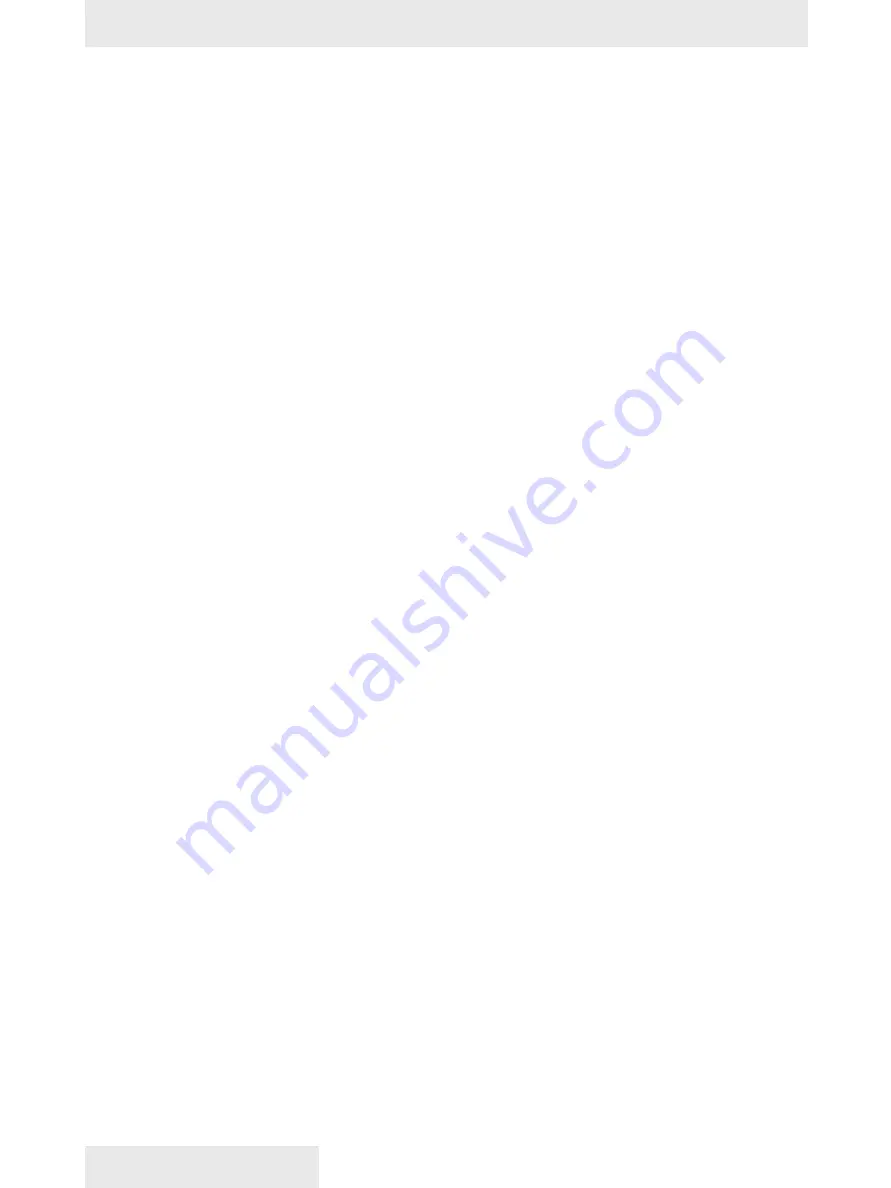
28
Position valve block gasket (29) on valve block. Take care that none of the gasket is cov-
ering the valve seats.
a. Position retainer plate (42) with O-ring grooves facing up, over valve block gasket.
Install four button-head cap screws (43), torque to 30 in.-lbs. (3.39 Nm).
b.Turn the assembly over so that it is resting with the retainer plate O-ring side down-
ward.
Place spring (33) (1.43" long) (36.3 mm) into poppet (30) and insert small hole end first
into outer-most bores at each end of the valve block (25).
Insert three poppets (31) and one poppet (34) in remaining bores as shown, small diam-
eter end first.
Slip springs (33) into poppets (34) and (30) as shown.
Insert two springs (35) (1.09" long) (27.7 mm) into remaining outer poppets (31).
Install spring (32) 1.56" long (39.6 mm) into remaining poppet located in center of valve
block.
Install four orifice plugs (3) in valve block (25) and tighten in place.
Thread pilot replenishing relief valve (36) into block (25). Valve must not extend below
lower surface of retainer plate.
Place O-ring (4) onto seat (5) and install in valve block cover (1). (Be careful not to dam-
age bore in seat.) Torque (5) to 15 ft.-lbs. (20.4 Nm). (Do not use impact wrench).
Lubricate O-ring (11) and insert into groove of seal piston (10) and slip spring (12) onto
end of seal piston and press into bore of housing guide (8).
a. Lubricate O-ring (9) and install on housing guide (8).
b. Place shank of cone (13) into spring (12).
c. Align cone with seat in valve cover and thread housing guide into bore and tighten
in place.
Thread nut (7) on soc. setscrew (6) and thread into housing guide (8) until it starts to
compress spring. Thread acorn nut (45) on soc. setscrew (6).
Coat check valve (2) threads with loctite removable thread locker #242 and thread into
end of valve cover (1). (Be sure check valve is properly installed and does not block pas-
sages from orifice plug (3). Lubricate O-ring (22) and install on plug (23) and tighten.
Repeat above step at the opposite end of the valve cover (1).
Disassemble the strainer assembly (14) in valve block and reassemble per the following:
a. Install the orifice screw of strainer assembly (14) into valve cover. Thread elastic stop
nut onto the orifice screw and torque to 23 in.-lbs. (2.6 Nm).
b. Install the strainer support, filter screen and #6-32 x 1/4 lg. screw. Torque #6-32
screw to 13 in.-lbs. (1.47 Nm).
Place O-ring (37) and two (2) O-rings (47) into the grooves on the upper surface of the
valve block and secure with vaseline or grease.
Place valve cover (1) over valve block (25) positioning over springs (33), (32) and (35)
and secure in place with four (4) socket hd. cap screws (41).
Lubricate O-ring (22) and install on plug (23) and tighten in place.
Lubricate O-ring (19) and install over plug (20) and tighten plug in place.
Lubricate O-rings (47) and install in underside of manifold block (15). Carefully, place
manifold block (15) on top of the valve cover (1) making sure the O-rings are correctly
seated. Secure with four (4) soc. hd. cap screws (41) by threading into valve block (25).
Insert spring (16) and spool (38) into manifold (15) with the spring guide and spring
towards the left side of the manifold (15) when viewing from the top rear.
Install temporary plugs (49) and (50) in 1/2" tube and 1/4" tube ports, front and back and
side. Insert O-ring (19) and plug (20) in alternate drain port.
VALVE BLOCK
for special mounting of servo valve
before 7-93 (continued)
ASSEMBLY PROCEDURES