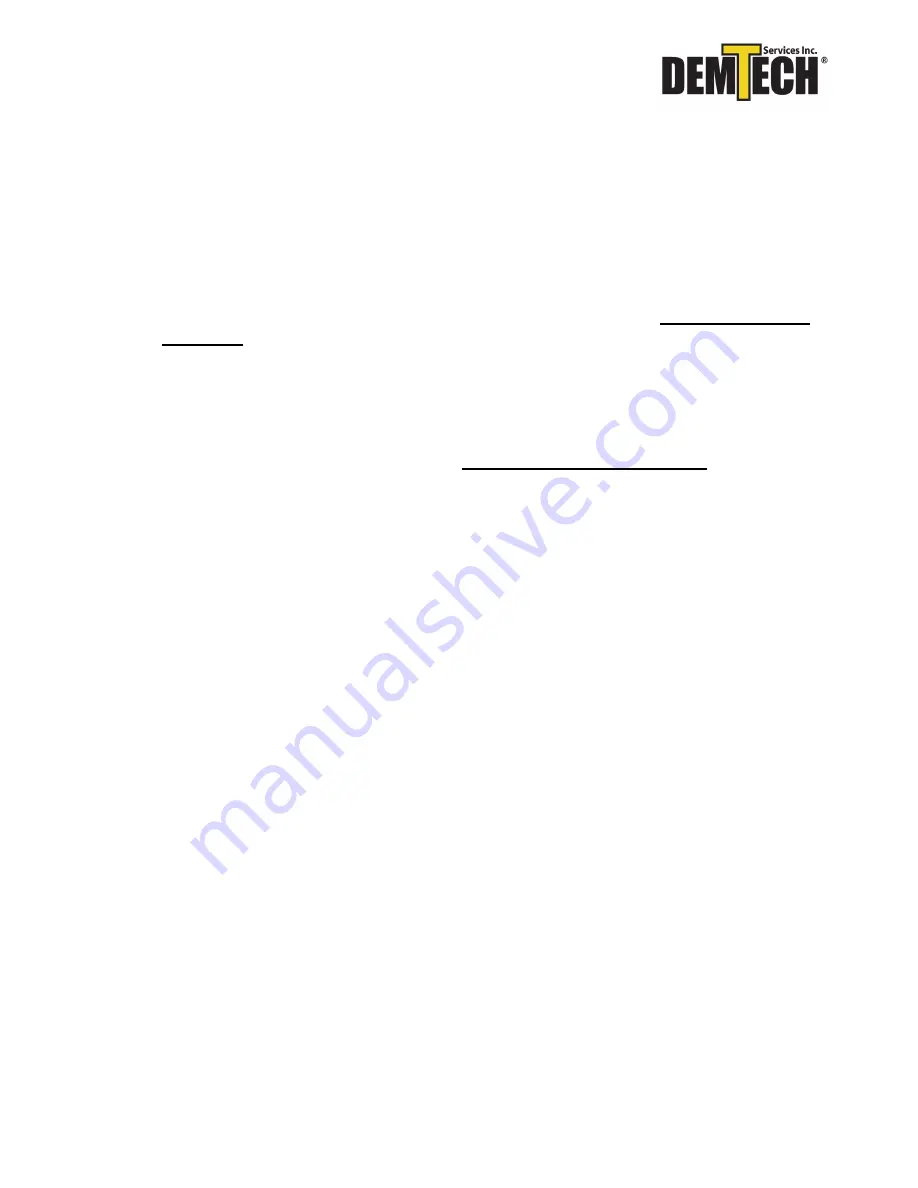
Rev. D, January 2021
Pro-Wedge XL Operator’s Manual
Page 5
6
Unpacking, Power Connection, and Accessories
6.1
Unpacking
Before opening the shipping/storage case for the first time and unpacking the welder,
inspect the outside of the case thoroughly for any signs of mishandling or damage during
shipping. Report any damage to the shipping carrier immediately and
do not proceed with
unpacking
. You should consult your administration concerning claims for shipping
damage. Please notify DEMTECH Services, Inc. or your authorized DEMTECH
distributor where the product was purchased in the event of any shipping damage.
Unlatch and open the shipping/storage case lid and inspect inside the case and equipment
thoroughly for any signs of mishandling or damage during shipping. Report any damage
to the shipping carrier immediately and
do not proceed with unpacking
. You should
consult your administration concerning claims for shipping damage. Please notify
DEMTECH Services, Inc. or your authorized DEMTECH distributor where the product
was purchased in the event of any shipping damage.
The Pro-Wedge hot wedge welder is delivered to you in a sturdy, reusable
shipping/storage case. The custom foam insert protects the unit from damage during
shipping and should be stored in the case at all times when not in use. When the unit
is out of the case, make sure the lid is closed to avoid dirt, dust and rain from getting
inside. Once the Pro-Wedge has been removed from the case, it is ready for use except
for any necessary set-up adjustments. For set-up procedure, refer to the set-up adjustment
section in this manual.
Make note of the orientation of the equipment and packing foam inserts inside the shipping
case to facilitate any repackaging requirements in the future. To avoid injury and/or
damage to the welder, be sure to use adequate care when lifting, removing or replacing the
welder into the shipping/storage case. The welder must be removed from the
shipping/storage case and placed in an appropriate location suitable for the welding you
intend to perform.
6.2
Electrical Plug Connection
The Pro-Wedge is supplied with an appropriate U.S. plug-end according to the specified
operating voltage of the welder. The supplied plug-end can be replaced by the customer
as long as the new one is rated at a minimum of 20 amps.
Summary of Contents for 500-0100/XL/A
Page 1: ...Pro Wedge XL Operator s Manual Model Number 500 0100 XL A Revision D...
Page 13: ...Rev D January 2021 Pro Wedge XL Operator s Manual Page 10 Figure 1 4 3 4 1 2...
Page 25: ...Rev D January 2021 Pro Wedge XL Operator s Manual Page 22 Figure 8 2 1...
Page 27: ...Rev D January 2021 Pro Wedge XL Operator s Manual Page 24 9 1 Appendix A Diagram 5...