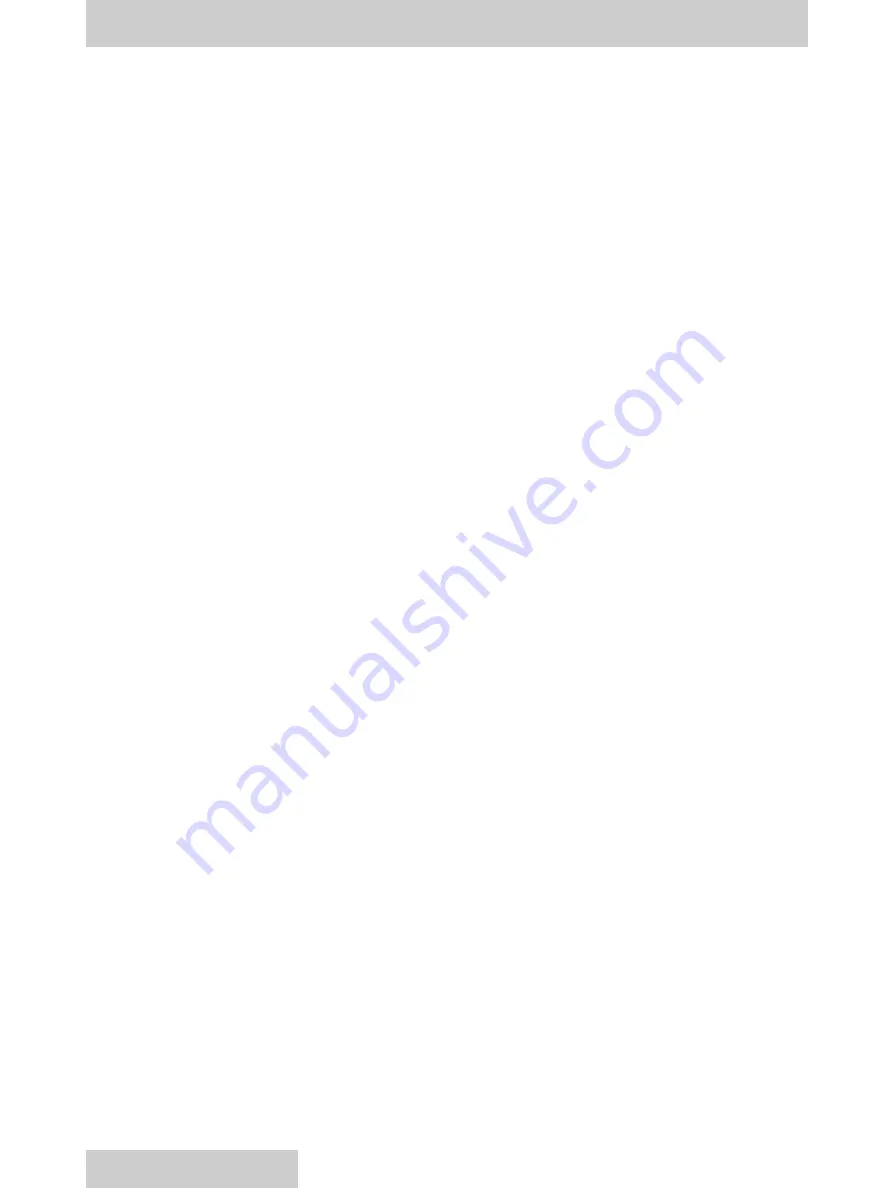
NOTE: Prior to assembly of reconditioned parts, check finish of gasket surface
on valve block and retainer. Must have 60 rms finish with no grinding marks
which might carry oil to outside surface. If lapping is necessary, check depth
of pockets for valve seats after lapping. Must be .085”, 2,16 mm minimum after
lapping to provide clearance for valve seats.
NOTE: Do not use impact tools or over tighten threaded parts.
Wash and dry all parts. During assembly, lapped and ground surfaces should be kept
lubricated with clean oil and protected from nic ks or surface damage.
Place valve block (1) with the six poppet valves bores up in order to press tw o roll pins
(26) in position. Roll pins to be .12”, 3,04 mm belo w surface of valve block. (Not
required after 8-96).
Install four orifice plugs (3) into valve block (1) and tighten in place.
Disassemble the strainer assembly (14) and reassemble per the following steps:
Install the orifice screw of the strainer assembly into valve block. Thread elastic stop
nut onto the orifice screw and torque to 23 lbs-in., 2,6 Nm.
Install clean filter screen on strainer support and secure in place with soc ket head cap
screw, 6-32 X 1/4” lg. Torque #6-32 screw to 13 lbs-in., 1,47 Nm.
Place valve block with poppet valve bores facing up. Position gasket (29) on valve
block.
Place springs (33) 1.43”, 36,32 mm lg. into outer most bores at each end of the v alve
block. Place sequence poppet (30) over these springs. Position seats (27) small
shoulder side first over poppets.
Place springs (35) 1.09”, 27,68 mm lg. into bores next to the sequence poppet valves
of two steps previous. Place dual relief poppet (31) over these springs. Position seats
(28) with the groove side facing up, over poppets.
Place spring (32) 1.56”, 39,6 mm into bore ne xt to compensator valve side of block.
Install replenish poppet over spring. Position seat (28) with the groove side facing
down, over poppet.
Insert spring (33) 1.43”, 36,3 mm into the remaining bore . Place servo poppet (34)
over the retainer and spring. Position seat (44) with the tapered bore f acing down, over
poppet.
Carefully position the retainer plate over seats and poppets. Pressing with one hand
on the valve block, compress seats, poppets and springs far enough to alternately
thread two button head cap screws (43) in far enough to hold the retainer plate . Install
the other two screws and alternately tighten screws. Torque to 30 lbs-in., 3,39 Nm.
Lubricate o-ring (4) and install on to seat (5), thread seat in v alve block. Be careful not
to damage bore in the seat. Torque to 15 lbs-in., 20,34 Nm.
Apply vaseline to shank of cone (13) and install spr ing (12) on cone. Carefully insert
cone and spring into valve block positioning point of cone into bore of seat.
Lubricate o-ring (11) install in groove of piston (10) and inser t end of piston into spr ing
(12).
Lubricate o-ring (9) and install on housing guide (8) and thread into v alve block.
Tighten in place.
Thread nut (7) on socket set screw (6) and thread screw into housing guide (8) until it
starts to compress spring.
Using a small bladed screw driver, thread the pilot replenishing relief valve assembly
(36) into valve block and lightly tighten in place. Do not over tighten. Over tightening
can cause sides of slot to break no w or at next removal.
Lubricate o-ring (4) and install on plug (25) and tighten plug in place .
Thread check valve (2) into valve block and lightly tighten in place. Do not over tighten.
Lubricate o-ring (22) and install on plug (23) and tighten in place . Repeat step on other
end of valve block.
ASSEMBLY PROCEDURE
VALVE BLOCK ASSEMBLY FOR
SERVO VALVE MOUNTING
Figure 13
33
www.comoso.com