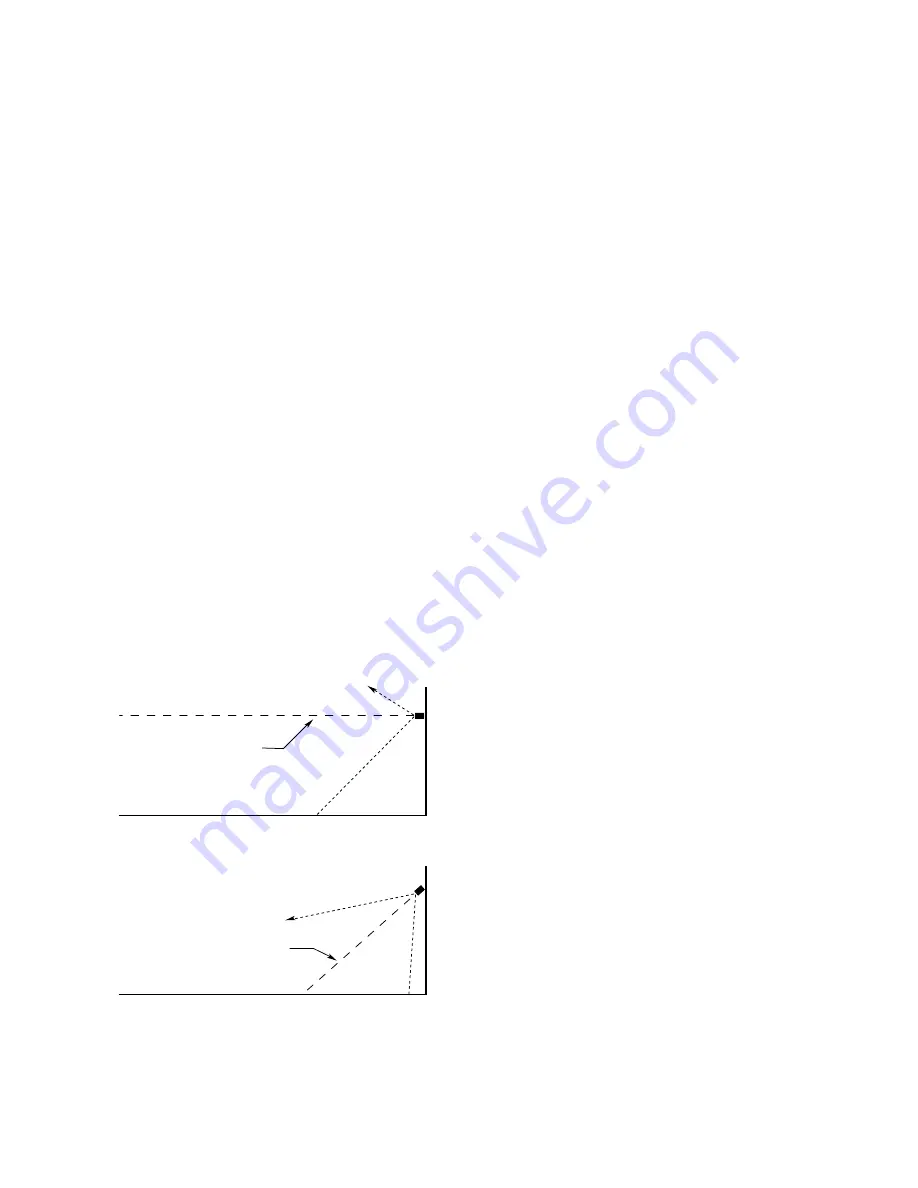
INSTALLATION
DETECTOR POSITIONING
Detectors should be positioned to provide the best
unobstructed view of the area to be protected. The
following factors should also be taken into considera-
tion:
• Locate and position the detector so that the fire haz-
ard(s) are within both the field of view and detection
range of the device. Refer to Appendix A for specific
information.
• Considering the 90 degree cone of vision, use
enough detectors to adequately cover the protected
area with overlapping cones of vision.
• For fastest response time, position the detectors as
close as possible to the anticipated fire source.
• Aim the detector with the anticipated fire source as
close as possible to the central axis of the cone of
vision.
• If possible, conduct actual flame tests to verify cor-
rect detector positioning and proper system opera-
tion.
• Position the detector in a manner that will minimize
the buildup of contaminants on the viewing window
and
oi
ring. Substances such as snow, ice, dirt, oil,
paint overspray and numerous other commonly
encountered materials are capable of attenuating
UV or IR radiation and adversely affecting detector
response.
• For outdoor applications, the detector should be
aimed downward at least 10 to 20 degrees to prevent
it from scanning the horizon. This minimizes response
to distant UV sources outside the protected area. See
Figure 1.
• The detector should not be placed where smoke
can obscure its view of the hazardous area. For
indoor applications, if dense smoke is expected to
accumulate at the onset of a fire, mounting the
detector on a side wall a few feet (1 meter) down
from the ceiling will normally allow enough time for
the unit to respond before it is affected by rising
smoke.
WIRING REQUIREMENTS
• Use 16 to 22 gauge (1.5 to 0.5 mm
2
) cable.
• A minimum input voltage of 18 vdc must be present
at the detector.
• Use cable that is suitable for the installation environ-
ment (harsh environments require specially made
cable).
• Shielded cable is highly recommended to protect
against interference caused by extraneous electri-
cal “noise.” Foil type shielded cable is recommend-
ed to protect from electromagnetic and radio fre-
quency interference. When using cables with
shields, the shield should be insulated at the detec-
tor and grounded only at the control cabinet.
• When cable is installed in conduit, the conduit
should not be used for wiring to other electrical
equipment.
• When cable is installed in conduit, the use of con-
duit seals is required to prevent damage to electri-
cal connections caused by condensation within the
conduit. These seals must be watertight and explo-
sion-proof and are to be installed even if they are
not required by local wiring codes. A seal must be
located as close to the U7652 as possible. In no
case should this seal be located more than 18 inch-
es (46 cm) from the unit. If a conduit swivel is used,
the seal must be located between the swivel and
the detector. When an explosion-proof installation is
required, an additional seal must also be installed at
any point where the conduit enters a non-hazardous
area.
• When cable glands are used, water-proof seals
must be fitted between the housing and the gland.
• Position the detector so that the conduit opening is
at the bottom or at either side of the device.
• Whenever possible, slope the conduit run down-
ward from the detector. Do not use conduit runs
that enter the device from the top. Refer to Figures
2 and 3.
5
95-8385
CENTER AXIS
OF DETECTOR
FIELD OF VIEW
CENTER AXIS
OF DETECTOR
FIELD OF VIEW
INCORRECT
CORRECT
NOTE: DETECTOR MUST ALWAYS BE AIMED
DOWNWARD AT LEAST 10 TO 20 DEGREES.
B1974
Figure 1—Detector Orientation Relative to Horizon