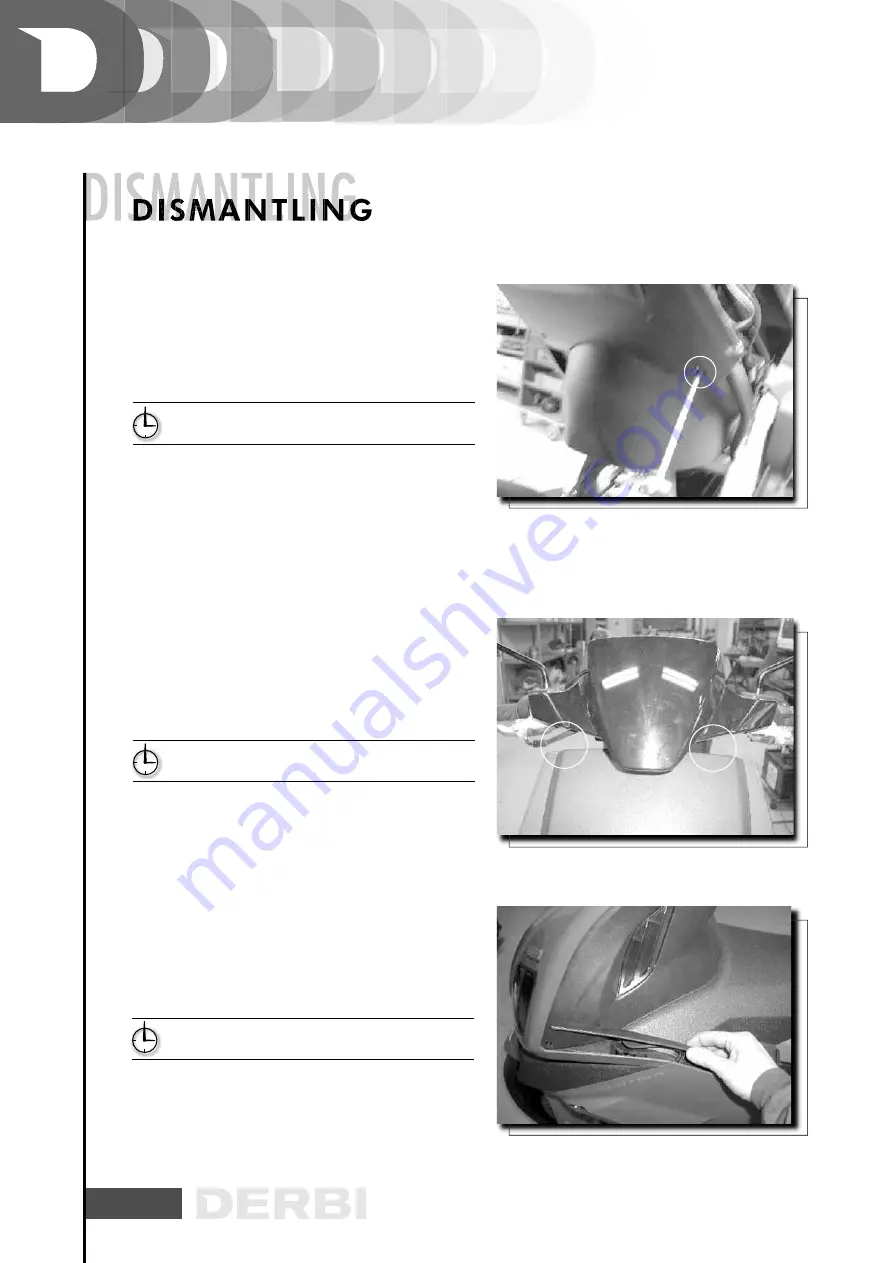
36
3. LOWER COWLING COVER
• Extract the 2 securing screws (Philips 6x16 with was-
her)
Time taken:
17 Minutes
N.B.
TO CONTINUE WITH THE HELMET HOLDER WE NEED
TO CONTINUE DISMANTLING THE FRONT PART, SIN-
CE THE PETROL TANK FRONT BREATHER PIPE PASSES
THROUGH THE HELMET HOLDER.
4. WATER-OIL TANK COVER
• Extract the 2 top screws (Philips 5x12).
Time taken:
19 Minutes
5. SIDE COVERS
• Pull them gently backwards.
Time taken:
20 Minutes
Summary of Contents for GP1 50 cc
Page 1: ...GP1 50 cc WORKSHOP MANUAL...
Page 3: ......
Page 128: ...127...
Page 138: ...created by w w w ciandisseny com...