4 4 6 Cylinder head TCD 2013 2V W 08 02 02...
Page 191: ...02 2010 OBJ_DOKU 21769 001 fm 8 8 6 Cylinder head TCD 2013 2V W 08 03 01...
Page 199: ...02 2010 OBJ_DOKU 21771 001 fm 6 6 6 Cylinder head TCD 2013 2V W 08 04 01...
Page 255: ...02 2010 OBJ_DOKU 21784 001 fm 4 4 6 Lubricating oil cooler TCD 2013 2V W 15 02 02...
Page 265: ...02 2010 OBJ_DOKU 21786 001 fm 8 8 6 High pressure pump TCD 2013 2V W 17 01 01...
Page 275: ...02 2010 OBJ_DOKU 21787 001 fm 10 10 6 High pressure pump TCD 2013 2V W 17 01 04...
Page 301: ...02 2010 OBJ_DOKU 21790 001 fm 6 6 6 Fuel filter TCD 2013 2V W 20 01 01...
Page 319: ...02 2010 OBJ_DOKU 21793 001 fm 4 4 6 Fuel pipes TCD 2013 2V W 21 02 03...
Page 325: ...02 2010 OBJ_DOKU 21795 001 fm 4 4 6 Charge air line TCD 2013 2V W 22 01 01...
Page 333: ...02 2010 OBJ_DOKU 21796 001 fm 8 8 6 Coolant pump TCD 2013 2V W 37 03 01...
Page 341: ...02 2010 OBJ_DOKU 21799 001 fm 4 4 6 Thermostat housing TCD 2013 2V W 38 02 01...
Page 361: ...02 2010 OBJ_DOKU 21803 001 fm 6 6 6 Fan console TCD 2013 2V W 39 04 03...
Page 383: ...02 2010 OBJ_DOKU 21808 001 fm 6 6 6 Engine mounting TCD 2013 2V W 46 00 01...
Page 389: ...02 2010 OBJ_DOKU 21809 001 fm 6 6 6 Engine mounting TCD 2013 2V W 47 01 01...
Page 401: ...02 2010 OBJ_DOKU 21810 001 fm 12 12 6 Cable harness TCD 2013 2V W 48 01 01...
Page 407: ...02 2010 OBJ_DOKU 21811 001 fm 6 6 6 Electrical equipment TCD 2013 2V W 48 02 01...
Page 411: ...02 2010 OBJ_DOKU 21812 001 fm 4 4 6 Electrical equipment TCD 2013 2V W 48 02 03...
Page 417: ...02 2010 OBJ_DOKU 21814 001 fm 4 4 6 Electrical equipment TCD 2013 2V W 48 04 01...
Page 423: ...02 2010 OBJ_DOKU 21816 001 fm 4 4 6 Electrical equipment TCD 2013 2V W 48 06 01...
Page 443: ...02 2010 OBJ_DOKU 21821 001 fm 4 4 6 Start aid TCD 2013 2V W 63 01 01...
Page 448: ...02 2010 OBJ_DOKU 21823 001 fm 1 8 7 Standard tools TCD 2013 2V W 49 00 01 7 Standard tools...
Page 456: ...02 2010 OBJ_DOKU 21824 001 fm 1 16 8 Special tools TCD 2013 2V W 49 01 01 8 Special tools...