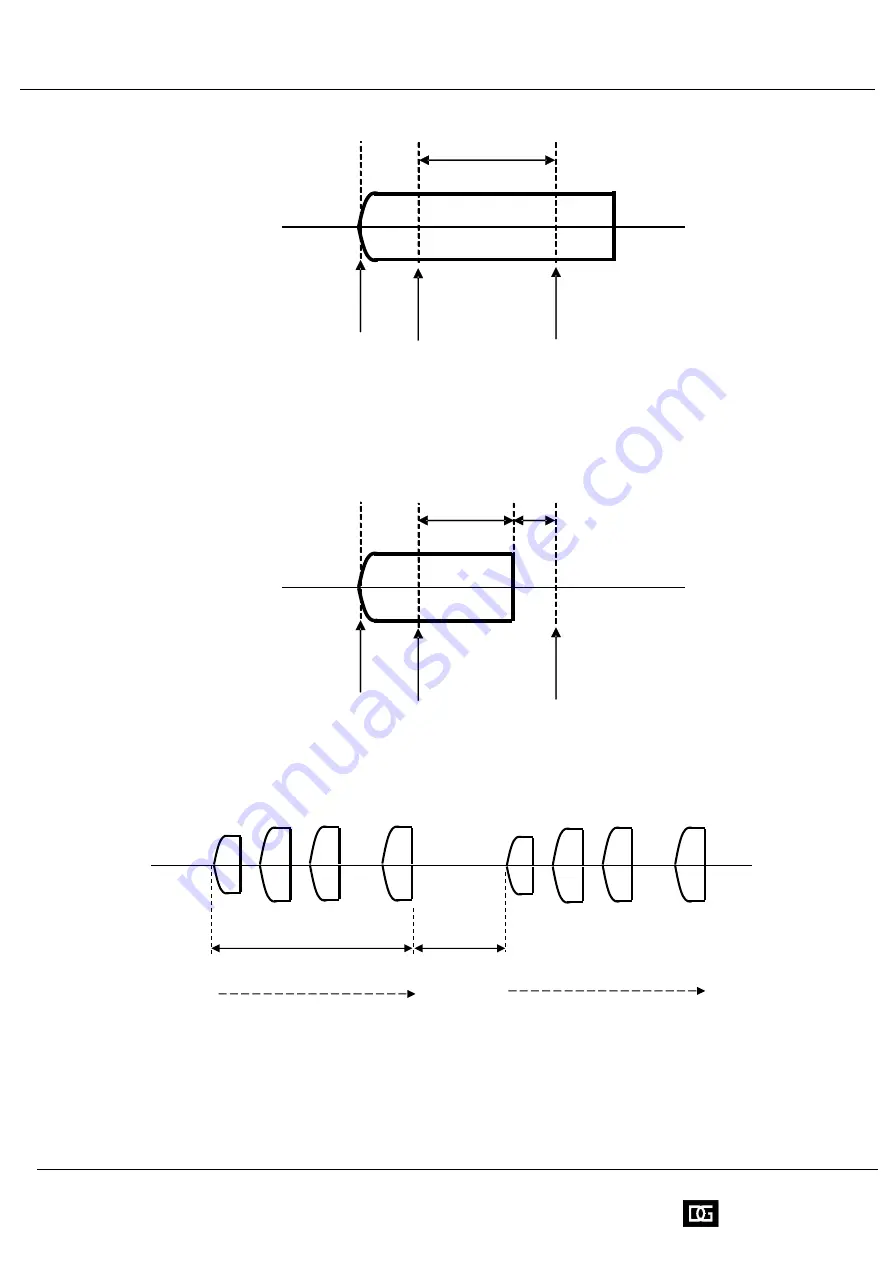
20
DENGENSHA
(b) Multi mode
Maximum measurement time is 99 cycles including pulse and cool time, and any
number of pulse is available as one weld.
When measured cool time is longer than [Sep cool]setting, next pulse is considered as
next weld.
Measuring weld
next weld
cool
to 99cyc
Detect weld
[FIRST]
cyc set
Count start
Displays the average
value during this period
Detect weld
Count start
This is ignored
during this period
Displays the average
value during this period
[LAST]
cyc set
[FIRST]
cyc set
[LAST]
cyc set
Summary of Contents for WS-100
Page 2: ......
Page 3: ......
Page 7: ...v DENGENSHA ...
Page 36: ...DENGENSHA Memo ...
Page 37: ...DENGENSHA Memo ...
Page 38: ...DENGENSHA Memo ...