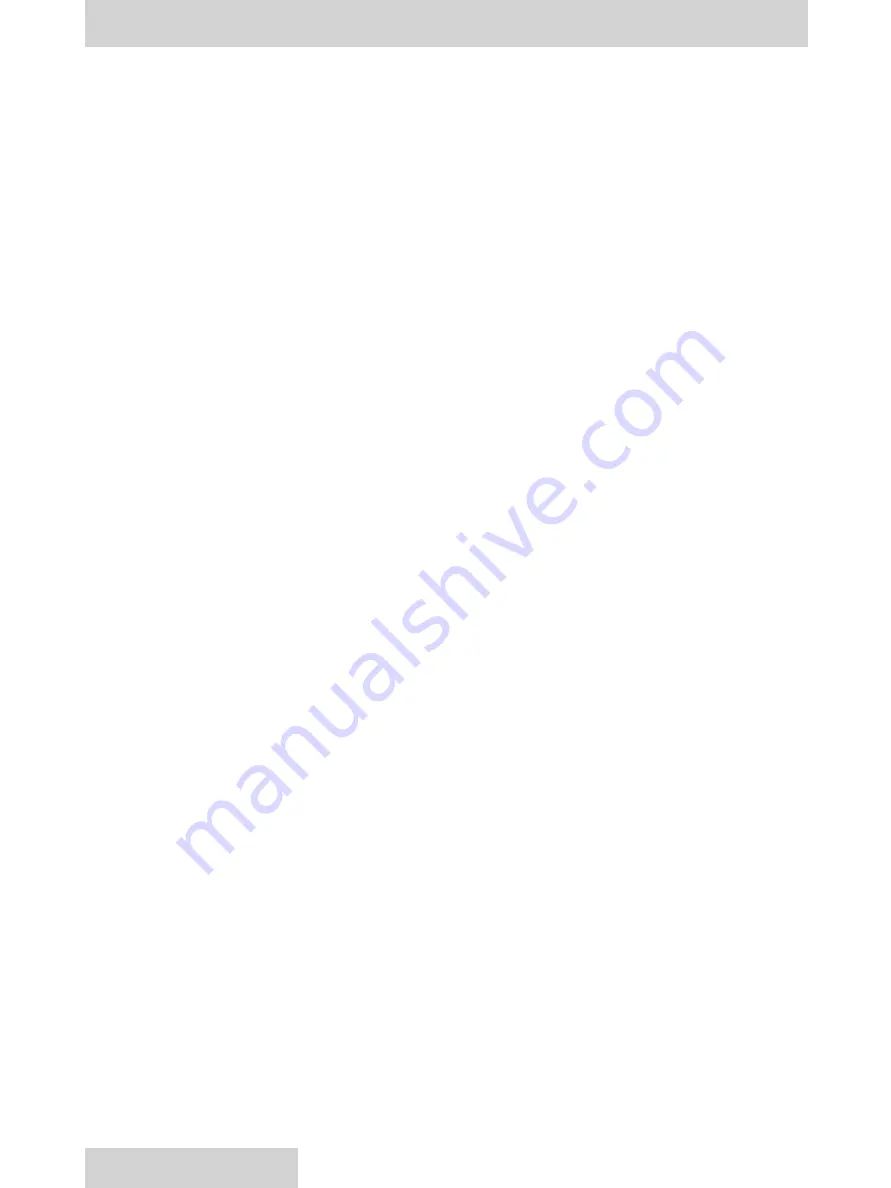
1.
Install gages on system pressure and on compensator vent ports.
2.
Turn compensator adjustment screw out to remove spring load, then 1/2 turn in.
3.
Turn differential adjustment screw out to remove spring load, then 1/2 turn in.
4.
Back out maximum volume stop to full volume.
5.
For setting and testing compensator override function, disable torque limiter in this
manner: Back out primary adjusting screw (15) figure 8, to remove all load. Turn in outer
adjusting screw (8) to go solid. Caution! do not apply over 1,2 Nm torque to avoid damage
to internal parts!
6.
Start prime mover with system relief set at 35 bar.
7.
Stroke pump to full displacement. Apply a load to the pump.
8.
Increase system relief valve until compensator de-strokes pump to zero displace-
ment. Set compensator to 103 bar.
9. Adjust compensator differential spool pressure to 13,8 bar. This is accomplished by
adjusting the differential screw until the difference in pressure readings between the sys-
tem pressure and compensator vent gages installed in the compensator cap is 13,8 bar.
(It may be necessary to change differential to gain stability. Use caution when exceeding
17 bar to avoid spring going solid, preventing compensator action.)
10. Set the compensator to 207 bar, 414 bar, and 500 bar. At each condition, increase the
system pressure until the pump fully de-strokes. At no time should the system pressure
vary more than 10,3 bar from the compensator setting. The control should be steady and
stable at all conditions.
11. Reduce pressure to 10,3 bar below the compensator setting. Pump should return to
full stroke. Repeat two or more times. Compensator setting should be repeatable.
12. Set compensator adjustment to at least 34,5 bar above the required setting, or 483
bar.
Set the torque limiter by using the formula:
kW = P• Q/(Eff. • 600)
where P = pressure in Bar
Q = flow in l/m
calculate these two values:
a.
System pressure at full pump flow.
b.
Pump flow at full system pressure.
13. Set system relief valve to pressure (a) calculated above. Back out primary adjusting
screw to remove all load. Set outer adjusting screw (8) so that pump just commences to
de-stroke.
14. Set the system relief valve to the required maximum system pressure. Set primary
adjusting screw (15) to obtain the calculated flow (b) at full system pressure.
15. Set compensator adjustment to the required setting, or 414 bar if not otherwise noted.
Note: Electric motor current may be used instead of calculated flows to set power. In step
13, set the outer adjusting screw (8) to achieve the rated motor current. In step 14, set
the adjustment (15) to achieve the rated motor current.
TORQUE LIMITER OVERRIDE
TEST AND ADJUSTMENT
19
www.comoso.com