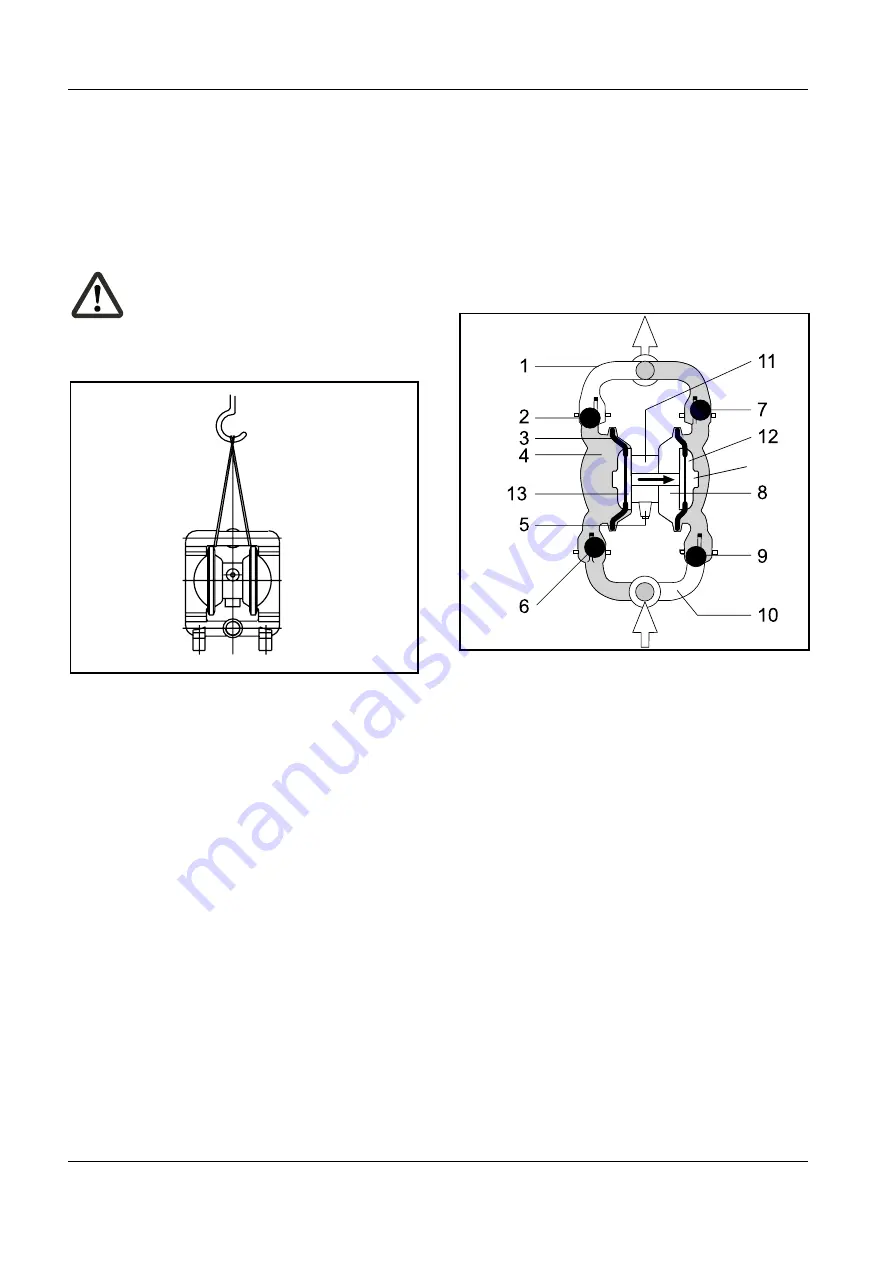
12
DEPA
®
Air Operated Diaphragm Pumps
n
Fasten the lifting tackle so that the
pump can be safely lifted.
n
For pumps DH40-TP/TPL please use
the corresponding lifting eye. For pumps
DH50-TP/TPL please use the available
notches.
Danger!
In order to avoid slipping of the
sling the rope must be crossed
over at the hook (Fig. 1).
Fig. 1: Transport of pump
Be careful when unpacking the pump and
proceed as follows:
■
Check the packaging material for trans-
port damage.
■
Take the pump carefully out of the pack-
aging material.
■
Check the pump for visual damage.
■
Remove the plugs from all pump ports.
■
Check seals and fluid lines for damage.
The following points must be strictly ob-
served when preparing the pump for stor-
age:
1 Discharge manifold
2 Top valve ball
(closed during suction)
3 Diaphragm
4 Pump chamber
5 Silencer
6 Bottom valve ball
(opened. Medium flows into chamber)
7 Top valve ball
(open. Product is pressed out)
8 Air chamber
(the drive air displaces the medium
via the diaphragm and at the same time
pulls back the second diaphragm)
9 Bottom valve ball
(closed during delivery)
10 Suction socket
11 Air control unit
12 Outer piston
13 Inner piston
14 Diaphragm, in the case of nopped E4
®
without outer diaphragm plate
Fig. 2: Design of pump
■
Store the pump in a dry place.
■
Thoroughly clean used pumps before
storage.
■
Do not subject stored pumps to ex-
treme temperature fluctuations.
1.3
Principle of function
14