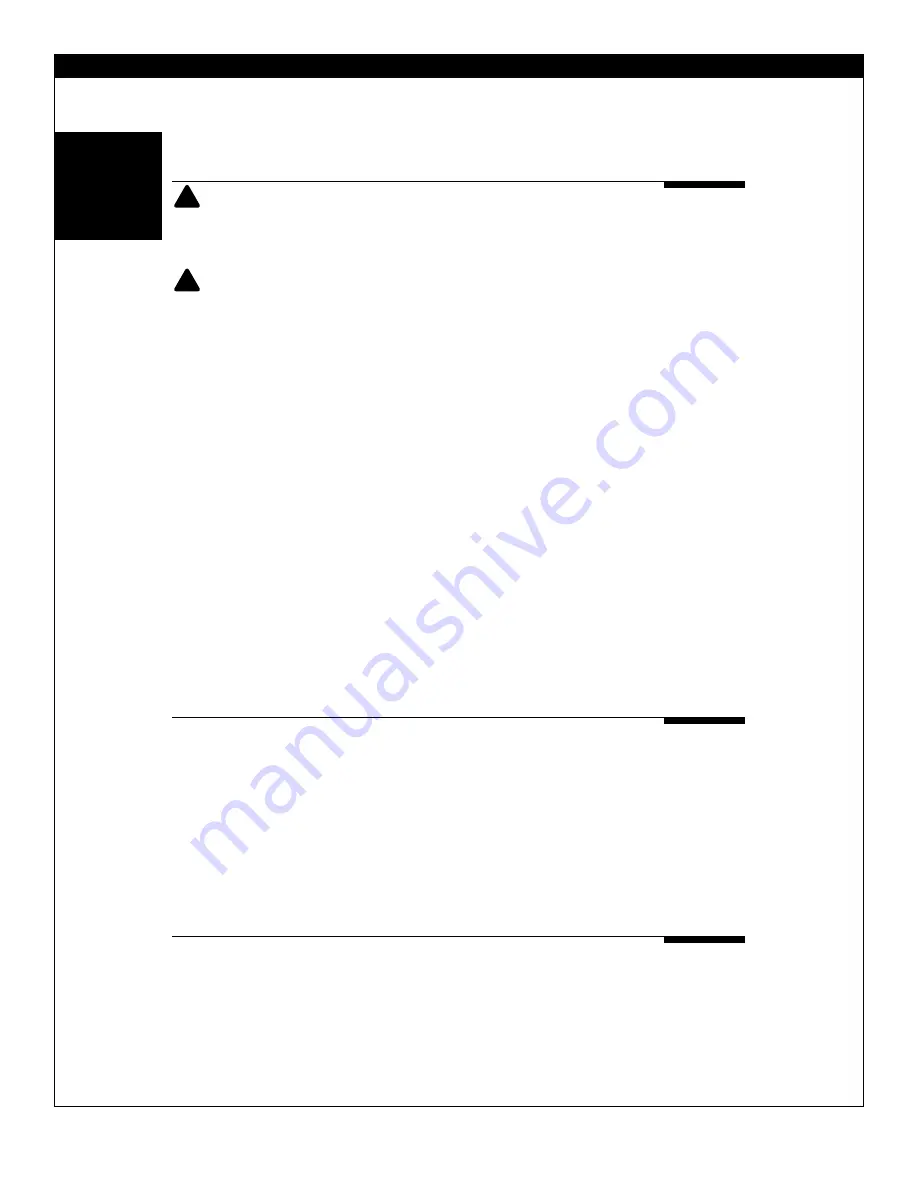
11
V E N T - F R E E G A S H E A T E R S E R V I C E M A N U A L
6
S E C T I O N
!
WARNING ICON
G 001
Testing Heater Gas Connections
1.
Remove the front panel of the heater by
removing the two screws near the bottom
corners and pulling the bottom of the panel
forward and then downward. Turn heater
control knob to the “OFF” position. Open
the manual shut-off valve (see Figure 8,
page 9). Apply solution of liquid detergent
and water to all connections from the supply
line to control valve. Bubbles forming indi-
cate leaks that must be corrected.
2.
Light the heater and check all remaining
internal connections for leaks with the liquid
detergent and water solution.
Correcting Leaks
1.
To correct a leak on flared tubing, first try
tightening the connection. If this doesn’t
work, reflare or replace the section of tub-
ing.
2.
On threaded piping, try tightening or re-
doping first. If the leak continues, take the
connection apart and inspect the threads. If
necessary, cut new threads or replace the
section of piping.
3.
If steps 1 and 2 fail to correct the problem,
look for pinholes in the pipe or fittings and
check for splits in the tubing. Replace ma-
terials or fittings that are defective.
Testing Gas Supply Line Connections
WARNING: All gas piping and connec-
tions must be tested for leaks after installation or
servicing. All leaks must be corrected immedi-
ately.
WARNING: NEVER USE AN OPEN
FLAME TO CHECK FOR A LEAK. Apply a
solution of liquid detergent and water to all
connections. The formation of bubbles indicate
leaks that must be corrected.
Pressure Testing Supply Line
1.
The heater and its control valve must be
disconnected from the gas supply piping
system during any testing of the gas supply
piping system when test pressures are in
excess of 14" W.C. (1/2 PSIG).
2.
The heater must be isolated from the gas
supply piping system by closing its individ-
ual manual shut-off valve during any pres-
sure testing of the gas supply piping system
when pressures are equal to or less than
14" W.C. (1/2 PSIG).
TEST PROCEDURES
Testing Gas Supply Piping System
1.
Inspect all connections from the gas supply
to the manual shut-off valve to be sure they
are tight or closed.
2.
Connect a low pressure gauge to the 1/8
inch NPT pressure tap (see
“Equipment”,
page 7). The manual shut-off valve should
be closed.
3.
Open the gas supply service valve to pres-
surize the system. Close the service valve
tightly.
4.
The low pressure gauge should read at
least 11 inches W.C. Bleed off pressure by
slowly opening the manual shut-off valve
to vent enough gas to reduce the pressure
to exactly 10 inches W.C.
5.
If the pressure remains at 10 inches W.C.
for 10 minutes, you can assume the gas
supply system is leak tight. If the pressure
drops, apply a solution of liquid detergent
and water to all connections and observe
carefully for forming and expanding bubbles.
Bubbles forming indicate a leak that must
be corrected.
!
WARNING ICON
G 001